SUDÁFRICA: BMG Electronics utilizó variadores de Danfoss para apoyar a DryTech International en el desarrollo de un alimentador de tornillo húmedo único para su uso en una operación de platino que comprende una mina, una planta de procesamiento y una fundición. Esta solución mejora la confiabilidad con una sincronización elegante sin servocontrol de movimiento, reduce los costos y también facilita el tiempo de mantenimiento.
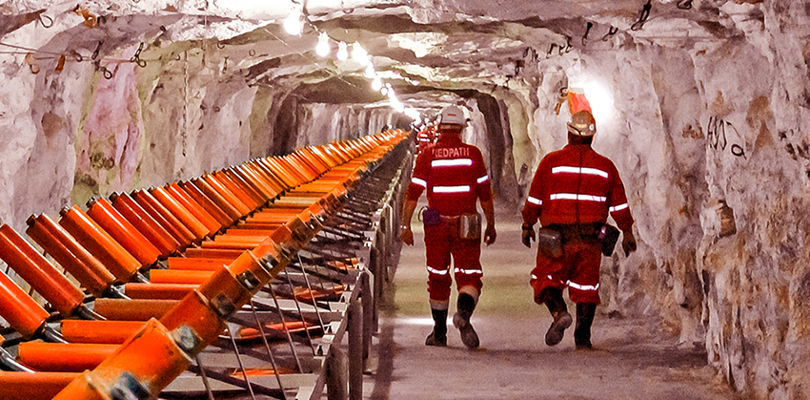
Descubra cómo BMG Electronics utilizó los variadores Danfoss para ayudar a DryTech International a desarrollar un alimentador de tornillo húmedo excepcionalmente eficiente.
Desafío: el material inusual requiere una solución única
DryTech International desarrolló el alimentador de tornillo húmedo para esta planta para hacer frente a las características inusuales del material que se procesa a partir de metales del grupo del platino (PGM), cromo y metales básicos. El material es extremadamente pegajoso, con una consistencia como la arcilla, y necesitaba ser transferido sin problemas a una secadora. Además, este material se recibe no solo de minas dentro del área inmediata en la provincia de Limpopo, sino también de minas en la provincia de Mpumalanga en Sudáfrica, a más de 300 km de distancia. Durante el tránsito, algunos compuestos se secan, mientras que otros permanecen húmedos.
Desde la perspectiva del diseño mecánico, los engranajes necesarios para el alimentador serían de gran escala, lo que plantearía algunos desafíos prácticos cuando se trata de encajar físicamente en la sincronización de la unidad sin que los tornillos choquen. Los engranajes más grandes también aumentarían sustancialmente los costos de los alimentadores de tornillo húmedo. La facilidad de mantenimiento era otro requisito de la planta. El rendimiento necesario del primer alimentador de tornillo húmedo estaba entre 30 y 40 toneladas por hora, con 15 toneladas por hora requeridas para el segundo alimentador.
Solución: ejes de tornillo sincronizados
![]() |
![]() |
![]() |
Modelo 3D de alimentador húmedo sin protectores | Modelo 3D de alimentador húmedo con protectores | Configuración del alimentador de tornillo húmedo DryTech con unidades FC 302 |
DryTech construyó una máquina de prueba para probar la aplicación, y la prueba mostró que un eje de tres tornillos era la solución más efectiva. Aunque durante la prueba, los tres ejes de tornillo estaban unidos mecánicamente entre sí, el cliente prefirió una solución con ejes independientes, sincronizados electrónicamente mediante unidades VLT® AutomationDrive FC 302 que controlaban un motor/reductor de 22 kW en cada eje. Este era un requisito crítico, ya que los tres ejes independientes deben girar de manera coordinada para ayudar a prevenir daños mecánicos. Por ejemplo, si uno de los motores, cajas de engranajes o ejes se sobrecarga y reduce la velocidad del motor, debe ser detectado por una función de desincronización y todos los ejes del tornillo deben detenerse. Una vez que se soluciona el problema y la aplicación se recupera manualmente, la aplicación vuelve automáticamente a la posición sincronizada correcta en el arranque, en lugar de tener que devolver el eje a la posición inicial manualmente.
