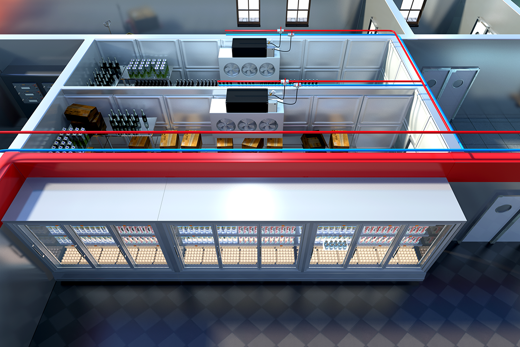
A cold room solution to meet every need
Found within the cold chain are cold storage facilities such as cold rooms. These facilities store or process both refrigerated and frozen products. They can be at the actual process facility or part of the distribution chain.
Compliance with hygiene and food safety regulations, but also energy regulations, is critical. Whether for a new installation or renovation, other parameters that must be considered when purchasing a cold room include ease of selection, refrigerant choice, installation options, reliability, maintenance, and operating costs.
Danfoss offers the widest portfolio of solutions for cold rooms to suit the diverse capacities, temperatures, and processes – for plug-in or remote installations, in small and larger sizes.
We offer contractor-friendly products & cold room solutions built with market leading expertise that are available everywhere and enable you to comply easily with regulations and save on installation and maintenance of walk-in refrigerators. Make the right choice for optimum protection of perishables, efficient operation and long lifespan.
Danfoss is a trustworthy partner for the cold room storage industry, with an extensive range of refrigeration monitoring solutions, experience and know-how. Our solutions for reliable walk-in cold rooms are specially developed to cover the extensive range of commercial refrigeration applications within; food service (restaurants, catering), specialty retail (butchers, bakeries etc.), process cooling (lab, medical, fruit ripening etc.), convenience stores, discount stores, and pharmacies.
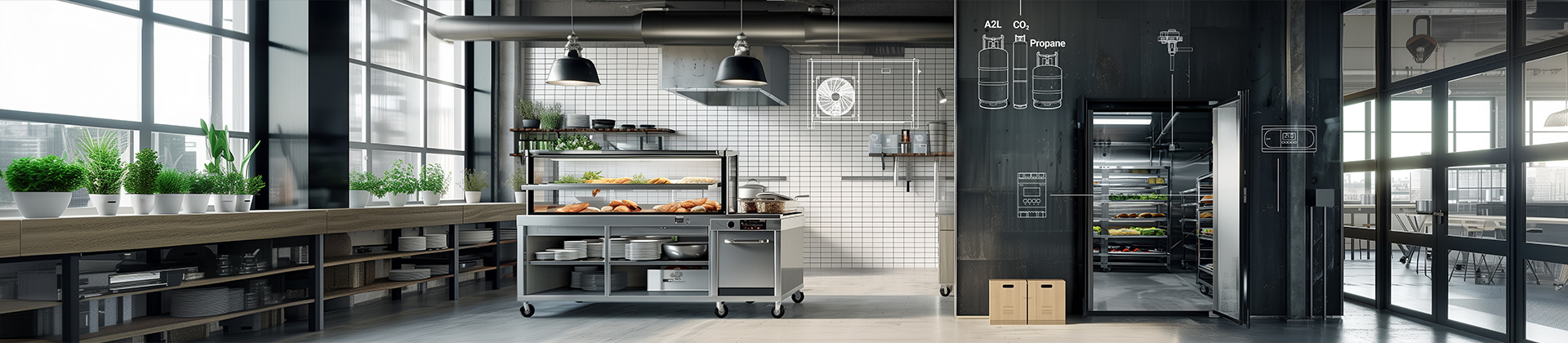
Low GWP solutions
Our extensive low GWP portfolio for cold rooms is compatible with a broad spectrum of refrigerants — from A2L to CO2 and propane.
Find the cooling solution that matches your needs.
