In generale, quando si tratta di refrigeranti, i chiller si dividono in due categorie: a pressione bassa/media (L/M) e a pressione media/alta (M/H). I chiller a pressione L/M possono trarre vantaggio dall'utilizzo di HFO puri (R1233zd e R1234ze), con un GWP molto vicino allo zero. L'infiammabilità è ridotta e gestibile, soprattutto per i sistemi installati all'aperto o in una sala macchine. Prevediamo che, nel breve-medio termine, questi tipi di sistemi utilizzeranno refrigeranti a bassissimo GWP. Il limite superiore di GWP, per i chiller a pressione L/M di grandi dimensioni, potrebbe essere pari a 630, valore che corrisponde al GWP della miscela HFO R513A, inclusa nel regolamento EPA-SNAP del luglio 2015, mentre la R134a sarà dequalificata a partire dal 2024.
Per i chiller a pressione M/H, le alternative con GWP medio sono nel range di 125-750 GWP, ma gli utenti devono essere disposti ad accettare una classificazione di infiammabilità A2L. Questo, ancora una volta, potrebbe essere accettabile per i sistemi installati all'aperto o in una sala macchine. In termini di GWP, il mercato probabilmente adotterà le alternative che offrono il miglior compromesso tra costi e prestazioni del sistema. Prevediamo che la scelta cadrà sui refrigeranti ad alta densità/alta pressione con un GWP intorno a 500-750.
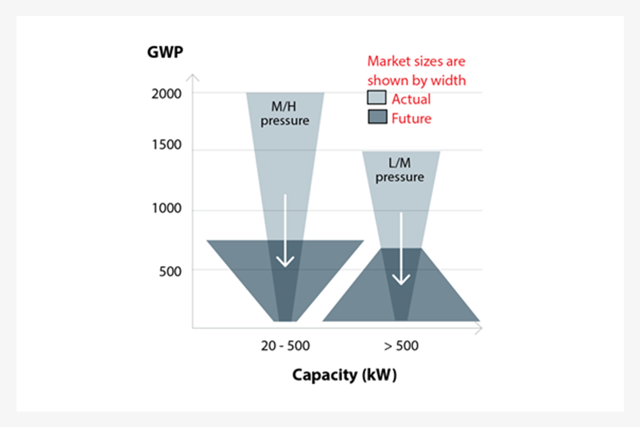
I sistemi VRF utilizzano quantità relativamente elevate di refrigerante per unità rispetto ai sistemi canalizzati, a causa dei loro evaporatori decentrati e delle conseguenti tubazioni. Per minimizzare le dimensioni delle tubazioni sono necessari refrigeranti di densità medio-alta e le uniche alternative all'R410A sono i refrigeranti A2L, come l'R32 o il DR55.
L'utilizzo di refrigeranti A2L è strettamente connesso alle norme di sicurezza, tra cui le norme EN378 e ISO5149, nelle quali la quantità di refrigerante A2L consentita è stata notevolmente aumentata nelle ultime edizioni. Il gruppo di lavoro ASHRAE15 sta inoltre esaminando le future esigenze di refrigeranti a basso GWP. Tuttavia, sebbene queste norme di sicurezza siano imprescindibili, da sole non sono sufficienti. Le numerose normative antincendio locali hanno spesso ostacolato l'utilizzo di refrigeranti A2L. Sono in continua fase di studio fluidi innovativi e alternativi per la circolazione: l'acqua è una scelta ovvia ed è stata proposta anche la CO2. Il recente phase-down degli HFC, scaturito dal Protocollo di Montreal, ha messo in evidenza le opportunità, ma anche i rischi associati all'utilizzo di refrigeranti A2L. Negli anni a venire si delineerà probabilmente una direzione più chiara in merito alla scelta dei refrigeranti per i sistemi VRF.
