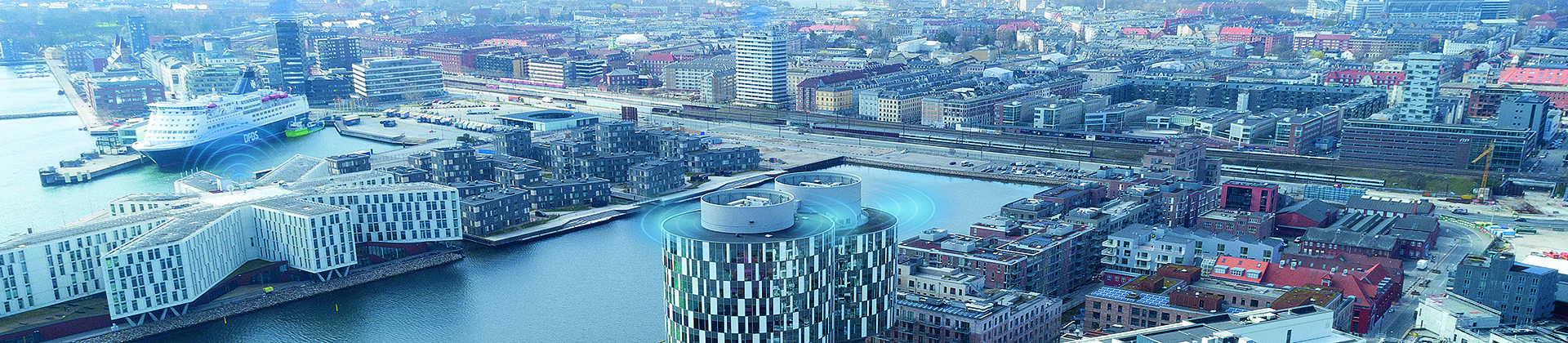
I drives sono più che semplici dispositivi di potenza
Grazie alla capacità di agire come sensori e hub di sensori, di elaborare, memorizzare e analizzare i dati e alle capacità di connettività, i drives sono elementi essenziali nei moderni impianti di automazione e nei sistemi di gestione di edifici (BMS). La funzionalità integrata di monitoraggio predittivo consente nuove modalità di esecuzione della manutenzione, come la manutenzione predittiva.
Evoluzione dei sistemi di automazione industriale
Nel passaggio all'attuale millennio, abbiamo assistito a un profondo cambiamento nella tecnologia, che ha portato a un modo completamente nuovo di lavorare, in modo digitale. Questa è la quarta rivoluzione industriale.
La prima rivoluzione industriale, avvenuta nel corso del XVIII e XIX secolo, è stata una rivoluzione meccanica, innescata dall'invenzione della macchina a vapore.
Alla fine del XIX e all'inizio del XX secolo, la seconda rivoluzione industriale si è sviluppata con l'adozione della produzione di massa, dell'elettrificazione e dei cambiamenti nelle comunicazioni. È stata l'era della rivoluzione elettrica. Più tardi, nel XX secolo, la terza rivoluzione industriale ha portato progressi nei semiconduttori, nell'informatica, nell'automazione e in Internet. Questa fase è nota anche come Rivoluzione Digitale.
La quarta rivoluzione industriale è nata dalla connessione in rete di computer, persone e dispositivi alimentati da dati e machine learning.
Sebbene il termine "Industria 4.0" sia abbastanza vago, una possibile definizione descrive il collegamento in rete intelligente di persone, dispositivi e sistemi sfruttando tutte le possibilità della digitalizzazione lungo l'intera catena del valore.
Tendenze dell'Industria 4.0 nei sistemi di automazione
L'impatto dell'Industria 4.0 sui sistemi motore e sui sistemi di gestione di edifici è una migrazione dalla "piramide dell'automazione" ai "sistemi in rete". Ciò significa che i vari elementi del sistema, come motori, azionamenti, sensori e controlli, sono interconnessi e collegati a un cloud - dove i dati vengono archiviati, elaborati, analizzati e dove vengono prese le decisioni.
