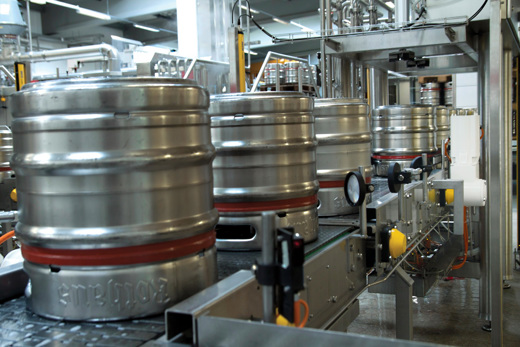
By installing a new KEG filling line using VLT® OneGearDrive® geared motors, frequency converters from the VLT® AutomationDrive series, and VLT® Decentral Drives, Rothaus AG has increased its filling capacity from 120 - 280 KEGs per hour with fewer drive types, and without increasing overall energy consumption.
Tannenzäpfle, Eiszäpfle and Weizenzäpfle, to mention just a few of the well-known beers produced by Badische Staatsbrauerei Rothaus AG, have an excellent reputation among beer connoisseurs. The brand image, along with the girl from the Black Forest and the Norway Spruce cones, are also well known beyond the boundaries of Baden-Württemberg. The brewery was founded in the inn “Zum Rothen Haus” in 1791 by Prince Abbot Martin Gerbert II of the Benedictine monastery of St. Blasien, and is currently one of the most modern breweries in Germany.
Superior product quality was the brewery’s highest priority even then, and this tradition has been upheld over the years. The firm therefore focuses on optimum hygiene and advanced production processes, which have required large investments in modern process technology over a number of years.
They include a new brew house, stainless steel fermentation and storage tanks, and extensive new piping. This allows the specialty beers from the Hochschwarzwald region to be produced using traditional methods such as cold fermentation and prolonged cold aging under optimal hygienic conditions.
Previous Experience with Danfoss Proved Savings Potential
Project manager Ralf Krieger and Filling Manager Roger Jäger, aided by their teams, selected Danfoss products for the drive systems of the new plant.
“We have used Danfoss frequency converters with success for several years and knew there was a potential to reduce the number of drive types in our production. The VLT® FlexConcept® also helps us to reduce our spare parts inventory,” explains Ralf Krieger, who also took the opportunity to start testing Danfoss VLT® OneGearDrive®.
The KEG filling system also serves as a test system for the hygienic version of the VLT® OneGearDrive®.
Although these permanent magnet (PM) motors are not necessarily required in the plant, we decided to fit 25 of them in the wet area to test their long-term behavior,” he continues. The VLT® OneGearDrives® Hygienic are controlled by 25 VLT® AutomationDrive FC 302 units, which are housed centrally in an electrical cabinet.
Fully Automated Filling from Cleaning to Palletizing
The new, fully automated KEG filling system was put into service in early 2011and replaced an outdated system. As a result of repeated investments and plant remodelling, the route travelled by the beer on its way to the filling stage had become longer and longer in the old plant. The new filling line was integrated seamlessly into the overall structure and reduces travel distances.
“The new filling line is fully automated; the only task that requires manual effort is supplying pallet stacks with 6 KEGs on each pallet to the infeed using a stacker. After this the stainless steel KEGs, which are fitted with RFID tags for quality control and tracking, pass through the entire system automatically. A robot turns the KEGs over with the valves facing downward and places them on a conveyor belt. The KEGs are cleaned on the outside and then automatically emptied and weighed,” explains Ralf Krieger.
Only completely empty KEGs are transferred to the three parallel machines, supplied by the plant engineering firm Albert Frey, that handle the tasks of thorough internal cleaning, rinsing and sterilization followed by filling with beer. The filled KEGs are turned over and fitted with plastic covers marked with all important data, such as the type, ingredients and expiry date, after which the finished KEGs are palletized by a robot. An automatic pallet truck then transports the freshly filled KEGs of Rothaus specialty beers on pallets to the Rothaus brewery finished goods stockroom.
System Architecture
“We decided to build a centralized system architecture in the wet area of the plant, with the VLT® Automation Drive FC 302 frequency converters housed in a central electrical cabinet. The modular units were mounted directly side by side for compact installation,” says Ralf Krieger.
The standard induction motors in the dry area of the palletizer are controlled by 40 VLT® Decentral Drive FCD 300 units.
The compact dimensions of the frequency converters facilitate their installation in the plant. They are fitted with covers to protect them against falling KEGs.
The decentral drives are powder-coated and are therefore easy to clean. Angled cooling fins and smooth surfaces ensure easy and reliable drainage of cleaning liquids. Five LEDs indicate the drive status at all times, and a connectable display enables easy diagnosis.
Integrated Components Ensure Efficiency
Another advantage of the Danfoss system is that the necessary EMC filter and mains chokes are factory fitted in all Danfoss VLT® frequency converters as integrated components. This saves even more space in the cabinet, which can be helpful in situations such as retrofitting existing plants, where space is usually limited.
As a result, the cabling effort is reduced while enabling the VLT® frequency converters comply with the applicable limits in the plant. The filters are also taken into account in the high efficiency figures, which are 98% or better. In practice, this translates into less heat dissipation and enables energy-efficient operation of the drives. The VLT® AutomationDrive FC 302 supports long motor cables as standard, which is extremely helpful in beverage plants with a centralized system structure. This eliminates the need for extra output filters as long as the cable length does not exceed 300 meters with unshielded cable or 150 meters with shielded cable, which reduces costs even further.
Energy Costs Unaffected by Production Boost
The new solution has enabled Rothaus boost filling capacities from 120-280 KEGs per hour with capacities of 10 to 50 liters. Impressively, the larger plant does not consume more energy than the previous plant.
“The components used in the VLT® FlexConcept® have proven their worth in the plant up to now. All motors and frequency converters operate reliably, and their designs offer a number of benefits compared to conventional drives. The equipment may optionally be operated in a centralized, decentralized or combined structure. All drives are designed for extremely high energy efficiency and provide good starting point for us to consider other projects with Danfoss products,” concludes Ralf Krieger.