Features and benefits
Widest portfolio for all types of cold room and walk-in refrigeration applications
Reliable and highly energy efficient solutions
Long service life, low operation and maintenance costs
Compliance with refrigerant and energy regulations
Products suitable for use with lower GWP and natural refrigerants
Global and local application expertise
Simple product selection with Coolselector®2 software
Highlighted products
-
if (isSmallPicture) {
; } else if (isBigColumns) { } else { }Optyma™ iCO₂ 4.6kW MTOptyma™ iCO₂ 4.6 kW (MBP) condensing unit is a robust and low-noise solution for natural refrigerant R744 compatibility.
-
if (isSmallPicture) {
; } else if (isBigColumns) { } else { }Optyma™ iCO₂ 20MT/10LTOptyma™ iCO2 20MT/10LT condensing unit is a robust and low-noise solution for natural refrigerant R744 compatibility.
-
if (isSmallPicture) {
; } else if (isBigColumns) { } else { }Optyma™ condensing unitsOptymaTM ranges of condensing units match your commercial refrigeration application needs, with their unique versatility and simplicity to install. Multi-refrigerants, using low-GWP and natural refrigerants, highly efficient, they are a perfect fit for small to mid-size cold rooms, display cabinets, milk cooling tanks, fermentation rooms and much more.
-
if (isSmallPicture) {
; } else if (isBigColumns) { } else { }Compressors for refrigerationDanfoss focuses on providing energy efficient, sustainable and smart refrigeration compressors for a varied range of commercial applications such as cold rooms, display windows, ice making machines, glass door merchandizers, process cooling etc. Their qualification with lower GWP refrigerants make them compliant with refrigerant regulations such as F-Gas in Europe.
-
if (isSmallPicture) {
; } else if (isBigColumns) { } else { }Thermostatic expansion valvesThermostatic expansion valves (TXV) are available as parts programs, i.e. with separate valve body and orifice assemblies, or as complete valves (fixed orifice). The category also contains thermostatic injection valves.
-
if (isSmallPicture) {
; } else if (isBigColumns) { } else { }Solenoid valves for HVAC-RSolenoid valves for A/C and commercial refrigeration for fluorinated refrigerants and CO2 (R744). Solenoid valves and coils are normally supplied separately and then assembled without tools, providing optimum flexibility and product availability.
-
if (isSmallPicture) {
; } else if (isBigColumns) { } else { }Optyma™ ControlOptyma™ Control is a cold room controller specifically designed for safety, protection, control, and ease of installation.
-
if (isSmallPicture) {
; } else if (isBigColumns) { } else { }DMLE / DCLE hermetic high pressure filter driers, HFC optimizedDMLE and DCLE hermetic filter driers are optimized for HFC refrigerants and mineral or benzene oils. Compatible with A2L refrigerants R32, R444B, R452B, R454B, R1234yf, and with A1, A2, and A3 refrigerants at a maximum working pressure (MWP) of 50 bar (725 psi).
