ITALIA: El hogar de la pasta es también la sede de las salsas sostenibles. Desde la planta Rubbiano de Barilla, en el corazón del distrito de comida de Parma, más de 150 millones de frascos de salsa para pasta preparada salen cada año para las mesas de todo el mundo. Una expansión de la planta completada en 2019 utiliza más de 400 motores de engranajes y accionamientos descentralizados de Danfoss para reducir la complejidad, optimizar el espacio y minimizar la huella de carbono.
Las líneas de producción se han construido de acuerdo con los más altos estándares de seguridad y respeto por el producto y las personas. La planta de Rubbiano está equipada con soluciones de automatización de última generación, utilizando las mejores tecnologías del mercado y el amplio conocimiento de Barilla en integración de fábrica y gestión de recursos de fabricación.
Una de las distinciones de la planta de Rubbiano es la compleja arquitectura de sus líneas de envasado, las cuales han sido organizadas para brindar la máxima flexibilidad. El complejo sistema transportador se utiliza para mover los frascos entre las máquinas y sistemas en el área de empaque, tanto para clasificar los diferentes flujos de productos semiacabados sin etiquetar entre las máquinas como para preparar el producto terminado y etiquetado para su envío.
El ingeniero de Barilla Mauro Ruozi explica:
“Dado que el sistema de transporte es muy articulado, realizamos un estudio en profundidad sobre los componentes (motores y accionamientos) más adecuados para lograr los objetivos de flexibilidad y eficiencia que nos habíamos propuesto. Al tener que construir un sistema con cientos de motores para dar servicio a los muchos transportadores, hubo muchos aspectos a considerar: eficiencia energética, simplicidad de cableado, espacio requerido en el sitio y por paneles eléctricos, mantenimiento rápido, facilidad de limpieza e integración en la red de la fábrica."
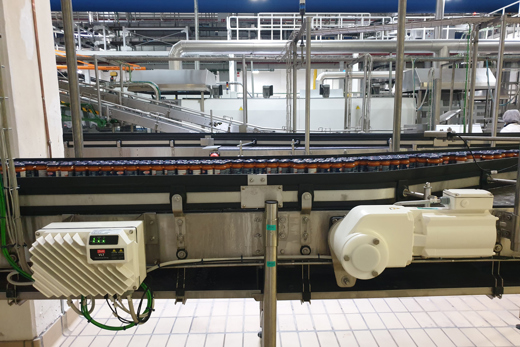
Barilla decidió adoptar una arquitectura basada en motorreductores inteligentes distribuidos a lo largo de todo el sistema de transporte del área de empaque e integrado en la red de control de la fábrica.
Danfoss VLT® FlexConcept® demostró ser la opción ganadora. Es un sistema descentralizado (campo) que combina el motor de engranajes VLT® OneGearDrive® de alta eficiencia y el variador de alto rendimiento VLT® Decentral Drive FCD 302.
Más de 400 motorreductores y accionamientos descentralizados se distribuyen a lo largo de todo el transportador. Debido a que están montados directamente sobre el propio transportador, el cableado se simplifica significativamente, reduciendo notablemente el espacio ocupado en la línea por los paneles eléctricos.
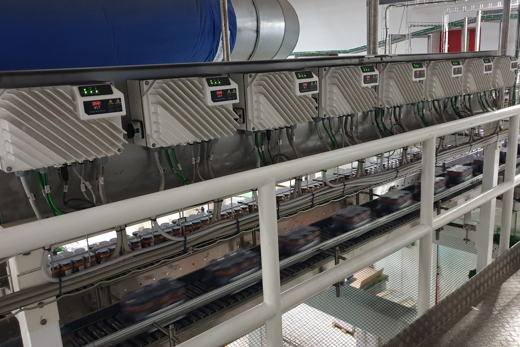
Todos los accionamientos descentralizados se han conectado en red e integrados en el PLC, que adquiere continuamente el estado operativo de las unidades en función del consumo energético. La conexión en red también permite reconfigurar los parámetros operativos de los variadores cuando sea necesario, detectar cualquier condición anormal o cambiar el diseño de la línea, todo en tiempo real.
La experiencia adquirida en dos años de funcionamiento de la planta ha confirmado el éxito de VLT® FlexConcept® en la reducción del número de variantes y, por tanto, de los costes operativos, el consumo de energía y las emisiones de CO2. La fábrica de Barilla se beneficia en términos de confiabilidad y economía general en el costo total de propiedad.
