UNITED STATES: Somewhere off the coast of New Jersey, the Weeks Marine dredge Magdalen removes thousands of tons of sand off the seafloor and loads it into her hopper. The vessel then navigates to a spot where the shoreline was eroded and discharges the sand there, using slurry pumps powered by medium-voltage drives to reclaim a beach that storms had washed away. Since Weeks Marine commissioned the trailing suction hopper dredge (TSHD) in December 2017, Magdalen has been on the job up and down U.S. coastal waters—from reclaiming beaches in New Jersey to removing silt in the Mississippi Delta.
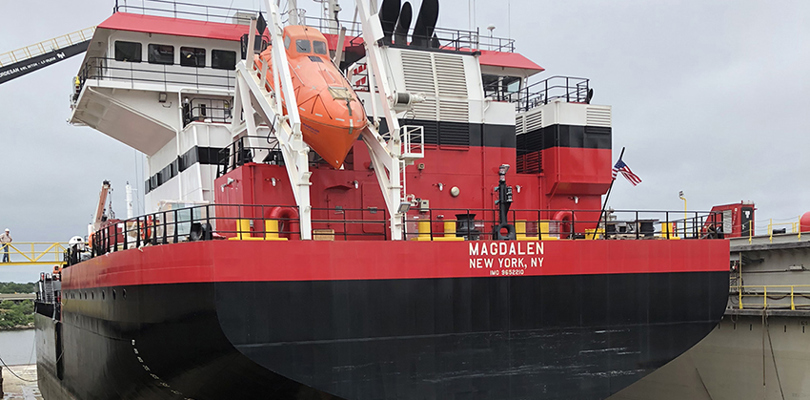
Learn how MAGDALEN pumps more than 6500 cubic meters of slurry every hour with best-in-class efficiency
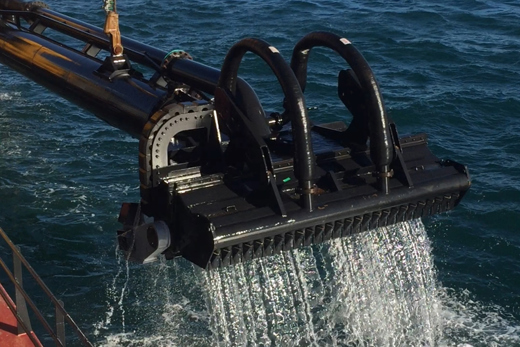
Dredging productivity needs controllable power
The Magdalen, which is built on a Royal IHC design, uses three VACON® 3000 medium-voltage (MV) drives that supply electric power to a high-efficiency Royal IHC dredge and booster pump. As a result, the dredge can load up to 8,550 cubic yards of material in about an hour. It then discharges the hopper by bottom dumping or pumping through miles of pipeline in roughly the same time.
During the dredging process, Magdalen lowers a suction pipe to the bottom of the seabed. The trailing draghead connected to the end of the suction pipe travels over the seabed like a vacuum cleaner’s nozzle. Jetting pumps supply water to the draghead to fluidize the sand being dredged. The centrifugal dredge pump creates vacuum in the suction pipe and discharges the material into the vessel’s hopper. While discharging its cargo load to shore, the centrifugal booster pump makes positive discharge pressure through a long pipeline, preserving slurry velocity and preventing material from clogging the pipe.
A modern, automated U-shaped console in Magdalen’s navigation bridge allows one person to navigate and control all dredging operations. Royal IHC’s Eco Pump Control Package among others uses artificial intelligence to optimize suction and discharge performance. The control package communicates with the Danfoss VACON® 3000 MV drives using Ethernet IP protocol. Pump speed increases or decreases when signals are sent to the MV drive to increase or decrease the frequency and power supplied to the AC pump motors.
