The South Korean National Institute of Fishery Science is enjoying great fuel savings and 20-30% less emissions from its newest research vessel. Danfoss Drives supported STX Engine, the South Korean ship engine experts, in designing an innovative drive solution to optimize generator and engine performance on board. The Danfoss Drives solution was instrumental in helping the shipbuilder to comply with the IMO environmental regulations effective in 2020.
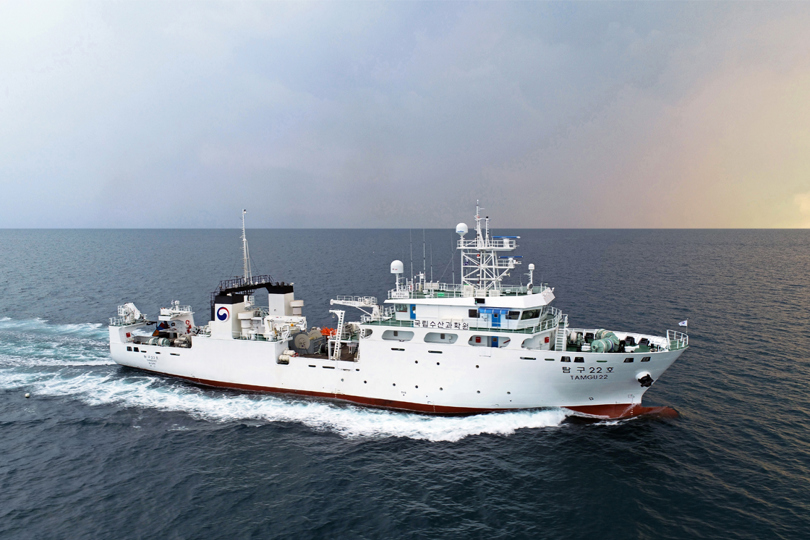
30% less emissions
Discover how a Danfoss shaft generator solution cut emissions by up to 30% on board the Korean research vessel, by comparison with conventional technology.
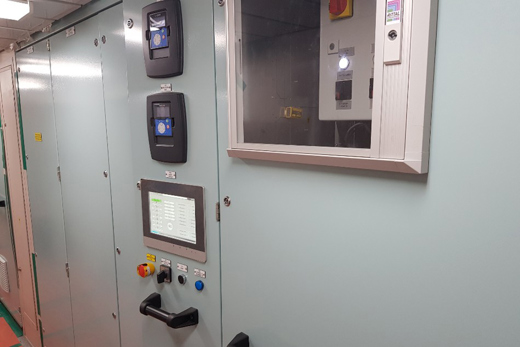
Optimal drive dimensioning saves space
In vessels, shaft generators are classified as generators. The design challenge was to double the standard shaft generator capacity, to meet the short circuit current requirements.
Danfoss was able to deliver a low complexity, high-performance shaft generator design. Installing a shaft generator onboard helped to meet emission targets by improving operational efficiency, and enabling designers to downsize the engine.
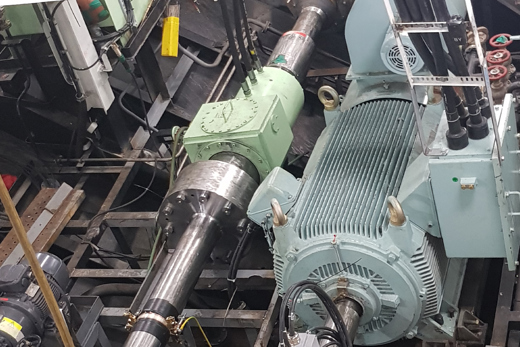
Electric propulsion for lower emissions
The Danfoss Drives shaft generator solution offers many advantages for ocean-going vessels:
- It uses asynchronous generators. This requires conversion of specifications from synchronous to asynchronous mode, made possible by local engineering and site trials
- Since the generator and engine are powered up via the Danfoss drive to provide power to navigation and ships, the result is an eco-friendly standard of operation with less noise, low vibration, lower energy consumption and lower CO2 and NOx emissions compared to ordinary ships
- During low-speed or part load operation, ships can run in electric propulsion mode without starting up the engine, for lower noise levels and reduced energy consumption
When operating the winch onboard a vessel, electric propulsion mode also protects the generator from overload. This approach helps to maintain the stability of the vessel, and improves reliability by avoiding overload which could lead to blackouts. In turn this extends component life expectancy.
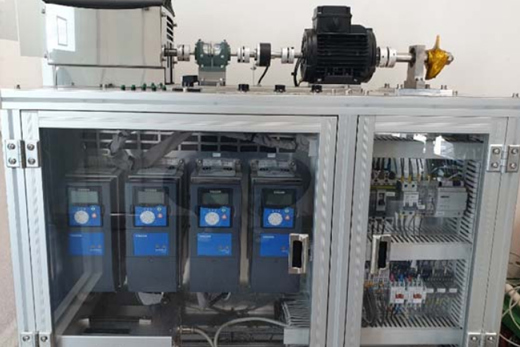
Engineering support and a working demo model
Danfoss conducted local engineering, project management, and local engineering commissioning. They ran a shaft generator demo system made by Danfoss Korea showing how to create an end-to-end system, and how to adapt the hybrid solution to this specific installation.