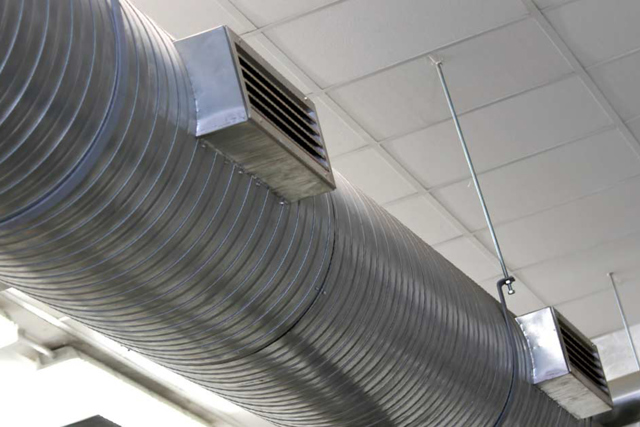
A una prima valutazione, la refrigerazione industriale (IR) sembra essere un settore che non pone particolari problemi per quanto riguarda i refrigeranti a basso GWP, ma non mancano potenziali insidie e c'è sempre spazio per ulteriori innovazioni. L'NH3 (ammoniaca) è stata il refrigerante preferito nella IR grazie al suo rendimento elevato e continua a essere utilizzata per soddisfare la costante domanda di refrigeranti sostenibili. Tuttavia, problemi di sicurezza possono potenzialmente limitare il successo dell'NH3, perché è tossica; nell'ultimo decennio si sono verificati alcuni gravi incidenti che ci hanno dato, come industria, importanti lezioni, come ad esempio quella di evitare prodotti che richiedono grandi cariche e la necessità di pianificare attentamente l'ubicazione degli impianti di dimensioni più grandi. Questo ha portato il settore della IR alla ricerca di modi nuovi e innovativi per ridurre la dimensione delle cariche. Un modo per ridurre le dimensioni della carica e aumentare l'efficienza è quello di combinare la NH3 con la CO2: la CO2 assume il ruolo di vettore termico e viene fatta circolare all'interno degli impianti di stoccaggio più grandi.
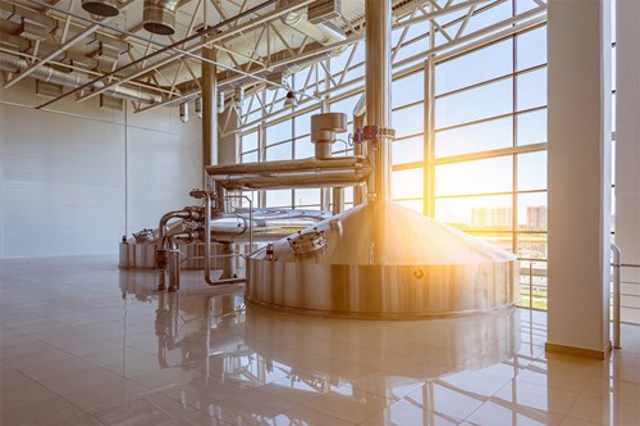
Le applicazioni di refrigerazione commerciale e di vendita al dettaglio di prodotti alimentari presentano esigenze diverse in termini di tipologie di sistemi e refrigeranti utilizzati. Tali applicazioni includono celle frigorifere, vetrine refrigerate, banchi frigoriferi e banchi a isola refrigerati, in soluzioni centralizzate o plug-in (circuiti frigoriferi ermetici o autonomi, con unità condensanti).
Le applicazioni di refrigerazione commerciale e di vendita al dettaglio di prodotti alimentari sono raggruppate in tre categorie principali.
Le applicazioni ermeticamente sigillate sono idonee all'utilizzo con refrigeranti a basso GWP e sono più sicure grazie alla ridotta quantità di carica. Molti di questi sistemi utilizzano già idrocarburi come l'R600a e il R290 e il phase-down dell'UE ha imposto valori di GWP inferiori a 150 a partire dal 2016.
Le unità condensanti hanno una carica di refrigerante compresa tipicamente tra 5 e 20 kg e la sicurezza in termini di infiammabilità è fondamentale, in quanto molti di questi sistemi sono accessibili al pubblico.
I refrigeranti a elevato GWP, come l'R404A, sono stati utilizzati per molti anni, ma una nuova alternativa è rappresentata dagli HFC classificati A1, che hanno un GWP inferiore del 60% rispetto a quello dell'R404A. Nondimeno, l’impatto delle temperature di mandata più elevate del compressore sul campo di funzionamento e l’impatto del glide del refrigerante sul rendimento frigorifero presentano nuove sfide. Riteniamo che il mercato si muoverà rapidamente verso un livello di GWP medio, intorno a 150, prima di ricercare soluzioni a GWP più basso come la CO2, l'R290 (idrocarburo) o le miscele HFO.