Documents
Type | Name | Language | Valid for | Updated | Download | File type |
---|---|---|---|---|---|---|
Brochure | Cold Room brochure for installers_FIN | Finnish | Finland | 16 Jan, 2019 | 5.5 MB | |
Brochure | Cold Room brochure for Installers_SWE | Swedish | Sweden | 16 Jan, 2019 | 892.9 KB | |
Brochure | Cold Room brochure for Installers/Contractors Europe | Danish | Denmark | 17 Jan, 2019 | 850.2 KB | |
Brochure | Cold Room brochure for Installers/Contractors Europe | English | Multiple | 08 Nov, 2018 | 871.8 KB | |
Brochure | Cold Room brochure for OEMs Europe | English | Multiple | 29 Jun, 2017 | 8.2 MB | |
Brochure | Cold Room brochure for OEMs North America | English | Multiple | 08 Sep, 2017 | 4.0 MB | |
Brochure | Danfoss Solutions for Walk-in Coolers and Freezers | English | Multiple | 10 Jan, 2024 | 3.7 MB | |
Article | Food safety Focus on system performance, reliability and connectivity | English | Multiple | 26 Mar, 2025 | 936.9 KB |
Learning
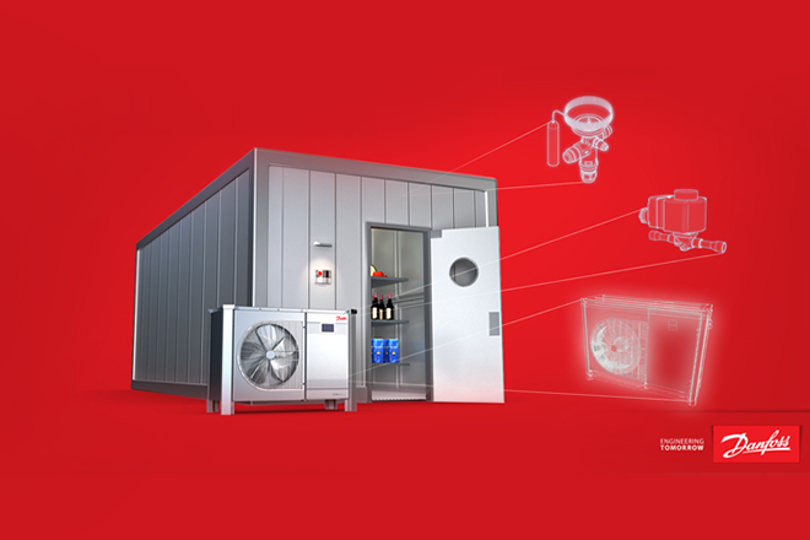
Cold room training program
Learn how to achieve better food preservation through Cold Room solutions with our online training program.
Case stories
-
if (isSmallPicture) {
; } else if (isBigColumns) { } else { }Refrigeration systems preserve apple quality using VSDs with integrated condition monitoring and DrivePro Remote Monitoring serviceITALY: At Rivoira Group, VLT® drives with built-in condition-based monitoring help preserve fruit perfectly by ensuring utterly reliable refrigeration.
-
if (isSmallPicture) {
; } else if (isBigColumns) { } else { }A new cold room in time for Christmas with fast-installation Optyma™ Slim PackA high-performing cold room delivered in a matter of days, so Hurren’s Butchers could maximize seasonal business.
-
if (isSmallPicture) {
; } else if (isBigColumns) { } else { }Danish supermarkets turned into heat suppliersA Danish supermarket fulfills 95 percent of its heating demand from its own cooling display cases. The chain has installed Danfoss heat recovery units and managed to halve its CO2 footprint in five years. Imagine if this was done in all supermarkets in the world.
-
if (isSmallPicture) {
; } else if (isBigColumns) { } else { }Hot gas defrost - the next step in commercial kitchen refrigerationAs authorities and customers focus on energy efficiency standards and ratings to understand not just what a commercial refrigeration unit costs to buy, but what it costs to operate, the refrigeration design engineer needs to look again at the fundamentals and consider new approaches.
-
if (isSmallPicture) {
; } else if (isBigColumns) { } else { }Raising the stakes in energy efficiencyEveryone was a winner in a three-horse race to supply coldrooms and cellar coolers to the new Princess Royal Grandstand at Cheltenham Racecourse.
-
if (isSmallPicture) {
; } else if (isBigColumns) { } else { }Diaper Poultry invests in new dispatch area cold room powered by Optyma™ PlusDiaper Poultry are really pleased with the result. Compared to the old refrigeration solution, the new Optyma™ solution is only about a quarter of the size, it works much more quietly and at the same time it is just as efficient as the old system.
FAQ for cold rooms
General questions on low GWP refrigerants
Alternatives to R404A/R507 and R409A
Retrofit market for cold rooms
Impact on cooling performance
Technical characteristics of refrigerants
Flammable vs. non-flammable refrigerants
CO2 and propane refrigerants
Refrigerant transitions: What to be aware of?
General FAQ on cold rooms
Contact us
For further information, please contact us.