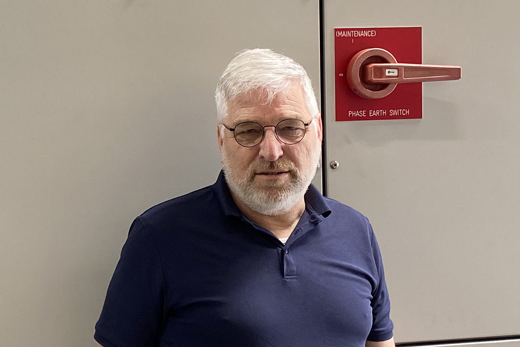
Best-in-class dredging efficiency
“Our goal for Magdalen was to achieve best-in-class dredging efficiency for conditions in the U.S.,” says Pieter Vos, IHC design engineer. Along with Simon Oomen he designed Magdalen’s electric installation/automation and specified the drives. “A fixed-speed pump motor can be employed where there is little variation in pipe length. But variable speed pump technology is required with discharge pipelines that experience significant differences between minimum and maximum loads. Danfoss VACON® 3000 MV drives let us handle large flow rate variations during the dredging process to avoid water hammer, clogging and other problems in the pipeline.”
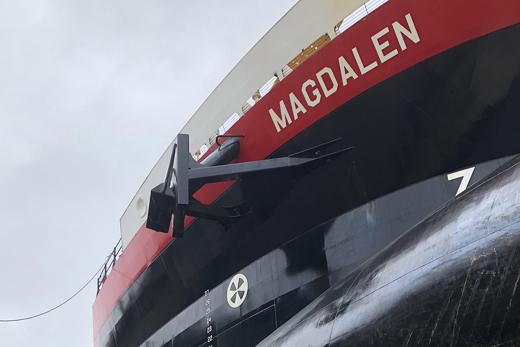
Intelligent control protects pump motors
The main propulsion diesel engines also drive the generators, which supply the electric power the Danfoss VACON® 3000 MV drives supply to the variable speed AC pump motors. The pumps include a 1.6 MW dredge pump and 3.2 MW booster pump, which is driven by two 1.6 MW electric motors in tandem formation. “The Danfoss VACON® 3000 MV drive controls the pumps far more effectively than a diesel engine and mechanical gears,” says Vos. “It responds quickly and precisely to the effects of temperature, pressure and forces on the pump motor. For example, if a large rock gets into the dredger, the control intelligence tells the Danfoss VACON® MV drive to quickly reduce motor RPMs to prevent motor burnout.”
Implementing variable speed control on dredge pumps is also more effective during dewatering operations when slower speeds are needed to remove water from the material in the hopper.

Smooth integration and reduced harmonics
Vos notes that Royal IHC was the first marine automation integrator to develop its own MV drive to run dredge pump(s) specifically for use in dredges: “MV drives are a better solution than conventional lower voltage (LV) drives, which require more cables and busbars in switchboards, and add weight, volume and heat.”
The VACON® 3000 MV drives also easily integrate with the ship’s electric system and power generation plant. The drive incorporates an active front-end (AFE) that reduces harmonics that could cause electrical distortions. The use of MV drives with AFE also makes it possible to optimize generator engine power to save energy.
In addition to VACON® 3000 MV drive technology, VACON® NXP drives were employed for the lower power voltage (LV) jet pumps and bow thruster. VACON® NXP drives provide a compact, high-performance control platform for both induction and permanent magnet motors in open and closed-loop control modes. For the bow thruster, the drive supplies electricity to the motor that drives a reduction gear directly connected to the thruster propeller. The thruster propeller is installed transversely in a thruster tunnel to improve maneuvering of the ship at slow speeds. The frequency-controlled electrically-driven propeller responds more quickly than conventional hydraulic steering systems and uses about half the energy.
