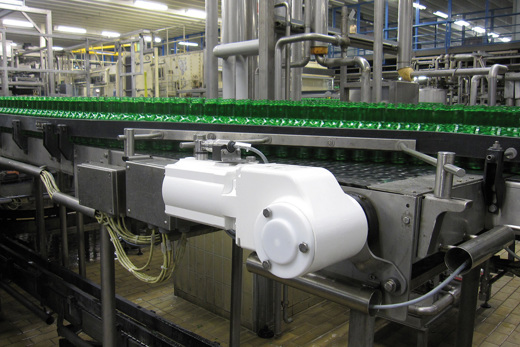
Maximize conveyor uptime
Ensure maximized uptime and the lowest cost of ownership for conveyors in dry, wet, or aseptic areas. Danfoss solutions ensure high energy efficiency whilst providing optimized motor control, improved quality and product consistency, minimized waste and optimized filling and packaging areas.
For highly sensitive product lines, such as conveyors for still bottled water and alcohol-free beer or new materials for packaging and bottles, Danfoss is unique in offering IPA compliant solutions for use in hygiene-critical sub-systems.
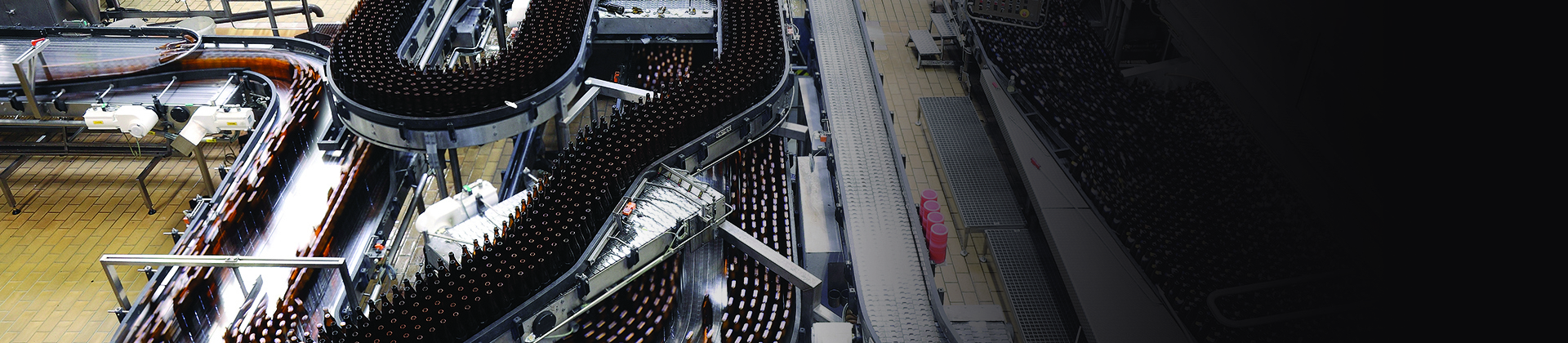
Discover how to maximize uptime with the VLT® FlexConcept® system
VLT® FlexConcept® combines modern motor technology with the most advanced inverter drives. This flexible unified drive system offers cost savings via high efficiency, robust reliability and variant reduction.
Reduce spare parts stock
The VLT® FlexConcept® system simplifies project planning, installation, commissioning and maintenance, especially for conveyor systems. System variants can be reduced by up to 70% so users benefit from maximum flexibility with a minimum number of modules. The system comprises only 3 gear motor variants to optimize your spare parts stock. Motors and drives in the VLT® FlexConcept® system offer a unified operating concept and standardized functionality regardless of whether the system is implemented with a centralized or decentralized structure.
FAQ
Products
-
if (isSmallPicture) {
; } else if (isBigColumns) { } else { }VLT® Midi Drive FC 280FC280 provides precise and efficient motor control for machine builders in the food and beverage, material handling and processing industries.
-
if (isSmallPicture) {
; } else if (isBigColumns) { } else { }VLT® AutomationDrive FC 301 / FC 302The VLT® AutomationDrive FC 301 / FC 302 is designed for variable speed control of all asynchronous motors and permanent magnet motors. It comes in a standard version (FC 301) and an advanced high dynamic version (FC 302) with additional functionalities.
-
if (isSmallPicture) {
; } else if (isBigColumns) { } else { }iC7-AutomationWhatever the environment, the iC7-Automation delivers the reliability and performance you need. With connectivity, security and intelligence, this drive lets you take advantage of the latest in Industrial IoT.
-
if (isSmallPicture) {
; } else if (isBigColumns) { } else { }VLT® Decentral Drive FCD 302Thanks to its rugged design, the FCD302 drive can be mounted close to motors in demanding applications.
-
if (isSmallPicture) {
; } else if (isBigColumns) { } else { }iC2-MicroThis next-generation micro drive gives you great cost effectiveness, durable reliability, and user-friendly commissioning and operation, all in a compact package.
Case stories
-
if (isSmallPicture) {
; } else if (isBigColumns) { } else { }iC7-Automation drives König’s automatic crate sorter at DGLKönig and Danfoss smoothly integrated iC7-Automation into DGL sorting machines for returned bottle crates. The highly efficient system sorts 3,600 crates hourly.
-
if (isSmallPicture) {
; } else if (isBigColumns) { } else { }Future-proof energy efficiency at AB InBev Hoegaarden® breweryChallenged by aging machinery and no time for downtime, AB InBev Hoegaarden® chose Danfoss iC7-Automation and VLT® OneGearDrive®—for high energy efficiency.
-
if (isSmallPicture) {
; } else if (isBigColumns) { } else { }Effortless control: Kohberg Bakery thrives with iC7-AutomationDENMARK: Kohberg Bakery upgraded its conveyor line for bread rolls to implement full control with built-in sensors and easy scalability for future adaptability.
-
if (isSmallPicture) {
; } else if (isBigColumns) { } else { }First mover controls beverage conveyor systems with iC7-AutomationBELGIUM: Legendre Conveyors has built up great trust in Danfoss over many years of conveyor design using VLT® drives. Now they progress to the new iC7 series.
-
if (isSmallPicture) {
; } else if (isBigColumns) { } else { }Maximizing uptime for high-volume bottle fillingNORTH MACEDONIA: To meet new standards for uptime, flexibility, and energy efficiency, Pivara Skopje’s RGB line needed modernization. The ideal VSDs? VLT® FlexConcept®.
-
if (isSmallPicture) {
; } else if (isBigColumns) { } else { }Brewing up real change at HEINEKENNETHERLANDS: HEINEKEN understands that to meet demand, its production line must always be up to the task – with all assets expected to deliver a consistently reliable and excellent performance. At Den Bosch brewery, the tough working environment posed several challenges. The solution was an upgrade using drives with integrated condition-based monitoring.