Since the shaft generator is classified as a generator onboard the ship, the conditions required for the general generator were applied.
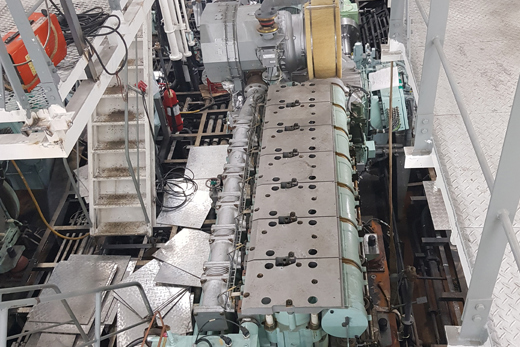
How does the shaft generator work?
The operation principle of conventional shaft generators used for controllable pitch propellers is to generate an electromagnetic field between stator and rotor using automatic voltage regulation (AVR) and an excitation unit. However, when running at low speed, the output voltage and frequency can reach such low levels that rated output voltage and frequency cannot be generated. Thus in order to drive the generator at rated speed, an excitation unit with an additional drive is required to boost the excitation voltage - and ensure the correct frequency.
An additional requirement of this project was power take in (PTI) functionality for the electric propulsion in order to control the speed of the propeller, which required an AC drive. Using an induction motor as generator combined with a Danfoss AC drive, the complexity of the synchronous generator with excitation system was eliminated, resulting in significant cost savings for commissioning and maintenance.
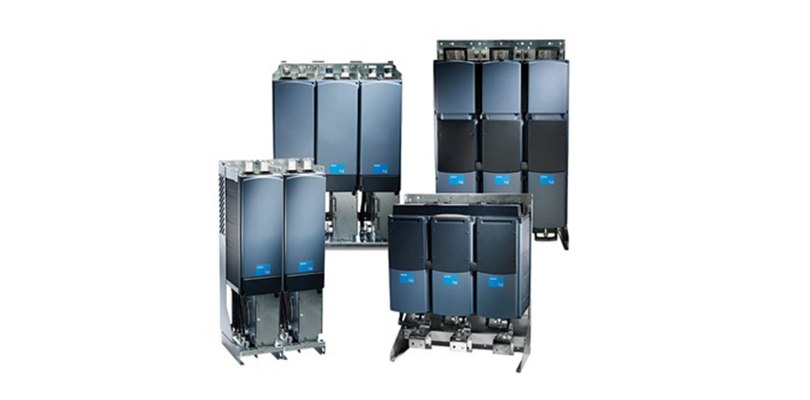
VACON® NXP Grid Converter
When applied to shaft generator solutions, this grid converter ensures that propulsion machinery is able to operate at various speeds. The shaft generator decouples the shaft from the mains, which allows better electrical quality and improved fuel economy. Additionally, power can either be taken from or entered into the propeller shaft. This is particularly useful for ships that often alternate their speeds as it creates fuel savings and minimizes exhaust emissions by up to 15%. It also creates an emergency mode meaning that the vessel can operate even if the main engine fails. Its importance cannot be overstated; use of a grid converter is a must in reaching emission targets.
Related Applications
-
if (isSmallPicture) {
; } else if (isBigColumns) { } else { }Decarbonizing the next-generation training ship, SkulebasNORWAY: The new training vessel at Maløy Fishing School uses less diesel and emits less CO2, while also meeting the rigorous demands of the fishing industry.
-
if (isSmallPicture) {
; } else if (isBigColumns) { } else { }Where smart ferry charging begins with a smart gridNORWAY: The Hareid-Sulesund ferry operations have reduced CO2 emissions by 7000 tonnes annually with the introduction of electric vessels. In transitioning ferries from diesel to pure electric power, powerful onshore support is essential, in the form of reliable infrastructure for rapid charging capacity and stable grid supply. The systems on board and on shore act as a single system – a sophisticated and competitive system developed by Norwegian Electric Systems (NES) using Danfoss technology.
-
if (isSmallPicture) {
; } else if (isBigColumns) { } else { }Future of the Fjords meets 2026 emission targets, todayThis world-first fully-electric carbon fiber vessel safeguards the pristine Norwegian fjord environment, ensuring zero emissions.
-
if (isSmallPicture) {
; } else if (isBigColumns) { } else { }VACON® drives power hybrid ferries 24/7NETHERLANDS: Passenger ferries bridge Amsterdam’s IJ River, keeping the city connected around the clock. Hybrid propulsion powered by VACON® drives ensures 24/7 uptime, smaller generator size, better air quality, less noise and easy maneuverability of the vessels.
-
if (isSmallPicture) {
; } else if (isBigColumns) { } else { }CCB Bergen saves 5,000 liters of diesel fuel dailyThe shore power supply system using VACON® NXP drive modules also annually reduces CO2 and NOx emissions by nearly 5,000 tons.