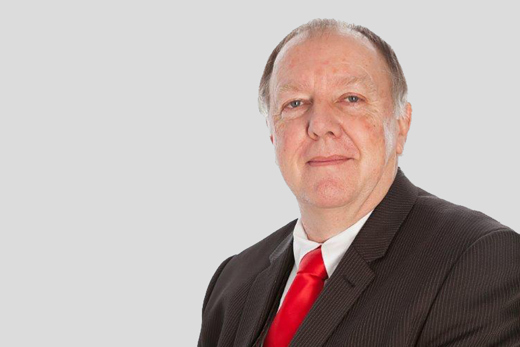
"La oferta de Danfoss VLT® AutomationDrive FC 302 proporcionó la solución ideal para este cliente, debido a su alternativa innovadora al enfoque tradicional de servocontrol para operaciones de posicionamiento y sincronización. Los variadores se adaptan a las aplicaciones a través de una parametrización simple". explica Stephen Brown, Gerente de Desarrollo de Negocios Mineros de Danfoss Turquía, Medio Oriente y África
Durante el funcionamiento normal, la carga en cada variador es relativamente ligera, a menos del 50 por ciento del par motor a plena carga (FLT), pero debido a la consistencia pegajosa del material, hay momentos en los que se producen cargas más altas. Esto ha demostrado ser especialmente cierto durante las condiciones de arranque o las condiciones de velocidad de alimentación baja. Los variadores de 22 kW con motores de 22 kW están bien preparados para hacer frente a estas condiciones, adaptando constantemente la potencia a la carga. Los motores están montados sobre la caja de engranajes que impulsan cada eje de tornillo, impulsando la caja de engranajes a través de una transmisión por correa.
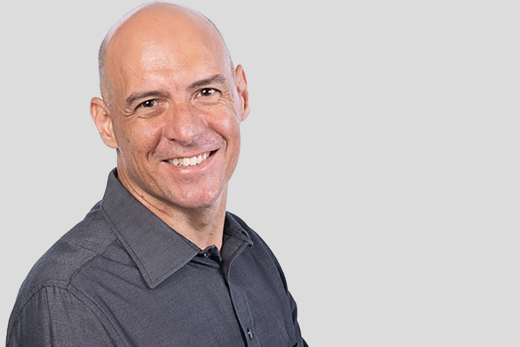
“Necesitábamos la flexibilidad para poder ajustar la relación de la polea de la correa durante la puesta en marcha para establecer la velocidad máxima y, por lo tanto, la tasa de rendimiento del alimentador. Esto también evita daños mecánicos en la correa, que fallará primero”.
- Riaan Van Niekerk, portavoz de DryTech
Control más estricto de velocidad y operación
La aplicación final puesta a punto por Juan Lerm, Técnico de Servicio de Campo de BMG Electronics, consta de tres tornillos conectados a los motores de 22 kW y reductores. El motor maestro (motor central) está controlado por un VLT® AutomationDrive FC 302 con PROFIBUS® y opciones de codificador. El Variador de Velocidad maestro con red PROFIBUS es el sistema de control que controla el funcionamiento y la velocidad de este motor según los requisitos del proceso. El motor maestro está equipado con un codificador para aumentar su respuesta de par dinámico, y el eje de este motor tiene un codificador de referencia para medir la velocidad de rotación real del eje del tornillo.
Cuanto mayores sean los pulsos por revolución (PPR), mejor será la sincronización, ya que los incrementos están más cerca entre sí, lo que aumenta la resolución de la retroalimentación.
“En esta aplicación usamos codificadores absolutos multivuelta 8192 PPR”, explica Mick Baugh, Gerente de Electrónica, División Electromecánica, BMG. "Cuando el alimentador húmedo necesita funcionar, da un comando de 'inicio' al variador de velocidad (VSD) maestro a través de PROFIBUS®. El VSD maestro luego da las señales de inicio a los VSD secundarios".
