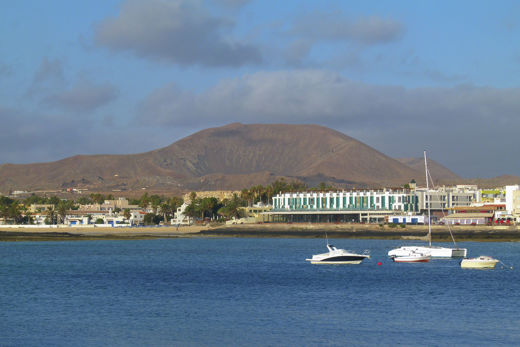
APP high-pressure pumps and iSave energy recovery devices help reducing energy costs at a water company suppying Corralejo on Fuerteventura
Veolia Water Technologies Iberica recently completed a retrofit for Suministros de Agua La Oliva, the municipal water company that supplies Corralejo on Fuerteventura in Spain’s Canary Islands. Built around Danfoss’s APP high pressure pumps and iSave energy recovery devices, the 2,000 m3 plant reduces the municipality’s energy consumption by 57%.
Related products
-
if (isSmallPicture) {
; } else if (isBigColumns) { } else { }High-pressure pumps for SWRO applicationsThe range of high-pressure APP pumps is optimized for both landbased, off-shore and marine sea water reverse osmosis applications. Available with or without motor.
-
if (isSmallPicture) {
; } else if (isBigColumns) { } else { }iSave® energy recovery devices for high-pressure membrane applicationsWith a 3-in-1 design that integrates highly effective isobaric pressure exchangers with positive displacement booster pumps and electrical motors, iSave® ERDs deliver big energy savings in small spaces. Covering train sizes from 200-3,000 m3/day