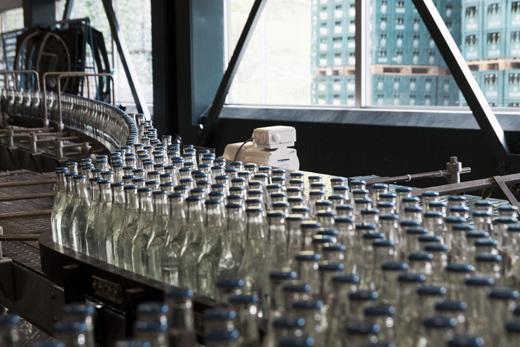
By using Danfoss VLT® OneGearDrives® to operate the conveyors in its filling line for mineral water, Valser Mineralquellen has replaced up to forty previous combinations of motors and gear units with just one motor size and three gear ratios. Subsequently the spares inventory has been significantly reduced and system output increased.
Reducing Complexity and Saving Energy
In the food and beverage industry demands for energy efficiency and flexibility are rising in line with increasing cost pressure. In the past, different drive concepts were required for different areas, such as production, filling and packaging. Previously, several hundred drives with a wide variety of sizes and power ratings were required to drive the large number of conveyors that connect the individual production machines. This resulted in large stocks of spare drives, corresponding maintenance effort and high energy costs.
Valser Mineralquellen recognized these considerations. Before modernisation with Danfoss VLT® OneGearDrives®, up to 40 different motor/gear variants with or without brakes were used, but now there is only one motor type in the modernized section of the plant. This not only reduces the cost of maintaining a full stock of spares but also saves a lot of maintenance effort. The time-consuming mechanical effort of swapping gear units on a spare motor to configure a suitable replacement for a defective drive has been entirely eliminated now that the OneGearDrive is used. Today Valser Mineralquellen keeps just three motors and one frequency converter in stock.
“This simplifies operations for us tremendously, particularly as the OneGearDrives are very energy efficient. Our direct electricity consumption has dropped by 10%”, said Roman Schmid, Maintenance Planner at Valser Mineralquellen.
“Furthermore, neutral-line currents are up to 50% lower, there are fewer harmonics, the phase balance is better, and there are fewer voltage and frequency deviations.”
“Together with the reduced spare parts inventory and easy installation, VLT® OneGearDrive® is a considerable improvement for our filling line. As part of our modernisation, we have also improved the operation of our conveyor systems. They run more smoothly now, and the belts don’t jerk at low speed,”according to Schmid.
VLT® OneGearDrive® – High Efficiency and Hygienic DesignVLT® OneGearDrive® is a highly efficient permanent magnet three-phase synchronous motor coupled to an optimized bevel gear box. The system can reach an efficiency level as high as 89%. With only one motor type and three gear ratios available, the motor concept covers all typical conveyor drives. Furthermore, the restricted range of physical configurations of the OneGearDrive simplifies spares holding and makes it more cost efficient, easing engineering and installation thanks to uniform mechanical dimensions.
The OneGearDrive is available in two versions: VLT® OneGearDrive® Standard for use in dry and wet production areas, and VLT® OneGearDrive® Hygienic for use in areas where hygiene is crucial and thorough cleaning is required, as well as in aseptic and clean room production areas.
Future-proof part of VLT® FlexConcept®
OneGearDrive is part of the VLT® FlexConcept®, Danfoss’ extremely flexible and efficient drive system concept that reduces the number of drive variants in typical food and beverage plants or material handing systems by up to 70%.
The VLT® FlexConcept® comprises the VLT® OneGearDrive®, combined with a VLT® Decentral Drive FCD 302 or VLT® AutomationDrive FC 302 frequency converter – perfectly matched components for energy-efficient drives in all system areas. This results in considerable savings in planning, commissioning, maintenance and inventory costs. Up to 50% cost savings compared to conventional systems can be achieved by using the OneGearDrive together with AutomationDrive FC 302 or Decentral Drive FCD 302.
The FlexConcept provides system manufacturers and operators with an solution which complies with applicable current and future standards relating to the new efficiency categories and guarantees a high degree of investment security. The products already fulfill the requirements of the Minimum Energy Performance Standard (MEPS) that will take force in 2017.
Valser Mineralbrunnen
Valser is Swiss mineral water from mineral springs in Vals, in the Canton of Graubünden. In 2002 the Hess Group sold Valser Mineralquellen AG to Coca-Cola HBC Schweiz, which produces and bottles products of the Coca Cola Company under licence.
The source water accumulates in the region of the Piz Aul massif in the form of rain, snow and ice. It seeps into the limestone marble, Bündner schist and dolomite and passes through cracks and fissures in these materials into the deeper parts of the mountain.
Inside the Piz Aul massif, the water is purified and highly mineralized by rock layers 220 million years old. After following a route at least 1000 meters deep over an average time of 25 years, the water eventually emerges from the Spring of St. Peter in Vals as a crystal-clear stream with a unique, balanced taste, enriched with many valuable minerals and trace elements.