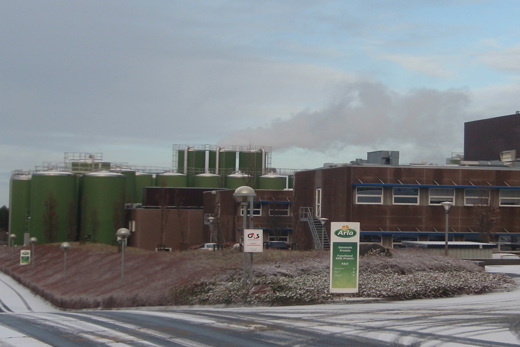
La producción de suero en polvo que consume energía en Arla Food Ingredients Group P / S en Videbæk, Dinamarca, se ha optimizado mediante el uso de variadores Danfoss VLT®. Ahorra energía, tiempo para el diseño del proyecto y hace que cientos de motores funcionen de manera más eficiente y dure más.
Para separar diferentes productos en el sitio de fabricación de suero en polvo en Arla Food Ingredients Group en Videbæk, los procesos exigen cientos de bombas, ventiladores, evaporadores, unidades de filtración y secadores por aspersión. Este es un proceso que consume mucha energía. Para ahorrar energía y dinero, Arla ha elegido un concepto para instalaciones de motores que incluye variadores VLT® de Danfoss.
En lugar de diseñar y construir nuevos paneles para arrancadores de motor, los convertidores de frecuencia VLT® (VLT® AutomationDrive FC 302 IP20) se instalan en las salas de control. ”Los accionamientos están conectados a todos los motores, nuevos y existentes, y los motores se benefician de todas las características de los accionamientos. Los sistemas de transmisión están conectados a un sistema de control computarizado, por lo que los empleados de Arla pueden controlar todo desde la pantalla de la computadora. Eso no era posible con el sistema antiguo. Siempre instalamos una tarjeta Profibus dentro del VLT® AutomationDrive con fines de control, lo que nos da la capacidad de acceder a los datos del proceso y a la información de las unidades. Esta es una gran ventaja ”, dice el gerente de mantenimiento de Arla Food Ingredients, Knud Rahbek.
Con un variador multipropósito, como VLT® AutomationDrive, que incluye filtros de armónicos y filtros EMC para cables de motor de 150 metros, todas las aplicaciones se pueden manejar con un tipo de variador VLT® y se puede acceder a todos los motores desde el control habitación.
Según Knud Rahbek, la fábrica también utiliza este concepto en proyectos de renovación. "Simplemente desechamos los paneles viejos y construimos la nueva instalación con variadores VLT® en conexión con los paneles de distribución"..”
Ahorros invertidos en nuevos convertidores de frecuencia
Antes de la instalación de los variadores VLT®, la fábrica tenía muchos motores con arrancadores DOL. Eso significó menos flexibilidad para el control de velocidad, más mantenimiento mecánico de los motores y menos control e información del motor y de la planta sin comunicación Profibus. También ocupó una gran cantidad de espacio en el panel. ”Los paneles ahora solo están diseñados para distribución, incluidos fusibles o disyuntores. Esto solo necesita la mitad del tamaño de un panel de arranque de motor normal y ahorra dinero y espacio en las salas de paneles ”, explica Knud Rahbek. El efectivo ahorrado se gasta en la compra de nuevos variadores VLT® de bajo consumo. Por lo tanto, el nuevo concepto de accionamiento no genera costos de inversión adicionales, sino que realmente ahorra dinero.y.
Gracias a este concepto, Arla también ahorra dinero en costes de ingeniería. Un ingeniero cuesta 750 dkk por hora, mientras que un electricista, cuyo trabajo es montar los variadores, solo cuesta 350 dkk por hora. Según Knud Rahbek, los electricistas de Arla han recibido formación para comprender los beneficios de los variadores VLT® y comprenden completamente cómo instalarlos y programarlos.hem.
Ahorro de energía en el foco
"Somos muy conscientes de la necesidad de ahorrar energía ya que somos una empresa intensiva en energía. Esto se debe al hecho de que el sitio de producción contiene más de 600 motores y ventiladores. La fábrica de Arla Food Ingredients en Videbæk utiliza alrededor de 50 millones de kWh de electricidad al año. Por lo tanto, un ahorro del 10% en los costos de energía es de gran importancia, ahorra una gran cantidad de dinero y hace una reducción significativa en la huella de carbono de Arla. Hemos agregado un variador VLT® a todos y cada uno de los motores y ventiladores y de esta manera hemos logrado un ahorro estimado entre un 5-15% de energía. Planeamos instalar 100 unidades más en nuevos proyectos durante los próximos tres años ”, explica Knud Rahbek.
Los accionamientos controlan las bombas accionadas por motor de modo que solo funcionen cuando sea necesario y solo a la velocidad requerida. Esto ahorra una gran cantidad de energía, ya que sin el control del inversor, los motores funcionarían continuamente. El control de velocidad en lugar del control de válvulas como antes reduce el tiempo de recuperación de la inversión en los variadores. En las unidades de filtración, por ejemplo, existen enormes beneficios adicionales de ahorro de energía debido al control mejorado de la temperatura a través del control de velocidad y flujo. La fábrica cuenta con numerosas unidades de filtración, ya que su función principal es aprovechar todos los elementos del suero que sobra de la elaboración del queso.
Acuerdo de DriveProTM Service
"Para nosotros es importante trabajar en estrecha colaboración con Danfoss. Si tenemos una avería en un variador VLT®, estaremos en funcionamiento nuevamente después de un máximo de 6 horas, debido al concepto de servicio de Danfoss. Las piezas adicionales están siempre a mano y son fáciles de adquirir. La estrecha cooperación con Danfoss también significa que nuestros empleados están muy familiarizados con los variadores VLT® y esto mejora la confiabilidad operativa ”, dice Knud Rahbek.
Arla Food Ingredients Group ha firmado un acuerdo de servicio DriveProTM con Danfoss que cubre los convertidores de frecuencia VLT® durante un período de 3 años desde su instalación. El socio de servicio de Danfoss, Styreg, verifica toda la base del VLT® instalada y lo documenta con la herramienta de software gratuita Danfoss VLT® Software Tool MCT10 para que, si ha habido advertencias o alarmas, se pueda evitar una avería adicional. Además, todos los parámetros de la unidad se descargan y las unidades se comprueban físicamente. En general, el acuerdo de servicio ofrece un mejor tiempo de actividad y reduce el número de costosas averías.
Resultados
La fábrica de Arla Food Ingredients Group en Videbæk, Dinamarca, utiliza alrededor de 50 millones de kWh de electricidad al año. Por tanto, un ahorro del 10% en costes energéticos es de gran importancia. 600 Danfoss VLT® AutomationDrive FC 302 se instalan en tamaños de 0,37 kW a 400 kW. Los proyectos futuros incluyen más de 100 unidades más durante los próximos 3 años.