In una rete di automazione, la quantità di dati è importante. Poiché i dati sono prodotti principalmente da sensori, il loro numero nei moderni sistemi di automazione è in aumento. Motori e macchine – come ventilatori, pompe e trasportatori – non sono i partecipanti più ovvi in una rete di dati. I sensori sono quindi necessari per raccogliere dati da queste macchine. I sensori sono connessi alla rete di dati utilizzando vari sistemi. Durante l'introduzione di un sistema avanzato di monitoraggio delle condizioni, il costo aggiuntivo dei sensori e della connettività è spesso considerato un ostacolo.
I moderni inverter a velocità variabile aprono nuove opportunità nella rete di automazione Industria 4.0 e nei sistemi di gestione di edifici. Tradizionalmente, i drives venivano considerati processori di potenza per il controllo della velocità del motore, del ventilatore, del trasportatore e/o della pompa. Oggi, anche gli inverter fanno parte della catena dell'informazionesfruttando il vantaggio della potenza di elaborazione, della capacità di memorizzazione e dell'interfaccia di comunicazione integrate nel convertitore di frequenza.
Per saperne di più, consulta il white paper e il video CBM
Oggi i drives sono molto più che semplici processori di potenza. Grazie alla capacità di agire come sensori e hub di sensori, elaborare, memorizzare e analizzare i dati, insieme alle capacità di connettività, sono diventati elementi vitali nei moderni sistemi di automazione .
I convertitori di frequenza sono spesso già presenti nelle installazioni automatizzate e rappresentano quindi un'ottima occasione per passare all'Industria 4.0.
Questo consente nuovi modi di eseguire la manutenzione, come la manutenzione predittiva. La funzionalità è
Esplora tutte le opportunità sulla manutenzione predittiva
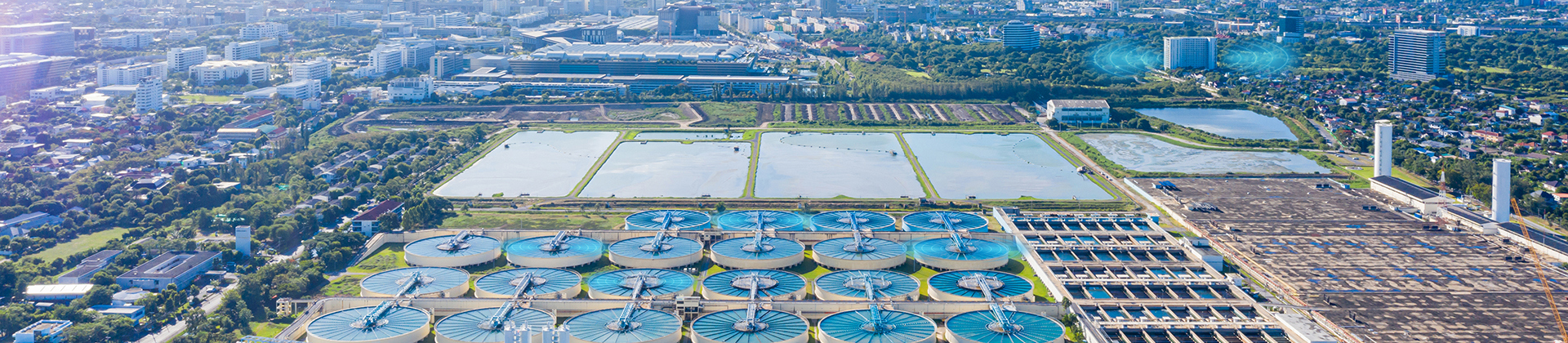
Monitoraggio dell'acqua e delle acque reflue
Nelle applicazioni idriche e di trattamento delle acque reflue, l'implementazione di un sistema di monitoraggio delle condizioni, integrato nei drives, ottimizza le prestazioni complessive.
E con l'edge computing, non è necessario connettersi al cloud.
