ITALY: Digitalization in the refrigeration sector can help companies reduce their electricity consumption, improve system management and streamline maintenance. Digitalization can also contribute to reducing general site management costs, and optimizing systems to eliminate production inefficiencies. It helps to make companies like Centro Carni Company more competitive in today’s market, which is under constant evolution and transformation.
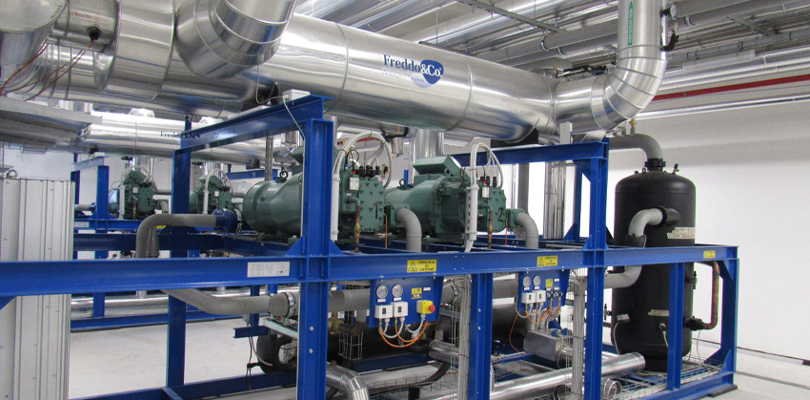
2 MW cooling capacity
Learn how the shock freezing process achieves maximum productivity with lower energy costs
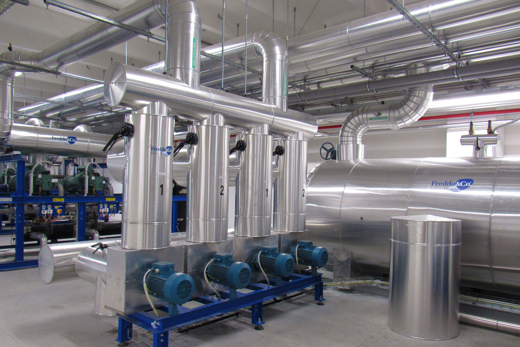
Renowned beef processor Centro Carni Company di Tombolo (PD) installed a new cooling system, designed and installed by industrial refrigeration system contractor Freddo & Co. The process handles 75 tons of raw material throughput every day. System requirements were clear:
- high yield
- no machine downtime
- guaranteed operator safety
- low maintenance costs
- automation and innovation
- sustainability
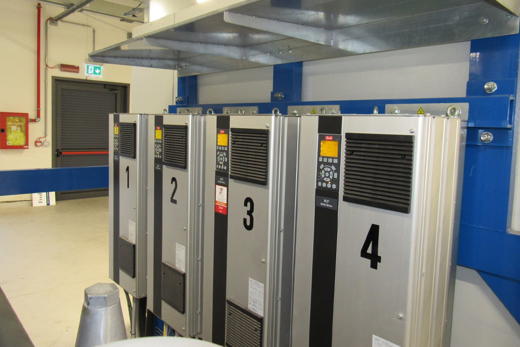
Fast return on investment
Technology and innovation are the focus of this cutting-edge project, implemented by the Vicenza-based company. As well as ensuring maximum productivity and quality, these technical solutions also ensure lower plant management costs in energy and maintenance. Using variable speed control can reduce power consumption by 30-40% for compressors, and by 50-70% for pumps and fans. This results in a faster return on investment, with major benefits for the company’s bottom line.
Freddo & Co chose Danfoss, as world- leading supplier of refrigeration products and solutions, as its technological partner. Danfoss supplied VLT® HVAC Drive FC 102 drives for compressor, pump, and fan control, as well as all refrigeration control components.
Danfoss drives are also equipped with innovative management and continuous motor-monitoring functions, which further reduce the management costs of the system. Danfoss VLT® HVAC Drive FC 102 units can operate continuously with no derating, even at temperatures of up to 50 °C, which makes them particularly suitable for direct use in the engine room.