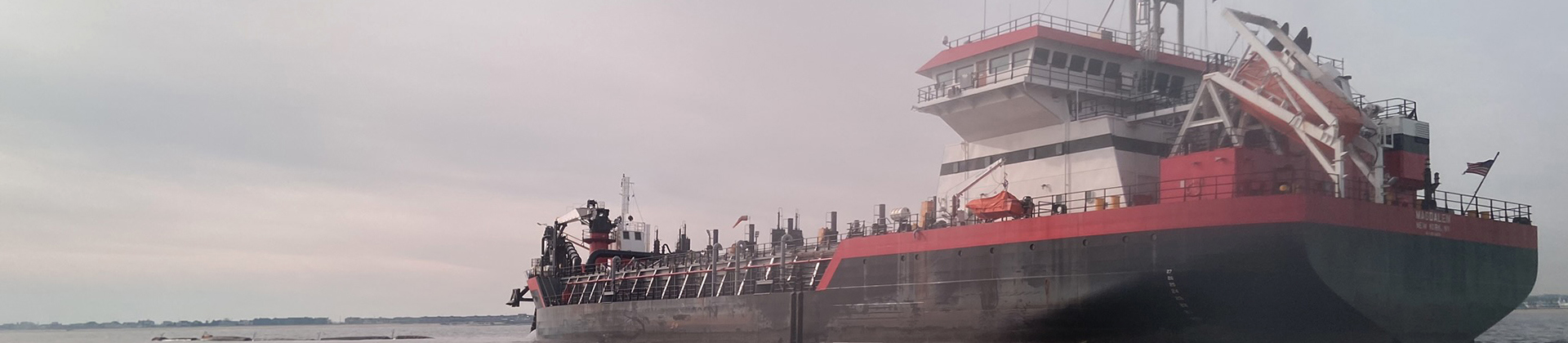
Unique robustness
“Competitors’ MV drives panels are made with standard industrial construction, which is not designed for the salty marine environment, the dust and dirt during vessel construction, and vibration and ship movement,” Vos explains.
“The VACON® 3000 MV drive was the only medium-voltage system available as totally enclosed, non-ventilated kit modules. This enabled Royal IHC to design a panel with a separate cable connection compartment – so, during construction, electronic compartments can remain totally enclosed in a non-ventilated chamber. Then, the modules are installed in a clean environment near the end of vessel construction. Open designs can be easily contaminated, which complicates cleaning and maintenance of electric components, costing hundreds of thousands of dollars.”
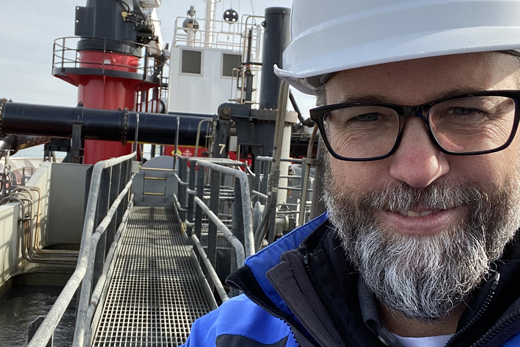
Extensive collaboration from factory pilot testing to onboard application
Magdalen launched in March 2017 with commissioning performed at Eastern Shipbuilding Group’s shipyard in October. Fully operational in December, the automation-and-drive project was the result of a collaborative design and implementation process.
Earlier in 2012, Danfoss developed and offered MV kits for pilot testing. Royal IHC placed its order in 2012, realizing the drive kit made it possible for Royal IHC to customize their own robust panels for the marine environment. The solution was developed in close cooperation with the Danfoss Marine Application Development Center (ADC). The ADC facilitated full-load factory testing of the drive panels and later included field testing. Vos was able to interact directly with Danfoss R&D engineers during factory acceptance testing (FAT) to demonstrate electrical and physical specifications were consistent with drawings, data sheets and project requirements.
In the enclosed VACON® drives, heat is removed through a closed-loop liquid-cooling system that employs a normal water and glycol-based heat transfer fluid and a heat exchanger, eliminating the need for a de-ionized water system. The low-harmonic filters of the AFE use forced air cooling.
