
Proekologiczne obiekty przemysłowe bazują na zaawansowanych rozwiązaniach, zapewniających maksymalną efektywność energetyczną oraz skuteczne gospodarowanie zasobami. Istotną częścią nowoczesnej infrastruktury są narzędzia umożliwiające zdalne monitorowanie poszczególnych elementów instalacji oraz całych układów. Ich znaczenie widać doskonale na przykładzie zielonej fabryki Danfoss w Grodzisku Mazowieckim.
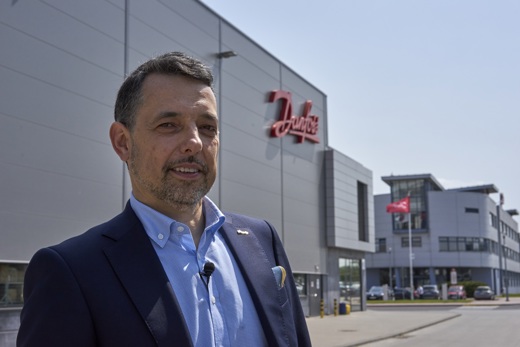
Dane w centrum zrównoważonego rozwoju przemysłu
Zrównoważony rozwój sektora przemysłowego jest ściśle związany z nowymi technologiami. Wprowadzanie rozwiązań wykorzystujących chmurę obliczeniową czy sztuczną inteligencję pozwala organizacjom na proekologiczne oraz zgodne ze strategią zrównoważonego rozwoju zmiany. Otwiera przy tym nowe pola do unowocześniania obiektów i usprawniania wewnętrznych procesów.
Istotną rolę w modernizowaniu firm w duchu zielonego przemysłu odgrywają narzędzia do
predykcyjnego monitoringu stanu silników. Jednym z nich jest Condition-Based Monitoring, dzięki któremu przedsiębiorstwa mogą w czasie rzeczywistym monitorować stan silników i układów napędowych i wykrywać problemy w prawidłowym funkcjonowaniu instalacji.
– Współcześnie znaczenie analityki jest nie do przecenienia. Wykorzystując dane, firmy mogą nie tylko efektywniej dbać o park maszynowy i całą infrastrukturę, ale też, jak w przypadku naszego zakładu w Grodzisku Mazowieckim, liczyć oszczędności wynikające z zainstalowania przetwornic lub optymalizacji pracy central wentylacyjnych. Potencjał rozwiązań monitorujących pracę urządzeń wyraźnie widać na przykładzie zeroemisyjnej fabryki Danfoss, która jest pilotażowym projektem tego typu w Polsce. Wszystkie instalacje techniczne zakładu są na bieżąco kontrolowane, co pozwala prowadzić optymalizację ich pracy dla uzyskania lepszej efektywności energetycznej i zapewnia bezawaryjną eksploatację – wyjaśnia Jakub Czapliński, dyrektor sprzedaży w Danfoss Drives.
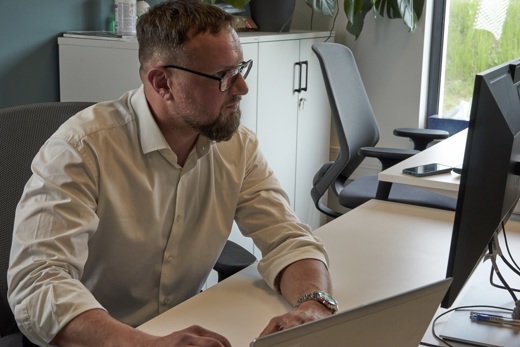
Zdalny monitoring fabryki w Grodzisku Mazowieckim
Danfoss w Grodzisku Mazowieckim produkuje między innymi zawory elektromagnetyczne oraz zawory do systemów chłodniczych. Działający na miejscu system wentylacji i klimatyzacji, oparty na przetwornicach częstotliwości Danfoss, zapewnia odpowiedni przepływ powietrza w obiekcie, a tym samym pozwala mu działać zgodnie z wyznaczonymi normami oraz zapewniać zatrudnionym pracownikom wysoki standard pracy.
Monitoring obejmuje dziesięć przetwornic częstotliwości, umieszczonych na dachu, o mocy do 18,5 kilowatów. Urządzenia komunikują się z chmurą obliczeniową poprzez Gateway za pomocą sieci komunikacyjnej bazującej na standardzie przemysłowego Ethernetu – Profinet.
Algorytmy CBM służące do predykcyjnego monitorowania stanu silnika monitorują w czasie rzeczywistym dwa parametry: stan izolacji silnika i profil obciążenia. Następnie dane z przetwornic, przez Gateway przekazywane są do chmury Azure. Dzięki temu uprawnieniu pracownicy służby utrzymania ruchu, wykorzystując przeglądarkę internetową, mają dostęp do kompleksowej informacji dotyczącej instalacji. Mogą z wyprzedzeniem reagować na szereg sygnałów, na przykład wskazujących na zwiększone przeciążenie, czy możliwe zabrudzenie filtrów w centralach wentylacyjnych. Całość bazuje na pomiarze wartości chwilowych prądu w funkcji prędkości i porównaniu ich z prawidłową charakterystyką, ostrzegając i alarmując służby utrzymania ruchu o wszelkich odstępstwach od wartości bazowych.
