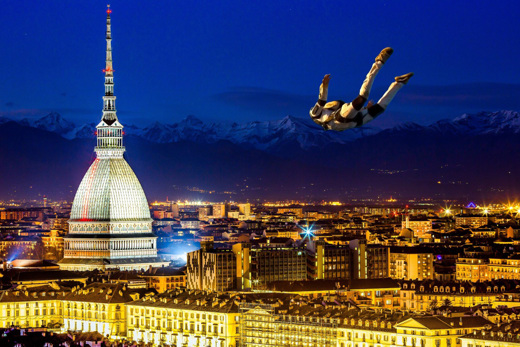
Mankind’s desire to fly has always been a dream since ancient times, so far a dream that only the skydivers in freefall have truly fulfilled.
Now a new attraction came to Turin: Fly Experience, the first vertical wind tunnel ever built in Italy that allows everyone to experience the real thrill of flight; namely the same feelings and the same perception sensed by a skydiver in freefall.
An innovative project
The flight chamber features a clear glass cylinder with a diameter of 4.30 meters and 11 meters tall where a powerful vertical airflow allows one or more persons to lift into the air and to perceive the great sensation of floating in the void, all in full safety thanks to the most advanced technologies.
The vertical air column is generated by 4 motors 500 kW each, driven by 4 Danfoss VLT® HVAC Drive FC 102 which ensure a precise speed control of the thrust axial fans. The air speed is controlled in a wide range from 180 km/h to lift a person in a horizontal position, up to a maximum speed of 300 km/h for upside down flight and for aerobatics, accomplishing the needs for both novices and professionals alike.
A skydiver who jumps from a plane has less than a minute in free fall to perform aerobatics, at the Fly Experience one can practice for several consecutive minutes in full safety. No intervals needed between multiple launches and no dependency on weather conditions.
Low harmonics and premium efficiency
The plant is adjacent to a very popular shopping mall, which is why one of the basic technical requirements was to minimize as much as possible the harmonic distortion generated by the drives, but while ensuring the best energy efficiency. This has been achieved by Danfoss through the installation of 4 standard 500 kW VLT® HVAC Drive FC 102 which guarantee a remarkable efficiency of 98%, and two Danfoss VLT® Advanced Active Filter AAF 006 400 A upstream of the two transformers (one for each pair of drives) to mitigate the distorted loads.
This solution has proved satisfactory not only from the point of view of the THvD value achieved at the secondary side of the transformers, but also much more efficient when compared to the alternative originally evaluated by the customer which involved the use of four Low Harmonic Drives based on Active Front End (AFE) technology.
Indeed, that solution would have led to the use of four units having a dissipation at full load of 22 kW each for a total amount of 88 kW, that means 25,352 W more than the current solution.
Safety first
One of the challenge that have been addressed, was to ensure the safety of people in case of mains failure.
In fact, coasting of the fans would result in a sudden loss of the air column and in some cases this could not match the strict safety expectations.
To get rid of this possibility, all drives have been enabled with the “Kinetic Backup” function that in case of mains failure uses the kinetic energy due to the moment of inertia of the fans to keep the units “alive” in order to perform a controlled ramp down.
Therefore, in case of mains loss, the drives continue to be fully operational ensuring a gradual and smooth reduction of the air flow to protect people from possible injuries.
This feature also guarantees longer uptime because effectively compensates for any temporary voltage dips preventing the drives from locking up.
Annual saving with Danfoss solution: > 10,000 EUR
Assuming an average usage of 4000 hours per year at a cost of energy equal to EUR 0.106 per kWh, this translates to the end user in an annual savings of around EUR 10,000 and about 41500 kg of CO2 not released into the atmosphere.