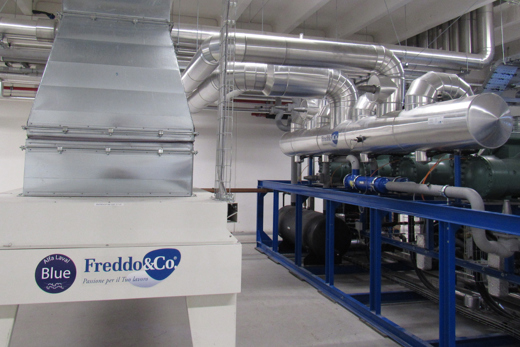
2 MW capacity for shock-freezing tunnels
The refrigeration system has a capacity of 2 MW and comprises a low- temperature direct-expansion plant for shock-freezing tunnels, equipped with four Bitzer screw compressors, each regulated by a 160 kW VLT® HVAC Drive FC 102 IP54 drive from Danfoss. The system is extremely compact and can be installed directly on-site or anywhere in the machine room. The drives require no additional protection, so the machine room electrical panels are more compact.
Freddo & Co has also installed drives on chiller systems for water: two 200 kW VLT® HVAC Drive FC 102 units, suitable for managing Bitzer screw compressors. Other smaller drives have been used for controlling the speed of evaporative condenser fans, pumping units, and air-handling units in processing room
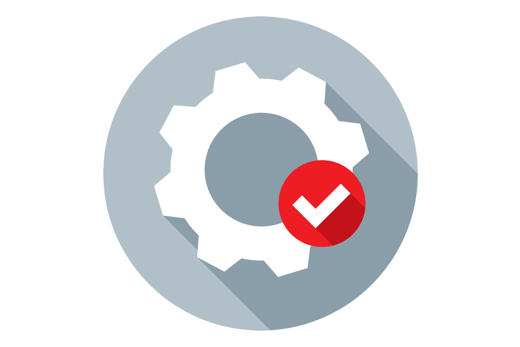
Ensuring non-stop operation
Freddo & Co’s plan for emergency operation is particularly interesting. If there is a fault on one compressor, the drive increases the frequency on the other compressor to 60 Hz, as opposed to the standard 50 Hz.
This change increases cooling efficiency by 20%, for the compressor which is still running. In practice, with one compressor stopped, the system will still be able to supply 90% of the total cooling power, thus ensuring continuity of on-site service and production, with a considerable positive impact on running costs.
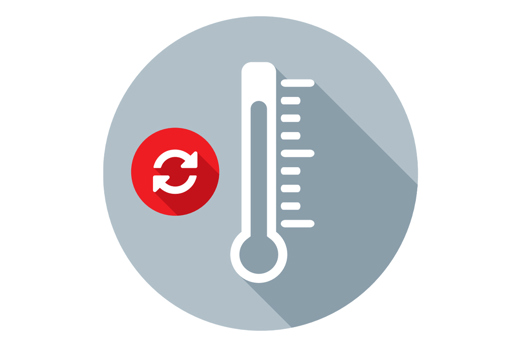
Adapting to external temperature
Freddo & Co has included an additional proprietary energy-saving function in this system, the NewCold®System, which exploits condenser fan control via the drive, to vary the condensation pressure setpoints by adapting them to the external temperature. For example, during the lower temperature seasons, this control method allows the compressors to run with lower condensing pressures, and thus with lower electrical absorption and higher cooling efficiency.
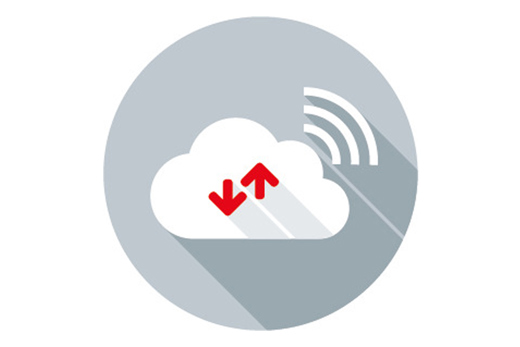
Remote monitoring
Freddo & Co has developed the Guardian system, which enables service operators to manage, monitor and program the different phases of system operation remotely. Danfoss drives can communicate in an advanced way with this system and use advanced algorithms to exchange essential data related to electric motors, alarms and parametrics. Moreover, if faults occur, Freddo & Co technicians can troubleshoot quickly or even resolve the problem remotely. Based on state-of-the-art technology in industrial refrigeration digitalization, the system completely fulfils all Industry 4.0 requirements.