I sistemi DX centralizzati sono di gran lunga le applicazioni con il maggior consumo di refrigerante, a causa delle loro grandi dimensioni di carica e degli elevati tassi di perdite. Si stima che utilizzino oltre il 40% in più della quantità di refrigerante di base raccomandata durante il phase-down. Negli ultimi dieci anni, la CO2 è diventata un refrigerante idoneo e può essere utilizzata in diverse configurazioni di sistema:
Impianti transcritici in cui la CO2 viene utilizzata in tutti i circuiti (MT e LT). Gli impianti a CO2 transcritici sono stati anche il motore dello sviluppo di sistemi integrati di riscaldamento e raffreddamento, associando la scelta del refrigerante al tipo di sistema.
Sistemi indiretti in cui un rack di tipo chiller che utilizza gli HFC, gli HC o la NH3 raffredda la CO2 in un ricevitore, la quale viene poi fatta circolare nel circuito MT, raffreddando il circuito MT. Il circuito LT è anch'esso coperto da CO2 e condensa direttamente nel chiller nella parte superiore o nel circuito MT della CO2.
Sistemi in cascata in cui la CO2 viene utilizzata solo nel circuito LT ed è immessa in cascata nel circuito MT che utilizza HFC. Questo tipo di impianto utilizza ancora circa l’80% del refrigerante HFC impiegato in un sistema convenzionale
La sede geografica influisce sul rendimento energetico di qualsiasi sistema a causa della temperatura ambiente esterna. Gli impianti a CO2 transcritici sono noti per la loro straordinaria sensibilità alle temperature esterne. Tuttavia, gli ultimi sviluppi nel campo delle tecnologie di iniezione hanno aumentato notevolmente l'efficienza degli impianti a CO2 anche nei climi molto caldi, e nei prossimi anni ci aspettiamo che si verifichi una svolta nel mercato.
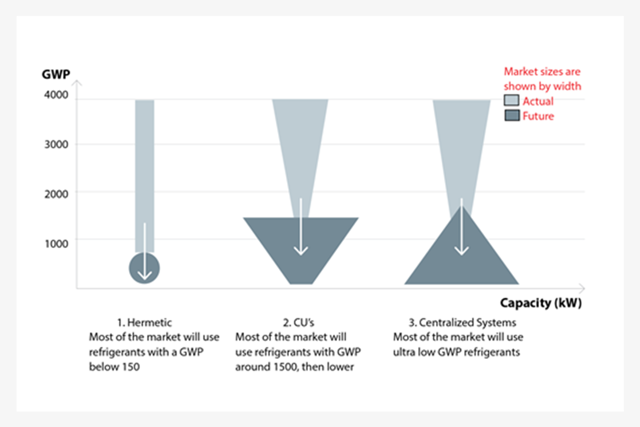
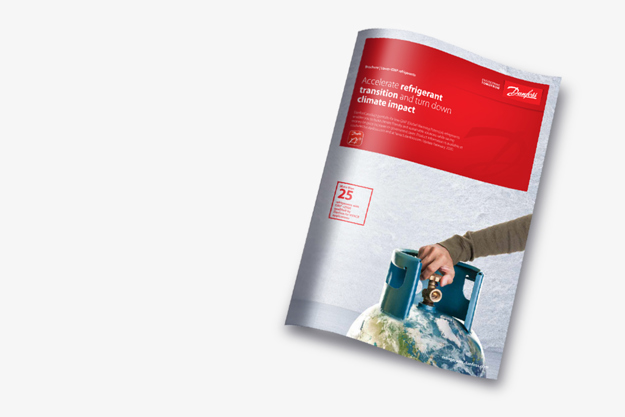
Maggiori informazioni sui refrigeranti
- Principali refrigeranti
- Refrigeranti naturali
- Sostituzione degli refrigeranti HFC
- Il Protocollo di Montreal
- Regolamento sui F-Gas (gas fluorurati) [UE]
- Piano di gestione della riduzione degli HCFC (HPMP) [Cina]
- Politica sulle nuove alternative significative (SNAP) [USA]
- Norme di sicurezza e codici edilizi
- Riduzione graduale degli HFC
- Eliminazione degli HCFC e CFC
- Domande frequenti - Modifica del limite dei refrigeranti infiammabili IEC 60335-2-89