– Opomiarowanie w naszej fabryce analizuje nie tylko pracę przetwornic częstotliwości, które są źródłem sterowania dla silnika elektrycznego lub centrali wentylacyjnej, ale całego systemu HVAC. Szczegółowa obserwacja jest możliwa dzięki zastosowaniu algorytmów matematycznych, które wyznaczają trendy na podstawie pomiarów bazowych. Każde wyjście poza ramy przekłada się na informację, którą należy traktować jako sygnał o usterce lub nadchodzącej awarii. To z kolei pozwala reagować z wyprzedzeniem i zaplanować prace serwisowe, by zminimalizować ich wpływ na działalność fabryki – tłumaczy Krzysztof Kubicki, koordynator ds. sprzedaży w Danfoss Drives.
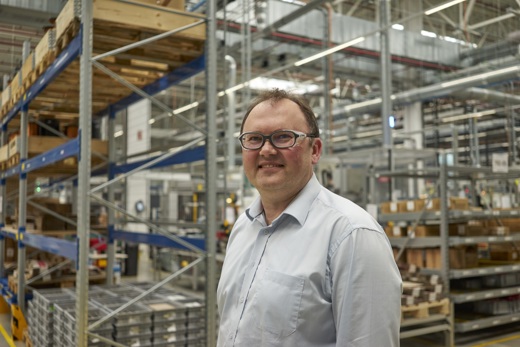
Optymalizacja wewnętrznych procesów
Zdalny monitoring stanowi dodatkowe narzędzie dla personelu utrzymania ruchu, który może działać skuteczniej, a jednocześnie zmniejszyć koszty związane z naprawami i magazynowaniem części zapasowych. Przewidywanie awarii wpływa na lepsze planowanie prac serwisowych i przekłada się na optymalizację działań w tym zakresie. Wykonywane przez inżynierów ruchu ręczne monitorowanie wiąże się z konkretnymi nakładami czasu, które mogą zostać zmniejszone, dzięki automatyzacji
i danym wskazującym, na przykład, na konieczność wymiany filtrów.
Condition-Based Monitoring wspiera specjalistów w takim planowaniu przestojów na akcje serwisowe, by w jak najmniejszym stopniu generowały straty w procesie produkcyjnym. Zazwyczaj nie wymaga to instalacji dodatkowych czujników. Łatwość wdrożenia otwiera drogę do monitorowania, na przykład, stanu uzwojenia stojana silnika. Analiza charakterystyki prądowej
i napięciowej umożliwia w takim przypadku wykrywanie uszkodzeń już na wczesnym etapie, a tym samym minimalizowanie kosztownych awarii.
Condition-Based Monitoring i Remote Monitoring to dzisiaj również istotny element strategii polityki zrównoważonego rozwoju realizowanej przez sektor przemysłowy. Rozszerzona analityka wpisuje się w potrzeby zakładów w dobie hybrydyzacji, umożliwiając takie planowanie prac, by poszczególne maszyny nie wchodziły w tym samym momencie w pełne obciążenie i nie generowały wartości szczytowych. Jednocześnie system zapewnia większe możliwości dostosowywania charakteru pracy urządzeń do oczekiwań i warunków, by zmniejszać zużycie energii elektrycznej. Ma to zastosowanie w przypadku centrali klimatyzacyjnych, których funkcjonowanie może być modyfikowane w reakcji na zmienne warunki atmosferyczne.
– Condition-Based Monitoring i Remote Monitoring, zaimplementowane w naszej fabryce, łączą wygodę dostępu do danych, których sposób prezentacji możemy swobodnie personalizować w dashboardzie, z szerokim zakresem funkcjonalności. Wpływają one na bezpieczeństwo produkcji, ochronę zdrowia pracowników i ich komfort pracy. Dostęp z poziomu przeglądarki internetowej do gromadzonych informacji, które są bezpiecznie przechowywane w chmurze i sprawnie przekazywane do specjalistów w formie alertów SMS czy mailowych, ułatwia wyciąganie trafnych wniosków oraz minimalizuje liczbę przestojów – Krzysztof Kubicki, koordynator ds. sprzedaży w Danfoss Drives.
– Specyfika naszej produkcji zakłada utrzymywanie magazynu wyprodukowanych urządzeń, tak zwanego buforu bezpieczeństwa. Jest to związane z efektywnością energetyczną fabryki i wiarygodnością biznesową dla naszych partnerów i klientów. Natomiast, jeśli mielibyśmy hipotetycznie oszacować straty przerwy w produkcji, a także straty związane z odejściem obsługi od stanowisk i cenę serwisu, to koszt jednorazowego przestoju oraz napraw uszkodzonych urządzeń wyniósłby nawet ponad 100 tysięcy złotych. Unikanie niespodziewanych przestojów ma więc konkretne przełożenie na oszczędności odczuwane w przemyśle – tłumaczy Jarosław Strzelczyk, starszy dyrektor operacyjny w Danfoss Poland.