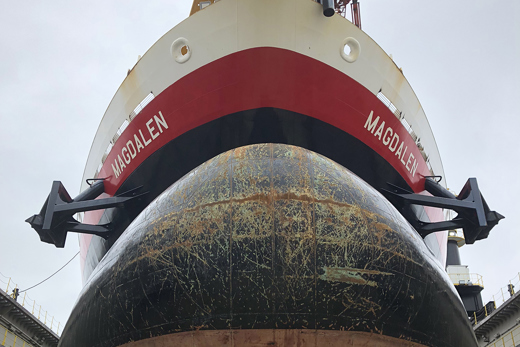
Customized solution ensures highest system efficiency
In the end, the team effort between Weeks Marine, Royal IHC, Danfoss, and Eastern Shipbuilding Group resulted in an innovative and effective drive solution. The VACON® drives handle the marine environment, provide a small footprint in the control cabin and deliver outstanding responsiveness for the operator on the bridge.
“On a complex project like this, it helps to have a supplier with complete LV and MV drive product lines, and also an MV drive kit package,” Vos concludes. “We were able to deliver a customized solution backed by the drive manufacturer complete with FAT testing at full electrical load at Danfoss premises nearby. As a result, we were able to deliver a drive solution with higher power efficiency, which translates into lower fuel costs and less maintenance.”
For Weeks Marine, it’s full speed ahead with Royal IHC’s custom solution using VACON® drives. According to Hans Blomberg, technical manager at Weeks Marine, “Royal IHC and Danfoss have helped Magdalen raise dredging efficiency to a higher level, saving energy and boosting productivity when excavating material from seabeds throughout U.S. coastal waters.”
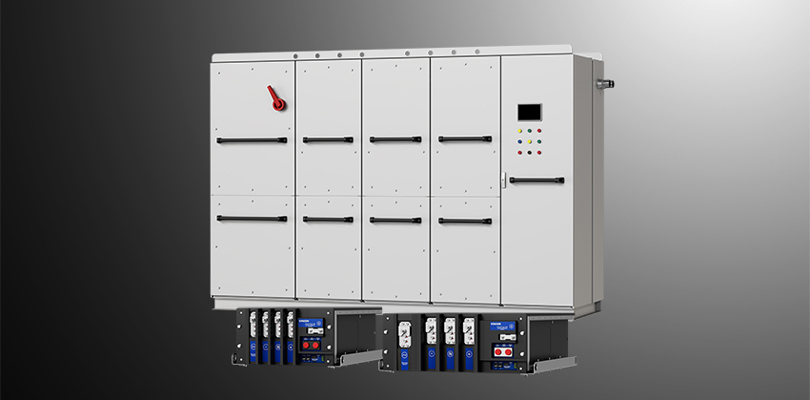
Individually tailored to meet the toughest medium-voltage requirements
Related applications
-
if (isSmallPicture) {
; } else if (isBigColumns) { } else { }Drives for marine power conversion and generationDraw upon expertise from Danfoss to optimize energy storage solutions using drives for power conversion both on board vessels, and in shore power supply for quieter and cleaner harbors.
-
if (isSmallPicture) {
; } else if (isBigColumns) { } else { }Drives for marine propulsion and thrustersFor more efficient operation and greater freedom in ship design, consider an electric-based main propulsion with engineering from Danfoss.
Related case stories
-
if (isSmallPicture) {
; } else if (isBigColumns) { } else { }MAGDALEN replenishes U.S. beaches with the power of VACON® 3000 medium-voltage drivesUNITED STATES: Somewhere off the coast of New Jersey, the Weeks Marine dredge Magdalen removes thousands of tons of sand off the seafloor and loads it into her hopper. The vessel then navigates to a spot where the shoreline was eroded and discharges the sand there, using slurry pumps powered by medium-voltage drives to reclaim a beach that storms had washed away.
-
if (isSmallPicture) {
; } else if (isBigColumns) { } else { }Royal IHC Scheldt River pioneers new environmental standards in dredging with flexible MV drivesA Danfoss medium-voltage drive solution boosts an inboard dredge pump and increases energy efficiency with a small footprint, minimum weight and low volume - while being robust enough to withstand the harsh marine environment.