Los dos tornillos seguidores están conectados a VLT® AutomationDrive FC 302 con una opción de controlador de sincronización VLT® MCO 350 también con PROFIBUS® para fines de supervisión. El codificador maestro está conectado a ambos MCO como una referencia maestra, lo que significa que las tarjetas MCO 350 monitorean la velocidad del eje maestro. El codificador seguidor está instalado en el eje del tornillo de los tornillos seguidores, y estos codificadores están conectados a cada MCO respectivo como una señal de retroalimentación.
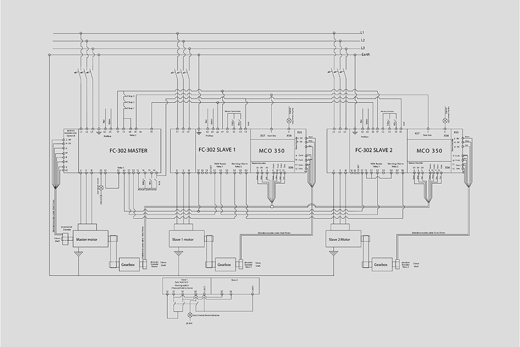
“La forma en que esto funciona es que el seguidor refleja efectivamente el codificador maestro: si el eje del tornillo maestro funciona a cierta velocidad, la tarjeta MCO del seguidor monitorea esa velocidad y la hace coincidir para que el eje del seguidor esté sincronizado con la referencia maestra, ” afirma Baugh.
“Si la aplicación se detiene en un estado de alarma, todos los motores se detendrán y los ejes del seguidor no estarán sincronizados. Cuando se da un comando de inicio, el VSD maestro tiene un retraso de cinco segundos, de modo que los tornillos se acelerarán y la aplicación volverá a sincronizarse por sí misma. Luego, el maestro subirá a la referencia de velocidad según la señal enviada en PROFIBUS”.
Si se ha realizado mantenimiento en la aplicación, los tornillos no estarán sincronizados. Se programó una sincronización manual para que los VSD pasen a una segunda configuración, y ahora cada tornillo se puede mover hacia adelante y hacia atrás para volver a colocar todos los tornillos en una posición de sincronización. Una vez que los tornillos están correctamente alineados, el técnico simplemente presiona el botón de sincronización para darle a la unidad una nueva posición cero. Cuando la aplicación se inicie de nuevo, se ejecutará de forma sincronizada.
“El hecho de que la opción del controlador de sincronización Danfoss VLT® MCO 350 no requiriera la escritura de un programa APOS especial también fue un factor decisivo importante”, agrega Baugh.
![]() |
![]() |
![]() |
Descubra las formas en que las unidades inteligentes agregan valor a sus operaciones: VLT® AutomationDrive FC 302 |
Obtenga más información sobre cómo aumentar la productividad con la sincronización, el posicionamiento y el control de levas de Danfoss | Descubra más soluciones de accionamiento para ahorros significativos de CAPEX y OPEX en minería y procesamiento de minerales |
Visite la página web del FC 302 | Lea el folleto de control de movimiento | Lea el folleto Minería |
Aplicaciones relacionadas
-
if (isSmallPicture) {
; } else if (isBigColumns) { } else { }Variadores de frecuencia para bombas de mineríaReducción de la carga térmica de la subestación y de la infraestructura de aire acondicionado, gracias al control de bombas refrigeradas por aire de Danfoss.
-
if (isSmallPicture) {
; } else if (isBigColumns) { } else { }Variadores de frecuencia para cintas transportadoras de mineríaLa flexibilidad para controlar la velocidad de las cintas transportadoras largas puede ayudar a optimizar todo el sistema, reducir los cuellos de botella y prolongar la vida útil del motor.
-
if (isSmallPicture) {
; } else if (isBigColumns) { } else { }Variadores de frecuencia para la ventilación de minasGarantizan un funcionamiento fiable y económico de los ventiladores, tanto en superficie como bajo tierra, con una fácil integración con los sistemas de ventilación según demanda (VoD).