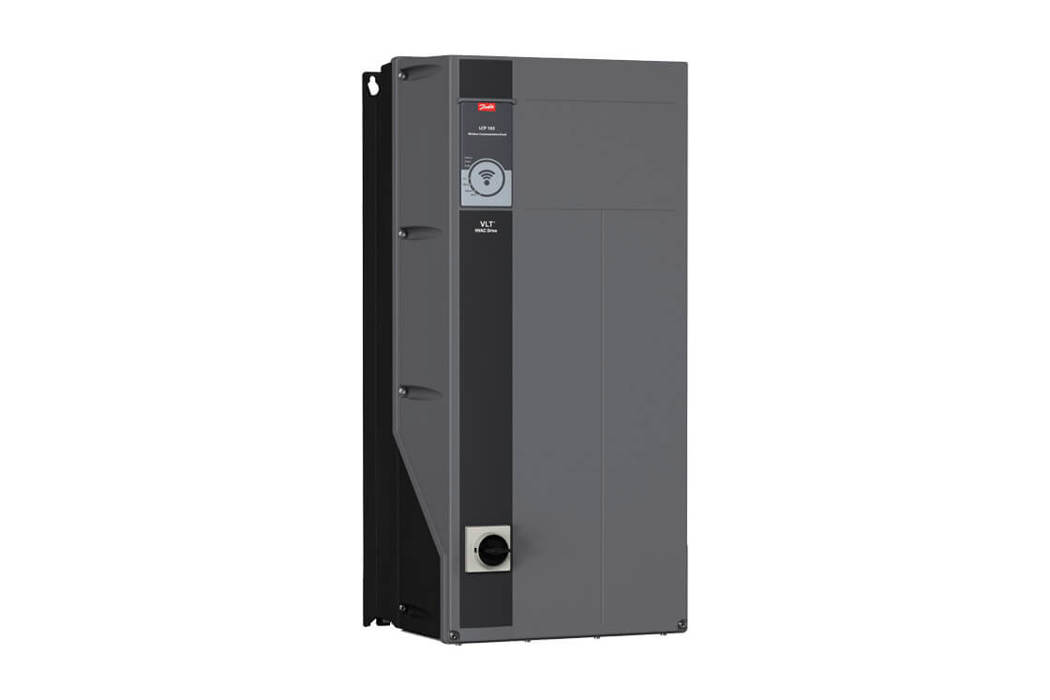
VLT® HVAC Drive FC 102 for intelligent compressor control
Related applications
-
if (isSmallPicture) {
; } else if (isBigColumns) { } else { }Drives for compressors in food and beverageCompressor speed control provides constant pressure regulation as well as reducing your energy consumption, especially for part-load operation.
Related case stories
-
if (isSmallPicture) {
; } else if (isBigColumns) { } else { }Refrigeration systems preserve apple quality using VSDs with integrated condition monitoring and DrivePro Remote Monitoring serviceITALY: At Rivoira Group, VLT® drives with built-in condition-based monitoring help preserve fruit perfectly by ensuring utterly reliable refrigeration.
-
if (isSmallPicture) {
; } else if (isBigColumns) { } else { }Digitalization drives energy savings at Centro Carni CompanyITALY: Digitized shock freezing systems helped Centro Carni Company improve productivity and quality, with less power consumption and more streamlined maintenance.
-
if (isSmallPicture) {
; } else if (isBigColumns) { } else { }85% startup energy reduction for Reindl KältetechnikVLT® Refrigeration Drive provides optimal control of the dehumidifier in the hay drying process.
-
if (isSmallPicture) {
; } else if (isBigColumns) { } else { }Unilever saves 25% energyVLT® AQUA Drive FC 202 maximizes pump efficiency and optimizes energy savings as part of boiler-house renovation project.
Contact us
For further information please contact us