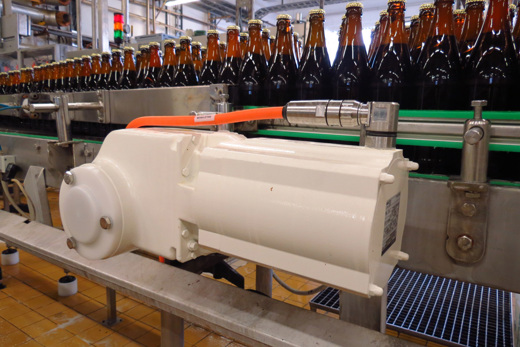
Breweries consume a lot of energy in running their processes. At Molson Coors’ Borsodi Brewery in northeastern Hungary, an upgrade of the gear motors on a glass bottle filling line has resulted in energy savings of 33-42%.
Improved reliability and productivity as well as reduced water consumption and emissions bring extra cost savings. The payback time of the retrofitting project will be less than three years.
The glass bottle filling line with a capacity of 35,000 bottles (0.33 liters and 0.5 liters) per hour had served the Borsodi Brewery for 24 years. Only a few motors were speed controlled by an AC drive, so the performance of the complete system was far less than optimal. As Molson Coors Group has set ambitious targets regarding energy and water efficiency and carbon intensity, a total of 36 old gear motors needed to be replaced with more efficient, speed-controlled motors.
“When planning the upgrade, our main attention was focused on energy savings to be achieved,” says Gábor Széman, Technical Service Manager, Borsodi Brewery. “We were introduced to the Danfoss VLT® FlexConcept® − which is a flexible, highly efficient conveyor drive system. Initial calculations showed an energy savings potential of approximately 40%, based on a comparison of the most inefficient, old gear motor of the filling line, and the high efficiency of 89.4% achieved by the VLT® FlexConcept®,” he continues.
The first step was to measure the energy consumption of an old bevel gear motor equipped with an AC drive. Then, the same measurement was repeated in the same location and under the same conditions with a VLT® OneGearDrive®, a highly efficient permanent magnet (PM) 3-phase synchronous motor controlled by a VLT® AutomationDrive FC 302.
“In different operating situations, the result was energy savings of 33-42%. This result fully supported the first theoretical calculation, as predicted. Based on this result we decided to go ahead with the upgrade, replacing all the old gear motors and AC drives with 36 new units of VLT® OneGearDrive and VLT® Automation-Drive FC 302,” says Mr. Széman.
Installation of the VLT® OneGearDrive® is easy and fast as it is mounted directly on the conveyor shaft, so chains are not required. “With the Danfoss VLT® FlexConcept® we control each motor and therefore, we have the possibility to optimize the production and also reduce losses. We are very satisfied with the performance of the new VLT® FlexConcept® drive system, and we are already planning a new retrofitting project,” Mr. Széman concludes.
When calculating energy savings and all other savings achievable in spare parts, cleaning time and operation costs, the payback time of the upgrade will be less than three years.
Cost savings and reduced emissions
In addition to the energy saving benefits, the Danfoss VLT® FlexConcept® provides the Borsodi Brewery with other useful advantages, such as:
Reduction in costs for spare parts and stock
Before the upgrade, a spare parts stock of more than ten different types of gear motors was required for maintenance purposes. Thanks to the Danfoss VLT® FlexConcept® enabling a reduced number of variants, the stock could be reduced to five units only (comprising VLT® OneGearDrive® and VLT® AutomationDrive FC 302).
Reduction in operation costs
The old gear motors caused system faults, which resulted in production loss and increased operation costs. Thanks to VLT® OneGearDrive®, the risk of system faults is considerably lower, which improves productivity.
Savings in cleaning time and water consumption
Thanks to the special design of the VLT® OneGearDrive®, which has no fan, no cooling fins, and has a special surface, the unit is very easy and fast to clean, so the brewery saves time, water, and detergents.
Reduction of CO2 emissions
The energy-efficient Danfoss VLT® FlexConcept® enables the brewery to reduce CO2 emissions by approximately 130 tons annually.
The old filling line was served by a total of 36 gear motors, bevel gear motors with induction motors with efficiency rating IE1, and a few mechanical adjustable gear motors.
About Borsodi Brewery
Borsodi Brewery is located in the village of Bőcs, near Miskolc, the capital of Borsod-Abaúj-Zemplén county in northeastern Hungary.
The brewery started beer brewing in 1973 with an initial production capacity of 875,000 hector liters. In 2012, the Borsodi Brewery was taken over by Molson Coors Brewing Company, an American Canadian brewery company which is one of the biggest brewers in the world.
The Hungarian beer market is around 5.7 million hector liters in total (2013).
Borsodi is one of the biggest beer producers in Hungary. Borsodi was the first producer of canned beer and non-alcoholic beer in Hungary.