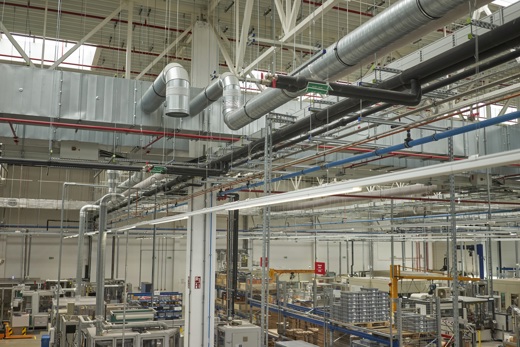
Zielona fabryka pracująca w oparciu o dane
Funkcjonujący w Grodzisku Mazowieckim zakład może pochwalić się wysoką efektywnością energetyczną. Jest to pierwszy tego rodzaju obiekt Danfoss na świecie zasilany w pełni
z odnawialnych źródeł energii, w którym wszystkie systemy techniczne są zautomatyzowane. Prawidłowe funkcjonowanie, zgodne z założeniami ESG organizacji, jest możliwe również dzięki dostępowi do danych, które są zbierane, przetwarzane i przechowywane przy wykorzystaniu systemów Condition-Based Monitoring i Remote Monitoring. Szereg dostępnych funkcjonalności zapewnia odpowiedzialnym za infrastrukturę specjalistom dostęp do wiedzy, którą mogą nieustannie wykorzystywać do optymalizacji procesów i lepszego zarządzania urządzeniami. W ten sposób rozwiązanie wpisuje się w aktualne potrzeby przemysłu 4.0 w Polsce i na całym świecie.
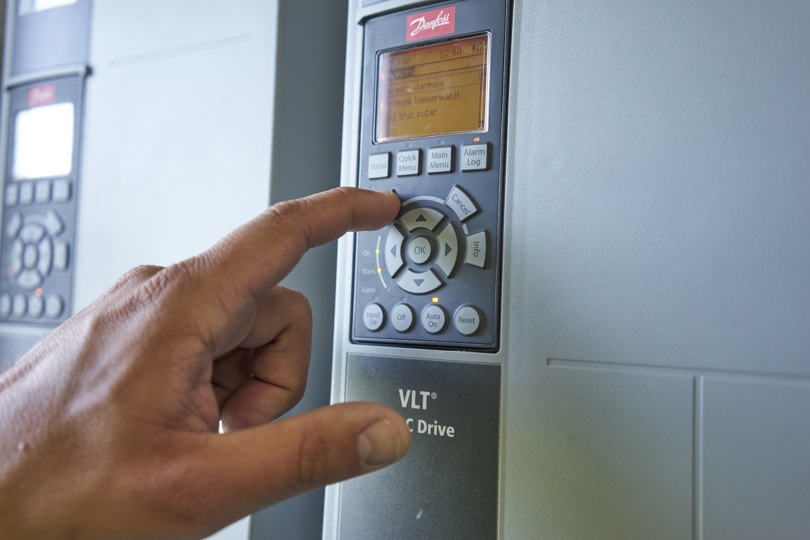
Brak przestojów dzięki inteligentnym przetwornicom częstotliwości Danfoss Drives z funkcją Condition-Based Monitoring
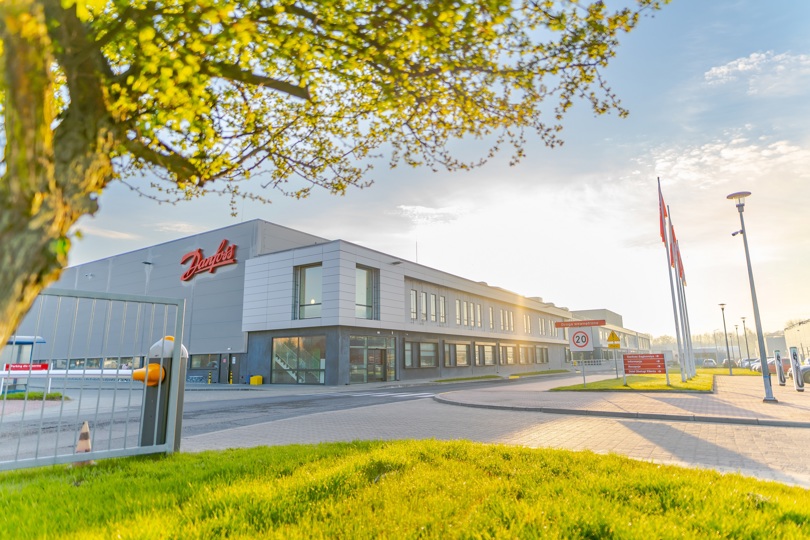
Odwiedź neutralną emisyjnie fabrykę Danfoss
Zapisz się na Decarbonization Path i poznaj trzy kluczowe kroki do osiągnięcia neutralności klimatycznej.