The F-gas regulation in Europe and similar legislation in other parts of the world push for low GWP solutions in food retail refrigeration. CO2 is proving to be one of the most efficient low GWP refrigerants thanks to the unique properties of the gas combined with technological discoveries that pave the way for optimum utilization of these properties.
The advantages using CO2 is declining with increasing outdoor temperature and classical south border of CO2 applications has been regarded as the Alps. Most recently, Ejector technology shows potential to make CO2 systems competitive in warmer climates, too. Four test sites installed with the Danfoss multi ejector concept in Europe and Africa show that Ejectors are working as expected under varying conditions in different set-ups with efficiencies up to 30%. The tests also reveal how plant design must accommodate Ejector performance characteristics.
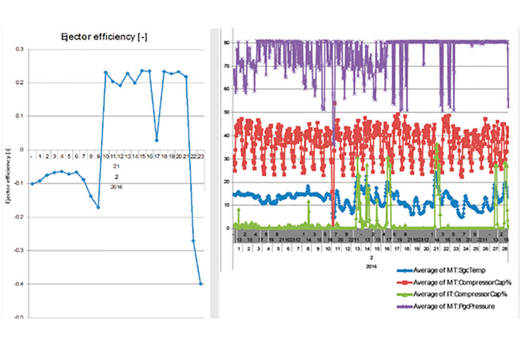
Test site 1
When running with heat recovery as is the case on site 1, the test results show that the Ejector is only running at long intervals. However, when the loads increase and the parallel compressors kick in, the Ejector wakes up and runs with up to 25% efficiency. From the test it can also be concluded that when running in heat recovery mode, it is important that the gas is not cooled too much in order to get full benefit of the Ejector.
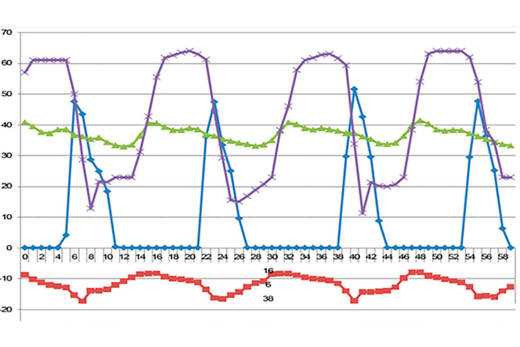
Test site 2
On site number 2, Ejectors are tested on a relatively big capacity refrigeration system – but with a low load. What becomes clear from the test is that if the compressor pack is oversized, the system becomes instable and the Ejector has limited effect. In other words, the compressor capacity needs to be adjusted in order to profit from the installation of Ejectors.
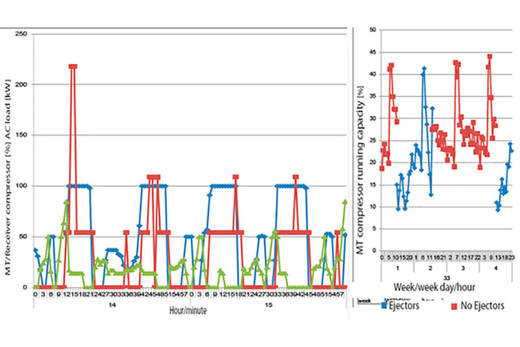
Test site 3
The supermarket in test 3 applies a large AC system in summer. Interestingly, the test case shows how the AC compressors with Ejector mounted in some periods t have the needed capacity to run the relatively small MT refrigeration system. The test demonstrates the potential in combined AC and refrigeration
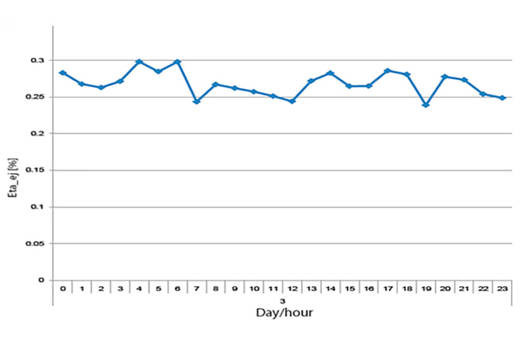
Test site 4
In the case of the supermarket in Africa, the documented efficiency of the Ejector reached 30%. When the Ejector is running, the receiver compressors take over the main part of the work, whereas when the Ejector is off, the MT compressors are dominant.
It is important that the system is adapted to ejector technology
The four tests under real supermarket conditions confirm how the plant design must be adapted to accommodate Ejector performance characteristics. Among the main findings are:
The compressor capacity steps must be adjusted to take full advantage of Ejectors
The Ejector pressure lift to the receiver has to be optimized in order to optimize the Ejector efficiency
What are the implications for energy efficiency?
Even though system energy efficiency when using the Ejector technology was not the main purpose of the test, some system efficiency output were detected. When calculating the energy efficiency based on the Ejector efficiency results, the energy saving potential of Ejector technology becomes evident. Among the results returned by the test are:
- At Site 4 - moving part load from MT compressors to Receiver compressors return energy efficiency improvements of at least 4% at 27°C.
- At Site 3 - when combining AC and refrigeration system the energy saving potential becomes even bigger. The test shows 10-15% energy efficiency improvements on the refrigeration system at ambient temperatures around 30°C.
In conclusion, the four tests performed by Danfoss confirmed that Ejectors are working as expected under varying conditions in different set-ups. The tests also show how the system design has to be tailored to the use of Ejectors to achieve maximum return on investment. In this way, the tests have brought the refrigeration community one step closer to implementation of Ejector technology as part of the effort to achieve sustainable refrigeration.
Torben Funder-Kristensen heads up the Public Industry Affairs department at Danfoss Cooling focusing on issues such as refrigerants, energy efficiency and new trends within the industry.