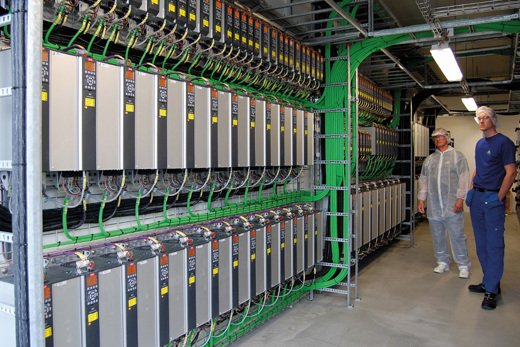
Los convertidores VLT® garantizan el máximo tiempo de actividad y alta precisión, además de reducir la demanda de energía de Arla, lo que también beneficia a los clientes.
En Arla Foods Ingredients, el usuario final es la próxima generación, pero antes de eso viene el fabricante de alimentos para bebés. La nueva planta que suministra un preparado de lactosa en polvo para lactantes —con un grado de lactosa superior al que era posible hasta ahora— cuadruplica la producción de lactosa en las instalaciones de Arla Videbæk de Dinamarca, con un ahorro de energía envidiable gracias a VLT® AutomationDrive.
Reducción del consumo de energía en las fases posteriores de producción
La nueva fábrica de lactosa de 80 000 t anuales de Arla Foods Ingredients añade valor hasta el punto de eliminar un proceso completo del cliente. El preparado para lactantes de alta calidad está listo para su combinación instantánea con otros ingredientes, lo que significa que los productores de alimentos pueden ahorrar un ciclo completo de mezcla y evaporación que consume mucha energía. Para conseguirlo, Arla garantiza unos niveles de calidad y seguridad alimentaria extremadamente altos, mediante un proceso estricto bajo un control de precisión. Los productores de alimentos consiguen un enorme ahorro de energía al poder eliminar un ciclo completo de mezcla y evaporación, por ejemplo, en la producción de alimentos para bebés o bebidas energéticas.
El reto para Arla es mantener la máxima calidad y un volumen anual de 80 000 t en la planta de preparado de lactosa para lactantes, a la vez que se mantiene por delante de los cada vez más ambiciosos indicadores clave de rendimiento basados en la huella de carbono, entre ellos:
- Consumo de agua: litros por kilo de polvo producido
- Energía consumida: kW/h por kg de polvo producido
Ganar la carrera energética
En su propia fábrica, Arla también está ganando la carrera energética, con un ahorro de energía del 5-15 % gracias al controlador VLT® instalado en todas y cada una de las bombas y los motores de los ventiladores, en comparación con el funcionamiento directo en línea (DOL).
Los motores representan una gran parte de todo el consumo de energía de la planta y, por lo tanto, se presta especial atención a la clase de eficiencia y a una mayor optimización mediante el control de los motores con convertidores VLT®. «Todos nuestros motores son asíncronos. Prestamos atención a la Directiva sobre diseño ecológico y fabricamos motores IE3 o IE4. Elegimos el mejor motor para la tarea, que satisfaga las necesidades de rendimiento sin excederlas».
«Hemos comenzado a utilizar la función de optimización avanzada de energía (AEO) en el FC 302 y a medir el consumo de energía a través de PROFIBUS. Sin embargo, normalmente necesitamos medir el rendimiento de toda la planta, no solo del convertidor de frecuencia, y eso lo hacemos midiendo la energía de cada sala de control. En el futuro, la nueva plataforma Carbon Desktop para Arla medirá toda la energía consumida a nivel de componentes, incluidos los convertidores VLT®».
Un convertidor de frecuencia para toda la planta
«En la medida de lo posible, todos nuestros motores están controlados por convertidores de frecuencia VLT® AutomationDrive. Y hay buenas razones para ello», explica Knud Rahbek:
- Nos hemos acostumbrado a este convertidor de frecuencia y nos hemos hecho expertos en el uso de las capacidades que ofrece esta unidad en particular. No nos sentiríamos seguros utilizando toda la gama de funciones que ofrece el convertidor si no lo conociéramos bien.
- Como resultado, algunos de nuestros electricistas se han vuelto increíblemente hábiles y sacan el máximo partido a la comunicación PROFIBUS.
- Nuestro equipo no tiene miedo de tocar el convertidor, ya que este dispone de una interfaz intuitiva.