Intelligenza integrata
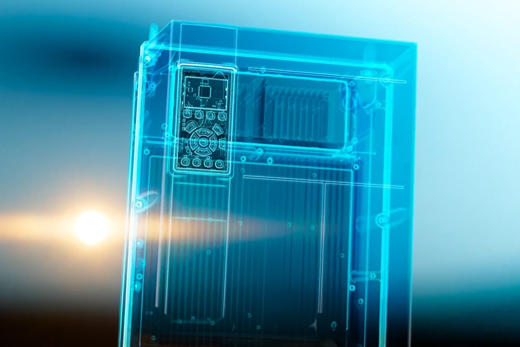
Cos'è un inverter intelligente?
Nella rete dell'Industria 4.0, l'inverter svolge un ruolo importante ed è caratterizzato da alcune funzioni caratteristiche:
- Connettività sicura: il convertitore di frequenza può essere collegato ad altri elementi in modo sicuro. Altri elementi della rete possono includere inverter, PLC, sensori e un cloud.
- Il convertitore di frequenza agisce da sensore: i drives utilizzano l'analisi della corrente motore e della tensione motore per rilevare le prestazioni del motore e dell'applicazione.
- Il convertitore di frequenza agisce da hub per i sensori: il convertitore di frequenza acquisisce dati da sensori esterni relativi al processo controllato dal convertitore stesso.
- Il convertitore di frequenza agisce da controllore: il drive può sostituire il PLC quando le limitazioni dell'applicazione lo consentono.
- Porta il concept del tuo dispositivo: connettività wireless con dispositivi intelligenti (smartphone, tablet).
Le informazioni provenienti dall'inverter possono essere identificate come segue:
- Segnali istantanei: segnali misurati direttamente dal drive utilizzando sensori integrati. Dati come la corrente motore, la tensione, la temperatura del drive e le loro derivate, ovvero la potenza come moltiplicazione della corrente e della tensione, o la coppia motore. Inoltre, il drive può essere utilizzato come hub per collegare sensori esterni che forniscono segnali istantanei.
- Segnali elaborati: segnali derivati dai segnali istantanei. Ad esempio, la distribuzione statistica (valori massimi, minimi, media e deviazione standard), l'analisi del dominio di frequenza o gli indicatori del profilo di missione.
- Segnali analitici: segnali che forniscono indicazioni sulle condizioni del drive, del motore e dell'applicazione. I segnali vengono utilizzati per attivare la manutenzione o per migliorare la progettazione del sistema.
Le tecniche di analisi della corrente motore permettono al drive di monitorare le condizioni del motore e dell'applicazione. La tecnica consente potenzialmente di eliminare i sensori fisici o di estrarre le prime segnalazioni di guasto che non sarebbe stato possibile rilevare. Ad esempio, l'utilizzo di questa tecnica consente di rilevare in anticipo i guasti di cavitazione e di avvolgimento o l'eccentricità del carico meccanico.
Il concetto del drive come hub per i sensori prevede il collegamento di sensori esterni al convertitore, evitando così la necessità di un gateway per collegare il sensore fisico alla rete di dati.
I sensori di vibrazione, di pressione e di temperatura sono esempi di sensori che possono essere collegati al convertitore di frequenza.
Il vantaggio di questo concetto non è solo legato al costo, ma anche alla possibilità di correlare i dati del sensore con diversi tipi di dati presenti nel convertitore di frequenza. Un esempio ovvio è la correlazione tra il livello di vibrazione di un sensore esterno e la velocità del motore, poiché la vibrazione dipende dalla velocità.
Manutenzione predittiva e altre strategie di manutenzione
Di seguito sono elencati diversi tipi di strategie di manutenzione:
- Manutenzione correttiva: dopo un guasto, il prodotto viene sostituito.
- Manutenzione preventiva: il prodotto viene sostituito prima che si verifichi un guasto, anche se il prodotto non riceve alcuna comunicazione.
- Manutenzione predittiva: il prodotto emette un avviso quando la sua durata effettiva varia rispetto alla durata prevista e vengono indicate le possibili cause principali.
- Manutenzione predittiva: il prodotto fornisce un avviso prima che raggiunga le ore di funzionamento previste per avviare l'intervento di manutenzione.
Perché è necessaria la manutenzione predittiva?
