New limits on sulfur emissions
Emissions from international shipping activities may have serious consequences for human beings and the natural environment. It is estimated that air pollution from marine activities alone accounts for up to 50,000 premature deaths every year in Europe.
For the last 60 years, IMO has been working on reducing the harmful emissions from shipping. In 1997 the MARPOL Convention was adopted to deal with air pollution. By January 2020, the emission control will be even stricter, when IMO starts enforcing a global limit for sulfur in fuel oil used for marine applications of 0.50% m/m (mass by mass). This will significantly reduce the amount of sulfur oxide emitted from ships to the benefit of people living close to ports and costs.
How to comply with the new regulation
To comply with the new requirements, the shipbuilding industry has several options:
- Use more expensive low sulfur fuels
- Install exhaust gas scrubber to wash out particles and sulfur
- Install engines running on natural gas
The relatively low price on HFO makes it attractive to install an exhaust gas scrubber, and for many shipbuilders, a hybrid scrubber system is likely to be the preferred solution to remove SOx due to its ability to switch between open or closed loop operations depending on the emission requirements at the specific location of the vessel.
When running the scrubber in closed loop mode, the recirculated scrubber water accumulates particles and sulfur that must be removed. The particles are separated in a hydro cyclone, whereas the sulfur is neutralized by adding an alkaline such as sodium hydroxide via a dosing system.
When choosing to use scrubber, it is required to monitor the exhaust, to ensure that the emissions limits are held and that the scrubber is working. This is done through Continuous Emission Monitoring Systems (CEMS) sensor solutions. CEMS sensor solutions can also be relevant for general enforcement of the 2020 Sulphur cap across the three above mentioned options in ensuring even compliance. Today, the burden of proof of compliance lies at authorities. In Denmark, enforcement of compliance is carried out through samples and sniffers. With this method, there is still loopholes and there is not a complete overview of emissions, and consequently not level playing field. Using CEMS solutions on all ships enables the possibility of full transparency of emissions which eases control of emissions, makes regulative enforcement efficient and ensures level playing field.
When to use stainless steel to protect the system
Corrosion by caustic sodium hydroxide at all concentrations is easily handled at room temperature with a variety of metals and alloys, including carbon steels. However, sodium hydroxide becomes more corrosive with increasing temperature and concentration.
The useful safe limit of carbon steel is approximately 65°C for caustic stress corrosion cracking (CSCC) and corrosion. The recirculated scrubber water can, however, easily reach temperatures above 65°C, and therefore a safer choice would be to use stainless steel.
Selective Catalytic Reduction systems for NOx may also require stainless solutions
Apart from SOx, nitrous oxides (NOx) are also subject to the IMO Tier III requirements. This means that it is mandatory to install or retrofit equipment/systems to reduce the NOx level to be in compliance with Tier III standards.
The emission of nitrous oxides can either be reduced by Exhaust Gas Recirculation or by Selective Catalytic Reduction (SCR), where Urea or Ammonia is sprayed into the exhaust gas before the gas passes through a catalyst. Due to the corrosive nature of ammonia and urea, all components of the dosing system should be either coated or made of stainless steel.
Furthermore, using emissions measurement equipment to measure and regulate the dosing of Urea to be more precise, reduces the risk of Ammonia Bi sulfate build-up and consequently avoidance of costly repairs and cleaning operations, as well as savings in Urea consumption.
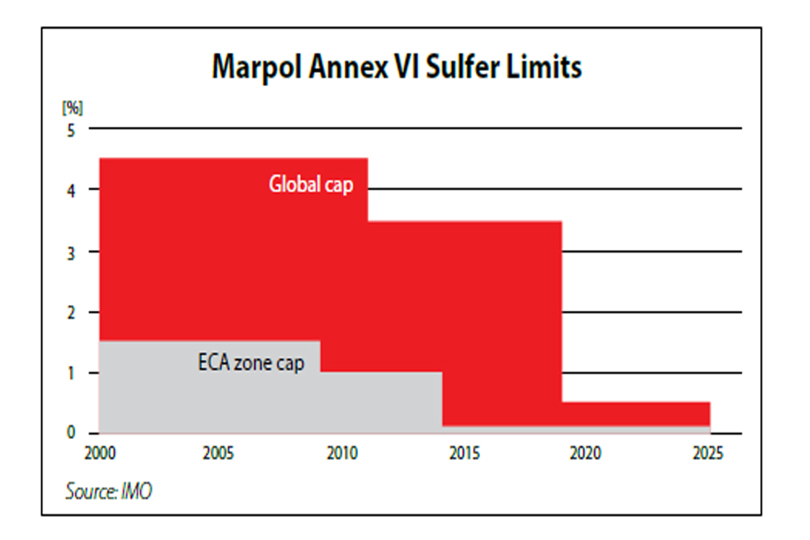
New regulation for exhaust gas
By January 2020, new restrictions of sulfur content in fuel oil were introduced. This article explores the challenge of sulfur emissions and potential solutions to comply with the new regulation.
Related product
-
if (isSmallPicture) {
; } else if (isBigColumns) { } else { }Heavy-duty temperature sensors, MBT 3250, 3252, 5250 & MBT 5252Heavy-duty temperature sensors for controlling cooling water, lubrication oil, hydraulic oil and refrigeration plants within general industry and marine applications. These temperature sensors are based on a standardized Pt 100 or Pt 1000 element, which gives a reliable and accurate measurement.
-
if (isSmallPicture) {
; } else if (isBigColumns) { } else { }EV212B Solenoid valves with FKM isolating diaphragm 2/2-way direct-operatedThe compact 2/2-way solenoid valve EV212B with an isolating diaphragm design ensures no fluid can enter the armature area meaning the valve can be used for aggressive fluids.