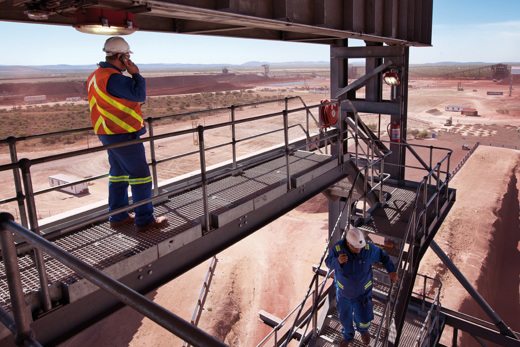
By employing VLT® drives with back channel cooling, the mine saves approximately 80 kW of electrical power. This benefit exceeds the power savings achieved by using high-efficiency motors instead of standard efficiency motors on the site.
Substation installation
At the Kolomela iron ore mine in South Africa, three 710 kW VLT® drives are installed on a mine dewatering system that distributes water to the plant operations as well as the local town water supply.
The traditional solution in the South African mining industry is to install drives in an enclosed MCC substation for protection from mining contaminants. Iron ore mines are known to be particularly dusty environments, with particles down to a few microns in size. This dust is not compatible with electronics, and so the closed, controlled air environment in the substation ensures the drives are kept cool and clean. However, to maintain the correct indoor temperature, the heat generated by the drives needs to be removed from the substation by an air conditioner.
Reduced air conditioning load
The load on the air conditioning system due to the heat loss from the drives and other equipment in the substation normally results in a relatively high power consumption of the air conditioning system. However in this case VLT® drives offer the ideal solution, with built-in back channel cooling, which significantly reduces the heat load in the substation from the drives. By employing VLT® drives, the power consumption in the substation was reduced by 80 kW,
- due to lower heat losses from the drives
- lower heat loads in the substation as a result of back channel cooling
- resultant lower power consumption of the air conditioning system in the substation.
The significantly smaller heat load enabled installation of a smaller, lower cost air conditioning system. This system has lower power consumption and operating costs.
Using the Danfoss back-channel cooling concept, air from outside the MCC substation is channeled through the floor of the substation, blown through the VLT® heatsink area, and then exhausted back out of the substation using simple ducting and without affecting the substation pressurization.
High-efficiency motors
During development of the mine, the focus was on optimizing energy efficiency by all possible means. High-efficiency motors were specified for the entire mine site, estimated to provide 65 kW power savings by comparison with standard efficiency motors. Nonetheless, the 80 kW power savings generated by the mine dewatering VLT® drives alone equate to even more than the total savings gained by selecting high-efficiency motors.
Payback
In a mine substation, use of VLT® drives with back channel cooling typically provides annual energy operating cost savings that are equivalent to approximately 8%-10% of the total purchase cost of all VLT® drives, compared to using alternative drives.
Taking advantage of back channel cooling requires installation of extra ducting (and sometimes filters), but this is achievable at a lower cost than not using back channel cooling. Without back channel cooling a significantly higher heat load from the drives accumulates in the substation, requiring purchase of a bigger, more expensive air conditioning system – and a larger power bill.
Therefore the payback for back channel cooling is instant. The mine achieves a net saving from day one of operations.
No-maintenance filter. Install and ignore it for ten years or more
Due to the harsh and dusty environment on the Kolomela iron ore mine site, an air filter is required to clean the air before it enters the heat sink channel of the VLT® drive.
What makes this air filter installation innovative is the use of a spin filter system. The spin filter used in the back channel cooling ductwork system for this substation uses a cyclone effect to provide a simple, maintenance free, clean air solution.
The alternative is a particulate air filter, which acts by blocking dust from passing through. Particulate air filters are however considered unsuitable for iron ore mine sites because they clog up due to the fine dust and therefore require a high level of maintenance.
Automatic Energy Optimization
The pumping system offers additional savings by utilizing the Automatic Energy Optimization (AEO) feature of the drive. Activating AEO ensures that motor magnetization is always at the optimum, real time requirement, and that no energy is expended unnecessarily.
Installed drives
In addition to the 710 kW dewatering pump drives at this mine site, there are many other VLT drives rated from 11 kW to 800 kW, reliably controlling equipment including
- Feed conveyors
- Buffer stockpile conveyor
- Train load out station conveyor
- Slew and long travel drive motors on the
- bucket wheel reclaimer
- fine ore stacker and
- lumpy ore stacker
Kumba Iron Ore’s Kolomela Mine comprises three open-cut pits and is a full dry-crush and screen operation, situated near the town of Postmasburg in the Northern Cape province of South Africa. The processing plant where the VLT® drives are installed was commissioned in 2011. During 2013 Kolomela mine produced 10.8 Mt iron ore, almost 2 Mt above the original target of 9Mt. The name “Kolomela” means “to dig deeper or further, to persevere”. Kumba Iron Ore, a member of the Anglo American plc group, is a leading value-adding supplier of high-quality iron ore to the global steel industry.