La manutenzione correttiva e quella preventiva sono basate sui guasti (eventi) o sul tempo. Pertanto, la manutenzione viene effettuata in caso di guasti (correttiva) o dopo ore di funzionamento prestabilite (preventiva). Questi tipi di manutenzione non utilizzano feedback provenienti dall'applicazione corrente.
Con l'introduzione dell'Industria 4.0 e la disponibilità dei dati dei sensori, oggi sono possibili tecniche di manutenzione predittiva. Tali strategie di manutenzione utilizzano i dati reali dei sensori per determinare le condizioni delle macchine in servizio (manutenzione predittiva) o per prevedere i guasti futuri (manutenzione preventiva).
Panoramica e vantaggi della manutenzione predittiva
La manutenzione predittiva è la tecnica di manutenzione più semplice e intuitiva basata sui dati dell'applicazione reale. I dati acquisiti vengono utilizzati per monitorare lo stato dell'attrezzatura in servizio. A tale scopo, i parametri chiave vengono selezionati come indicatori per identificare i guasti in fase di sviluppo. Le condizioni di una macchina generalmente si deteriorano nel tempo. Ciò è illustrato dalla curva P-f che mostra un tipico modello di guasto. Un guasto funzionale si verifica quando l'apparecchiatura non esegue la funzione prevista. La manutenzione predittiva ha lo scopo di individuare i potenziali guasti prima che si verifichino.
Vantaggi della pianficiazione degli interventi di manutenzione
- Riduzione dei tempi di fermo
- Eliminazione di interruzioni impreviste della produzione
- Ottimizzazione della manutenzione
- Riduzione delle scorte di ricambi
Il CBM in 3 step
Condition-based monitoring per convertitori di frequenza a velocità variabile
Una parte integrante della manutenzione predittiva prevede il monitoraggio delle condizioni di macchine e impianti.
Nelle applicazioni a velocità variabile, le condizioni dell'applicazione spesso dipendono dalla velocità. Ad esempio, i livelli di vibrazione tendono ad aumentare a velocità più elevate, sebbene questa relazione non sia lineare. Infatti, a determinate velocità possono verificarsi risonanze che scompaiono quando la velocità viene aumentata.
L'utilizzo di un sistema autonomo per monitorare le condizioni di un'applicazione a velocità variabile è complicato dalla necessità di conoscere la velocità e la correlazione tra il valore monitorato e la velocità.
L'utilizzo di inverter per il monitoraggio predittivo ("inverter come sensore" o inverter come hub per i sensori") è una soluzione vantaggiosa, in quanto le informazioni sulla velocità dell'applicazione sono già presenti nel drive.
Inoltre, le informazioni sulla coppia e sull'accelerazione del carico/motore sono prontamente disponibili nel convertitore di frequenza.
Il Condition-based Monitoring in tre step:
Prodotti in evidenza
Prodotti Danfoss che utilizzano il monitoraggio predittivo
-
if (isSmallPicture) {
; } else if (isBigColumns) { } else { }VLT® HVAC Drive FC 102Il VLT® HVAC Drive FC102 è l'inverter resistente e intelligente che migliora le applicazioni su pompe e ventilatori nei sistemi di gestione di edifici, e funziona outdoor in quasi tutte le condizioni climatiche.
-
if (isSmallPicture) {
; } else if (isBigColumns) { } else { }VLT® Refrigeration Drive FC 103VLT® Refrigeration Drive FC 103 è l'inverter dedicato al controllo di compressori, pompe e ventilatori. Assicura notevoli risparmi energetici negli impianti di refrigerazione.
-
if (isSmallPicture) {
; } else if (isBigColumns) { } else { }Inverter VLT® AQUA Drive FC 202Il VLT® AQUA Drive FC 202 controlla tutti i tipi di pompe ed è dotato di un controllore in cascata.
-
if (isSmallPicture) {
; } else if (isBigColumns) { } else { }VLT® AutomationDrive FC 301/FC 302Il VLT® AutomationDrive FC 301/FC 302 è progettato per il controllo a velocità variabile di tutti i motori asincroni e motori a magneti permanenti. È disponibile in una versione standard (FC 301) e in una versione avanzata altamente dinamica (FC 302) con funzionalità supplementari.
