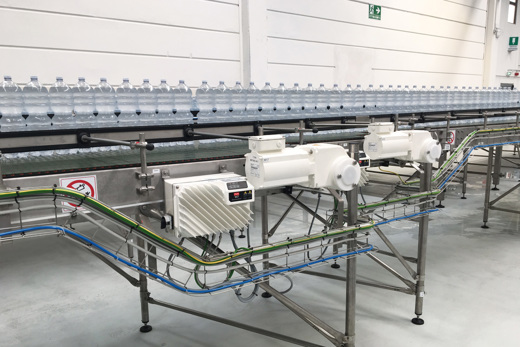
The VLT® FlexConcept® was chosen to help Nestlé Waters fulfill their goal to optimize environmental sustainability and minimize energy consumption.
The Sanpellegrino Group recently opened a mineral-water bottling plant for Nestlé Vera Naturae in Castrocielo, Italy. Heralded as a protocol for future bottling plants, it has a high focus on environmental sustainability and reducing energy consumption. And it is regarded as one of the most outstanding Nestlé Waters’ plants, due to its optimization of water consumption.
ACMI S.p.A., an Italian company that specializes in the production of high-technology bottling and packaging lines, and an important OEM customer of Danfoss Drives, has been working with Nestlé Waters for several years.
ACMI was commissioned to fulfill a new installation of AC drives and relevant gear motors in a new PET bottling line (with a capacity of 44,000 bottles per hour in a 2-liter format).
ACMI is well known for its research and technological innovation and strategic planning, and using all its resources to find the best possible solutions for its customers. The VLT® FlexConcept® conveyor solution was one of many strong arguments that helped ACMI choose Danfoss Drives to help them fulfill their commitment to Nestlé Waters.
Highly efficient conveyor drive system
Today’s bottling lines need higher efficiency, more flexibility and greater reliability to achieve real and ongoing cost reductions. Effective motor control of conveyors is crucial to improve process performance and reliability. The VLT® FlexConcept® conveyor drive solution combines integrated modern motor technology with the latest motor control components to create a coordinated, standardized system that optimizes energy consumption and minimizes maintenance costs.
The VLT® FlexConcept® consists of the VLT® OneGearDrive®, the VLT® DecentralDrive FCD 302 and/or the VLT® AutomationDrive FC 302.
The project for Nestlé Waters was a new decentralized installation consisting of 98 VLT® OneGearDrives® (three gear ratios) and 98 VLT® DecentralDrives FCD 302.
Increased hygiene levels
The VLT® OneGearDrive® offers high system efficiency – up to 40% power savings compared to conventional systems to ensure savings in both money and energy. Its completely smooth enclosure means there are no crevices or places for dirt to collect making it easy to clean and increasing the hygiene levels that are so important in bottle-filling lines. Fan-free operation ensures lower noise emission and that no airborne germs and dirt particles are drawn into the motor and then expelled back into the surrounding air – again important from a hygiene point of view.
Reduction in valuable commissioning time
By choosing decentralized drives, such as the VLT® DecentralDrive FCD 302, ACMI could deliver the whole conveying system ex-factory, pre-wired and pre-tested. This saved valuable commissioning time after installation and eliminated the need for expensive expert staff on-site to mount and test the drives. The only action required was to simply connect the power and fieldbus cables.
The decentralized drives also removed the need for switchgear rooms. By fitting neatly into the space next to the conveyor system, initial costs were significantly reduced. The loop in/out cable methodology in the VLT® Decentral Drive FCD 302 minimized cabling requirements and reduced costs. Maintenance is simplified as individual drives can be easily identified and repairs can be quickly performed by the fast module swap-over design.
The low total cost of ownership sealed the deal
With only 3 gearbox ratios in one common design, VLT® FlexConcept® allows plants such as Nestlé Waters to reduce and optimize their spare-part inventory by up to 70%, save on warehouse costs and have faster component availability. The unified user interface also reduces staff training costs. And, with fewer variants, the VLT® FlexConcept® simplifies project planning, installation, commissioning and maintenance, irrespective of whether a centralized or decentralized plant design is required. This results in significantly lower operating costs and substantial energy savings.
The Danfoss Drives service concept was the icing on the cake
As an OEM, it was important for ACMI to know what added value they could get from Danfoss. The Danfoss Drives service concept focuses on their specific needs. Drawing on extensive knowledge and experience in drive applications, the concept includes application advice, commissioning, service and repair and training.
Danfoss offers a broad range of user and service manuals in different languages and training sessions for design- and service-engineers that are tailored to the application at hand. And, to ensure optimal and trouble-free operation of the drives, a worldwide a team of specialists is on standby 24 hours a day.
“Before choosing the drives solution for the conveyors in our new bottling plant, we made, in close cooperation with our Product Technology Centre, a long investigation and an in-depth analysis of the best technologies currently available. Our final decision to go for the Danfoss VLT® FlexConcept® was based on the fact that it has proven to be the best in class not only in terms of both energy and water savings but more broadly also in terms of total cost of ownership. The solution perfectly matches our idea of combining environmental sustainability and economic growth,” stated Angelo Calderaro, Project Manager, and Nestlé Waters.