- La formación del nuevo personal resulta mucho más fácil cuando solo se tiene que enseñar un sistema. Los nuevos electricistas tienen la oportunidad de aprender junto a un miembro del equipo en sus comienzos. Luego, se les asigna la tarea de configurar la lista de parámetros de 15 a 20 convertidores al mismo tiempo, bajo supervisión. Se trata de una situación real, en la que todo debe funcionar bien y se trabaja bajo presión. Si el electricista comete un error, tiene que descubrirlo él mismo».
En palabras de Simon Arentoft, gerente de mantenimiento:
«Tenemos una persona de contacto para los temas relacionados con los convertidores y sabemos a quién llamar en una situación de urgencia. Podemos confiar en que Danfoss responderá rápidamente, y esto significa que podemos reaccionar con la misma rapidez para evitar retrasos en la producción, en caso de problemas.»
Almacenamiento de alta eficiencia
Con un solo tipo de convertidor instalado en toda la planta —EL FC 302—, la logística relativa a los repuestos se reduce al mínimo absolutamente necesario. Con unas existencias increíblemente reducidas de tan solo ocho unidades (una para cada tamaño de alojamiento de hasta 90 kW) se puede prestar servicio a todo el parque de convertidores de frecuencia instalado (1400 unidades). Así, es comprensible que los costes de almacenamiento sean notablemente bajos en relación con el volumen instalado. El nivel de existencias sigue siendo suficiente para cambiar un convertidor, realizar la reparación in situ y encargar con precisión el convertidor de recambio correcto en cualquier momento.
¡No pares nunca!
Un requisito fundamental de las operaciones de Arla es trabajar sin interrupciones. Aún así, la sustitución de un convertidor de baja a media potencia no se cubre con convertidores redundantes. La sustitución de un convertidor dura 20 minutos, durante los cuales la producción continúa a un volumen ligeramente reducido, lo que resulta más rentable que utilizar unidades redundantes.
Sin embargo, para el cambio de los convertidores de alta potencia, como los que controlan los enormes ventiladores de las torres de ventilación, la parada de la producción es inevitable.
«La sustitución de unidades con una potencia superior a 90 kW está cubierta por un técnico de guardia las 24 horas del día, de acuerdo con el contrato de mantenimiento. Sin embargo, en los últimos cuatro años no hemos tenido ni una sola llamada de mantenimiento urgente», señala sonriendo Simon Arentoft.
La experiencia anterior demuestra que la instalación de convertidores FC 302 en toda la planta mejora el tiempo de actividad, debido a las ventajas de las funciones de protección contra la sobrecarga del motor. La estrategia de instalar los convertidores en salas de control en lugar de armarios también permite un tiempo de actividad fiable y una reducción del consumo energético. Al estar instalados en salas de control, los FC 302 son fáciles de ventilar y tienen una vida útil más larga, además de ser fácilmente accesibles para los técnicos de mantenimiento.
Contrato de mantenimiento de DrivePro®
El mantenimiento interno corre a cargo de un equipo de 30 técnicos expertos y se complementa con un contrato de mantenimiento con Danfoss. Knud Rahbek subraya que, cuando surge un problema, es vital poder confiar plenamente en la respuesta rápida de un técnico de mantenimiento. Por lo tanto, Arla exige —y recibe— un elevado nivel de servicio de Danfoss, tal y como se especifica en el contrato de mantenimiento suscrito.
Aspectos destacados
- Revisión de mantenimiento periódica de todos los convertidores de frecuencia, incluida la transferencia de datos al LCP
- Descuento en los cursos de formación de Danfoss para el personal de Arla
- Técnico de mantenimiento de guardia las 24 horas para solicitudes urgentes
- Servicio de entrega en 24 horas para convertidores de recambio
Arla Foods Ingredients Group
La fábrica de lactosa de Videbæk (Dinamarca) consume 120 GWh de electricidad al año. Por lo tanto, un ahorro de energía del 15 % anual en los costes energéticos es de enorme importancia.
Hay instalados 1400 convertidores VLT® AutomationDrive FC 302 de Danfoss, con una potencia nominal de 0,37 kW a 630 kW.
La máxima calidad vale la pena
La lactosa de alta calidad de Arla supera incluso los más estrictos estándares internacionales de calidad, garantizando así la seguridad alimentaria en todo momento. La lactosa de mezcla seca reduce eficazmente los costes de producción del usuario final, a la vez que ofrece una gran flexibilidad de producción que aumentará la capacidad del usuario final hasta en un 25 %. Gracias a los procesos de producción altamente eficientes, estos beneficios tangibles se consiguen de forma totalmente neutra en cuanto a las emisiones de CO2.