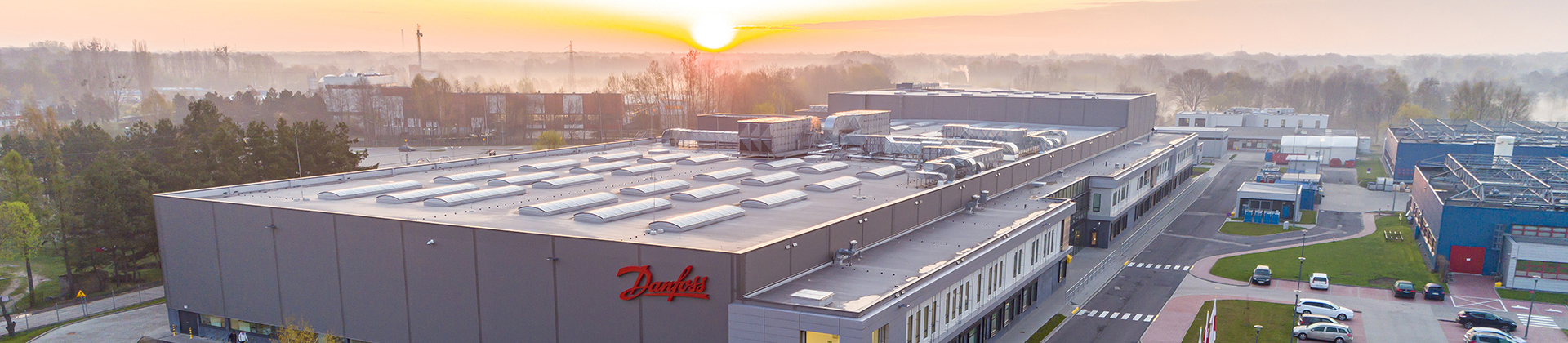

POLOGNE : Des approches innovantes de la production industrielle sont essentielles compte tenu des défis croissants associés au changement climatique et de la nécessité de réduire les émissions de gaz à effet de serre. Par conséquent, les fabricants s’efforcent de plus en plus d’utiliser des sources d’énergie propres et durables pour minimiser leur impact environnemental.
L’usine de Danfoss à Grodzisk Mazowiecki fait partie des installations de production les plus avancées de l’entreprise. C’est également la première installation entièrement alimentée par des sources d’énergie renouvelables. Un aspect important lors de la construction de l’usine a été d’optimiser l’efficacité, en utilisant des technologies de collecte et de traitement des données. Dans l’usine, le VLT® HVAC Drive FC 102 assure une ventilation efficace, avec une surveillance conditionnelle en connexion avec un service de surveillance à distance DrivePro®. Ces variateurs contrôlent le système de ventilation et de climatisation et recueillent également des informations sur les paramètres ou les situations d’urgence du système.
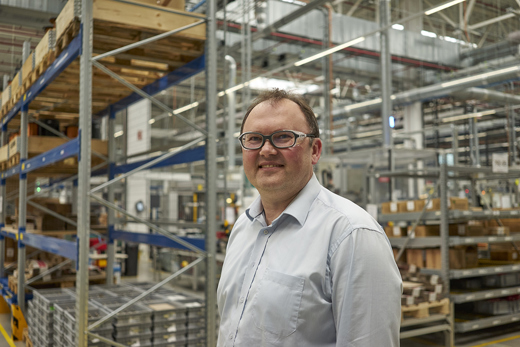
Le défi : plus de confort pour moins d’émissions de CO2
Dans le cadre du processus de conception de l’installation, il était important de garantir la sécurité des travailleurs et de la production. Les systèmes devaient répondre aux exigences en matière de maintien de paramètres définis dans les bâtiments pour garantir un environnement de travail confortable.
La suppression du risque de temps d’arrêt était également une priorité. Selon les estimations, un arrêt de la production coûte à l’usine 22 000 euros par incident. Ce chiffre se base sur des facteurs comme le coût des retards dans l'observation des délais de commande, l’achat de pièces de rechange et le coût des employés quittant leur poste de travail.
Danfoss vise également à atteindre la neutralité carbone d’ici 2030. Pour répondre à cet objectif et aux demandes des clients en matière de produits durables et respectueux de l’environnement, Danfoss s’est concentré sur l’utilisation de sources d’énergie renouvelables et sur l’optimisation de l’efficacité énergétique dans sa nouvelle usine. En réduisant sa consommation d’énergie et en optimisant ainsi son empreinte carbone, Danfoss a cherché à réduire les coûts tout en remplissant ses engagements en faveur de pratiques éthiques et respectueuses de l’environnement.