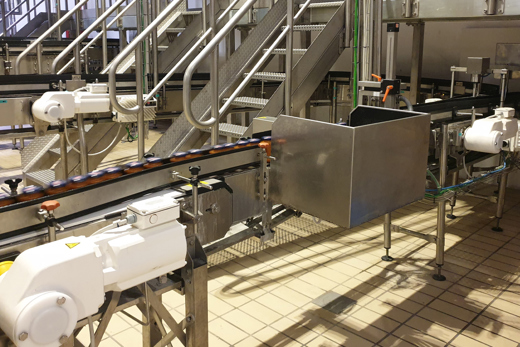
Mauro Ruozi da fe:
“El uso de 400 motorreductores y accionamientos descentralizados de alta eficiencia nos ha permitido reducir no solo el consumo de energía, sino también los costes indirectos, gracias al uso de menos espacio para los cuadros eléctricos y al menor mantenimiento. Dado que se puede utilizar un solo modelo de variador en todos los puntos de la planta con una rápida reconfiguración remota, hemos reducido los activos fijos en el almacén de repuestos y hemos acelerado las operaciones de mantenimiento. Además, gracias a su superficie perfectamente lisa y resistente a los agentes de limpieza y soluciones desinfectantes más agresivos, las soluciones VLT® FlexConcept® se adaptan perfectamente a este tipo de aplicación ".
El mismo tipo de variador Danfoss, pero instalado en paneles eléctricos, también se ha utilizado en la planta de Rubbiano para impulsar algunos VLT® OneGearDrive® en condiciones IP69 K en el área de la cocina, cumpliendo con todos los requisitos, reglas y pautas sobre lavabilidad. , diseño higiénico y resistencia a las soluciones detergentes y desinfectantes.
Ruozi concluye: "El uso de las soluciones de Danfoss nos ha ayudado a perseguir nuestros objetivos de sostenibilidad, y los resultados han confirmado completamente lo que se predijo en la evaluación comparativa en profundidad que impulsó esta elección".
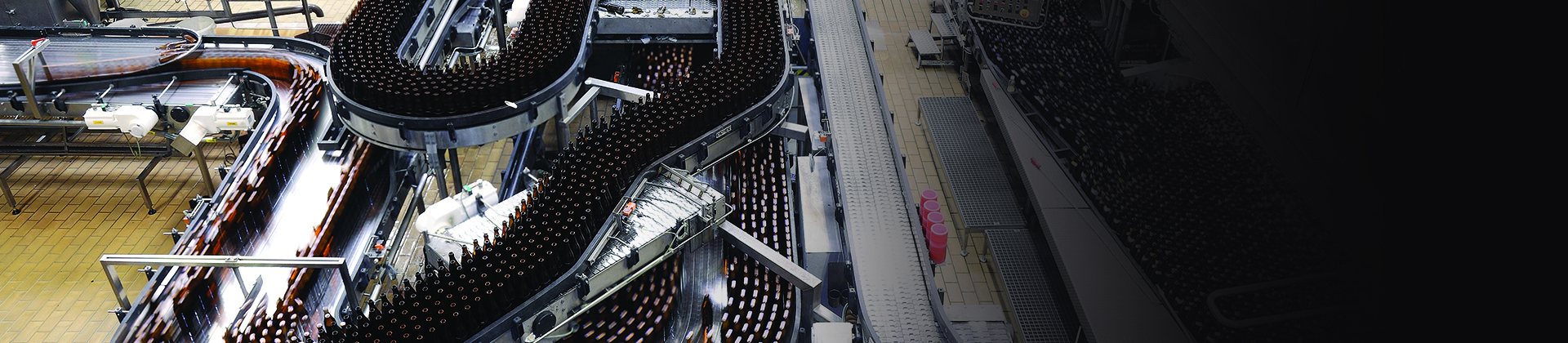
Descubra cómo maximizar el tiempo de actividad con el sistema VLT® FlexConcept®
VLT® FlexConcept® combina la tecnología de motores moderna con los convertidores de frecuencia más avanzados en un sistema de variador unificado flexible que ofrece alta eficiencia, confiabilidad robusta y reducción de variantes.