Decarbonization of the water industry comes down to energy efficiency
Our thirsty world requires an increasing amount of water for homes, industry, and agriculture. And the more water we use, the more wastewater we must treat. All this water usage requires energy: our global water-use cycle uses an estimated 1,000 TWh of electricity annually.
The “water-energy nexus” underscores the carbon impact of how we manage our water resources from conservation and sourcing to treatment and reuse. The decisions we make here are crucial both environmentally and financially.
Some water treatment methods, though energy-intensive, are essential for supporting millions of lives and livelihoods. Due to climate change and increasing water scarcity, for example, many communities rely on membrane processes to desalinate seawater. Similarly, we depend on membrane processes to treat some of our most highly polluted wastewater.
As our use of these processes grows, so does the importance of reducing their related carbon emissions. Conserving water and improving the energy efficiency of water treatment are both vital decarbonization strategies. At Danfoss, we’re continually working to reduce our own water consumption. And we’ve made it our business to help others reduce the energy intensity of their membrane-based water treatments.
Energy-efficient high pressure is key to decarbonizing membrane processes in water treatment
Reverse osmosis, nanofiltration, ultrafiltration, and microfiltration all force water at high pressure through semi-permeable membranes to remove impurities. Applications of these high-pressure membrane processes include seawater reverse osmosis (SWRO) desalination and zero liquid discharge (ZLD) wastewater treatment and many other purification processes widely used in the food, beverage, dairy, mining, and other industries.
While highly effective at removing dissolved salts and other contaminants, these advanced filtration techniques are energy-intensive, primarily due to the high pressure required to send water through membranes. The electricity needed for pressurization typically accounts for up to 70% of these process’s total energy consumption.
Improving the energy efficiency of these membrane processes is an effective way to reduce their carbon footprint. Fortunately, it also lowers their financial costs. Three technologies in particular can considerably reduce the energy required to pressurize water:
- Energy recovery devices (ERDs) reduce electricity consumption by up to 60% compared to systems without ERDs
- Energy-efficient membranes that increase permeate flux and reduce fouling reduce electricity consumption by up to 30% compared to less efficient membranes
- Energy-efficient high-pressure pumps reduce electricity consumption by up to 20% compared to less efficient pumps
Navigating the decarbonization journey: One shared goal, many starting points
By choosing high-efficiency pumps, ERDs, and membranes, equipment specifiers can significantly advance decarbonization efforts. These technologies not only reduce the carbon footprint of plants throughout their lifetimes but also substantially reduces operating expenditures for plant operators and end users.
For new plant constructions, incorporating these technologies from the design phase ensures energy-efficient operations and compliance with evolving environmental regulations.
For existing facilities, upgrades that improve energy efficiency are equally vital. Retrofitting existing plants with energy-saving technology can lead to considerable reductions in greenhouse gas (GHG) emissions and operational costs. The return on investment for such updates is often realized within a surprisingly short payback period due to lowered energy expenses.
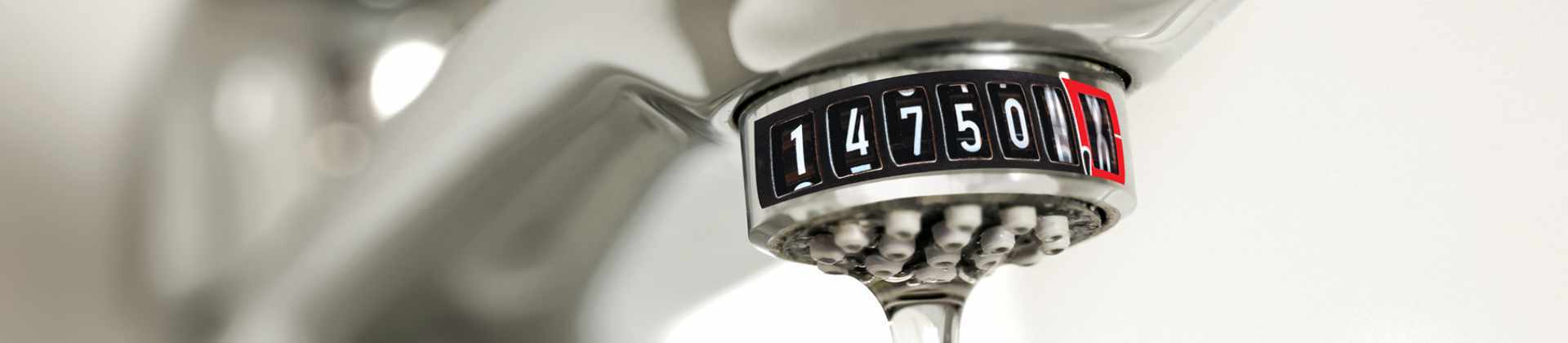
Energy-efficient SWRO
Learn how to improve SWRO’s energy efficiency in both new and existing plants.
Decarbonization requires more than reducing direct energy consumption
To minimize energy consumption and greenhouse gas (GHG) emissions in water treatment, it’s crucial to adopt a comprehensive perspective that extends beyond direct operational energy use. Decision-makers must also consider the full lifecycle of components, including the energy and emissions involved in their production and end-of-life disposal.
By evaluating the environmental impact of processes and components across the value chain, decision makers can gain insights into direct emissions from owned or controlled sources, indirect emissions from the generation of purchased electricity, and all other indirect emissions, including those associated with the manufacturing and disposal of equipment that has reached the end of its lifecycle. Collaboration with vendors who prioritize reuse, repair, and refurbishment extends equipment lifecycles throughout the value chain, contributing further to decarbonization efforts.
Danfoss is committed to decarbonization, not only by advancing energy-efficient solutions for our customers across multiple industries, but also by decarbonizing our own global operations thorough our “Reduce, Reuse, Re-source” approach. Danfoss pledges to cut 46.2% of total scope 1 and 2 GHG emissions by 2030, using 2019 as the baseline year. Additionally, Danfoss aims to decrease absolute scope 3 GHG emissions by 15% within the same period. Learn more about Danfoss’ decarbonization efforts here.
FAQ
Read more about solutions for desalination
-
if (isSmallPicture) {
; } else if (isBigColumns) { } else { }High-pressure pumps for SWRO applicationsThe range of high-pressure APP pumps is optimized for both landbased, off-shore and marine sea water reverse osmosis applications. Available with or without motor.
-
if (isSmallPicture) {
; } else if (isBigColumns) { } else { }Energy recovery device for medium to large SWRO applicationsThe first active ERD for medium and large plants integrates highly effective isobaric pressure exchangers with a low-voltage motor to eliminate the risk of rotor overspin, reduce mixing and biofouling, and facilitate smarter automation. Covering train sizes from 1,500 m3/day and above.
-
if (isSmallPicture) {
; } else if (isBigColumns) { } else { }iSave® energy recovery devices for high-pressure membrane applicationsWith a 3-in-1 design that integrates highly effective isobaric pressure exchangers with positive displacement booster pumps and electrical motors, iSave® ERDs deliver big energy savings in small spaces. Covering train sizes from 200-3,000 m3/day