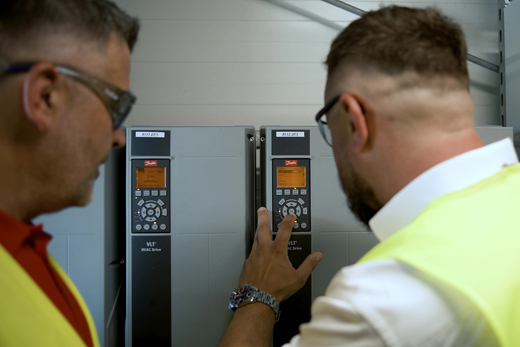
La solution : des variateurs intelligents avec surveillance à distance
Le système de ventilation et de climatisation de l’usine est contrôlé par des unités Danfoss VLT® HVAC Drive FC 102 avec surveillance conditionnelle (CBM) intégrée et service de surveillance à distance DrivePro®.
Le service de surveillance s’applique à 10 variateurs dans la plage de puissance jusqu’à 18,5 kW. Ces variateurs fonctionnent en conjonction avec l'informatique en nuage sur la base d'une norme Ethernet industrielle. La CBM améliore le contrôle en temps réel du statut d’isolation du moteur et du profil de charge. Les données historiques et en temps réel sont accessibles via un navigateur Web, ce qui signifie que le personnel de maintenance peut les analyser depuis n’importe où dans le monde.
Le service de maintenance de l’usine reçoit des notifications concernant d’éventuels écarts par rapport aux valeurs de référence. Cela permet au personnel d’identifier les situations qui peuvent présenter un risque de panne imminente, telles que des filtres encrassés ou une surcharge accrue, et d'y réagir précocement. Les notifications permettent également de rationaliser le processus de localisation des pannes.
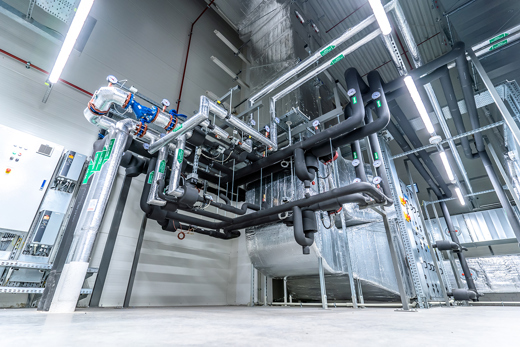
Résultat : 50 % de consommation d'énergie en moins
Pour l’usine, le principal avantage de la technologie des variateurs Danfoss, en particulier la CBM et la surveillance à distance, est la réduction du nombre de pannes et une meilleure disponibilité. Le service de surveillance à distance DrivePro® a amélioré l’efficacité de l’ensemble du service de maintenance, facilitant ainsi le processus de maintenance. En surveillant l’état de fonctionnement des machines, le personnel peut établir un plan détaillé de réparation et de maintenance. Les pièces de rechange sont commandées bien à l’avance. Par conséquent, il n’est pas nécessaire de stocker des composants redondants. La réduction de la charge sur les machines prolonge la durée de vie de l’ensemble de l’installation. Ainsi, le temps consacré aux différentes activités de maintenance a été réduit et la continuité de la production est maintenue. Les coûts d’entretien et de maintenance ont également diminué.
Grâce à une électrification complète, à l’utilisation de solutions éco-énergétiques (comme les variateurs Danfoss) et à l’utilisation d’énergie provenant de sources renouvelables, le nouveau hall de production de Grodzisk Mazowiecki est désormais neutre sur le plan climatique. Danfoss réduit ainsi les émissions et les coûts d’exploitation tout en veillant au bien-être de ses employés et en faisant un pas de plus vers ses objectifs climatiques.
Produits Danfoss installés dans ce projet
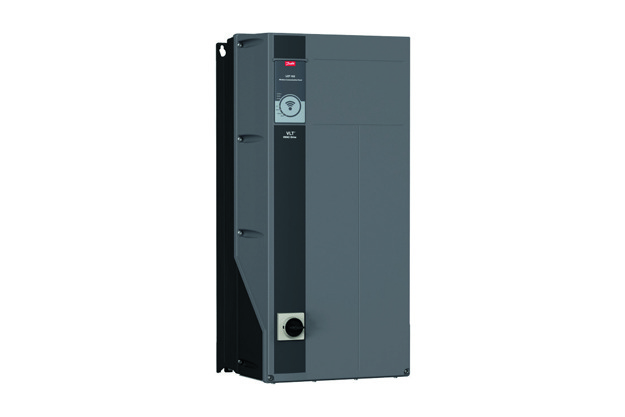
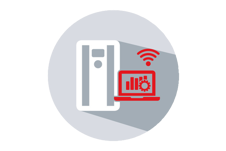