-
if (isSmallPicture) {
; } else if (isBigColumns) { } else { }VACON® NXP DC/DC Converter - Supporto energetico vicino al consumoMassimizza la produzione di energia nelle soluzioni ibride e contribuisce a migliorare le prestazioni avvicinando il supporto di energia al consumo.
-
if (isSmallPicture) {
; } else if (isBigColumns) { } else { }VACON® NXP DCGuard - Protezione e stabilità della rete DCVACON® NXP DCGuard™ fornisce una protezione da cortocircuito affidabile dei sistemi di distribuzione DC per una selettività completa tra i sistemi di distribuzione; inoltre garantisce una rapida disconnessione in caso di guasto.
-
if (isSmallPicture) {
; } else if (isBigColumns) { } else { }VACON® NXP Common DC Bus - Utilizza e redistribuisci l'energia in modo efficienteInverter che consente a integratori di sistema, costruttori di macchine e OEM di progettare e costruire sistemi industriali efficienti. Disponibile nelle configurazioni Active Front End (NXA), Front End non rigenerativo (NXN), chopper di frenatura (NXB) e Inverter (NXI).
-
if (isSmallPicture) {
; } else if (isBigColumns) { } else { }VACON® NXP Liquid Cooled Common DC Bus - Inverter di facile integrazione e massima affidabilitàIntegra i vantaggi del raffreddamento a liquido nei sistemi common DC bus in situazioni gravose. Sono disponibili le configurazioni Active Front End (NXA), Front End non rigenerativo (NXN), chopper di frenatura (NXB) e Inverter (NXI).
-
if (isSmallPicture) {
; } else if (isBigColumns) { } else { }VACON® NXP Grid Converter - Inverter per una migliore stabilità della reteConvertitori di frequenza raffreddati a liquido progettati specificamente per essere applicati nei sistemi di distribuzione intelligenti, nei sistemi di stoccaggio dell'energia e di gestione dell'energia nel settore navale.
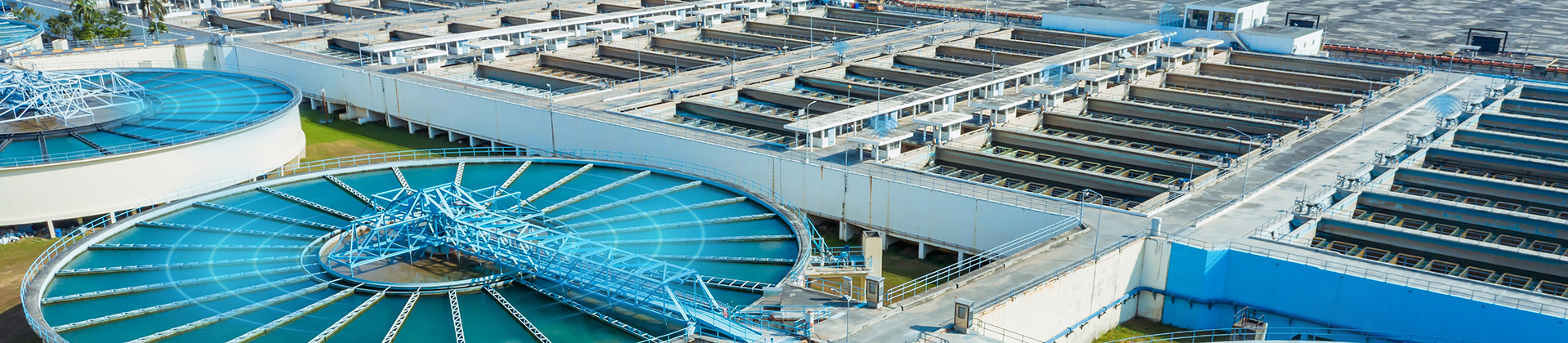
Le prime innovazioni di Danfoss
Il CBM nasce da una lunga storia di innovazioni Danfoss. I drives Danfoss si distinguono dagli altri presenti sul mercato per le funzioni intelligenti integrate, che riducono la necessità di componenti esterni necessari.