Hydrogen – a clean and sustainable energy source
Green hydrogen is a promising and rapidly developing field of renewable energy. As the world seeks to transition away from fossil energy sources to reduce carbon emissions and mitigate climate change, hydrogen produced through the electrolysis of water using renewable energy sources has emerged as a key contender.
Danfoss supports the green transitions with high-pressure pumps and energy recovery devices. Overall, high-pressure pumps for ultra-pure water are a critical component of green hydrogen generation, enabling the efficient and reliable production of this promising renewable energy source.
The water needed for hydrogen production must be ultra-pure. To protect the scarce drinking water resources seawater reverse osmosis could be a better way to ensure water supply.
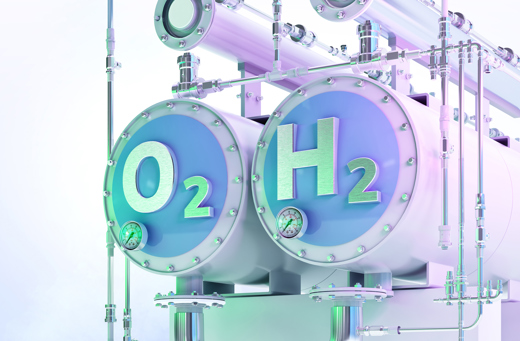
Electrolysis process explained
A hydrogen electrolyzer is a device that uses electricity to split water (H20) into its constituent elements, hydrogen (H2) and oxygen (O2). This process is called electrolysis and is achieved by passing an electric current through water, which causes the water molecules to break apart into hydrogen and oxygen ions.
The electrolysis process requires ultra-pure water to ensure the efficiency and longevity of the electrolyzers. High-pressure pumps are often used to feed ultra-pure water into the electrolysis cell. These pumps are designed to generate the high pressures needed and maintain a steady flow of water.
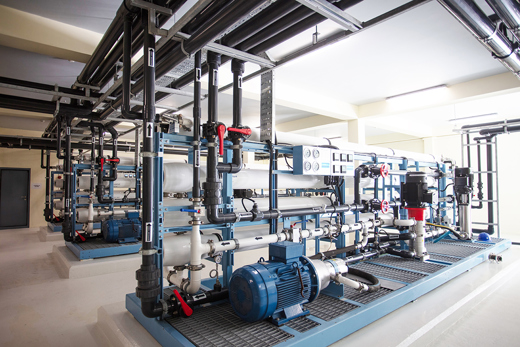
Water treatment
According to the UN, water scarcity is one of the major challenges facing the world today and tomorrow. The world has lots of saltwater, but not nearly as much fresh water. Turning seawater into DI water, which can be used for hydrogen production is a promising and sustainable approach that can help to protect the scarce freshwater resources.
Using high-pressure pumps and energy recovery devices from Danfoss in the seawater reverse osmosis process is not only a sustainable approach but also the most energy efficient way to produce the DI water needed.
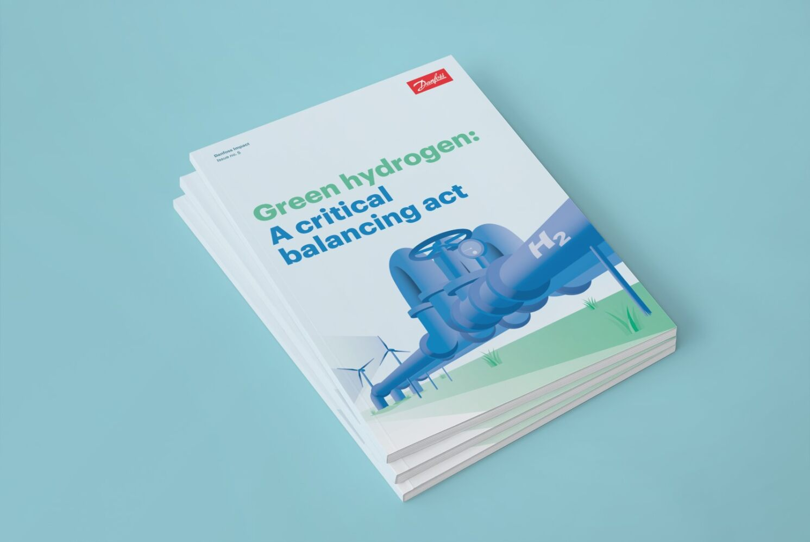
Green hydrogen - a critical balancing act
Green hydrogen will play a critical role in the transition away from fossil fuels. Download our informative whitepaper to learn how to prioritize electrification and energy efficiency measures, produce hydrogen efficiently, and utilize it wisely to drive sustainable transformation in hard-to-decarbonize sectors. Take the first step towards a greener future by downloading the whitepaper now.
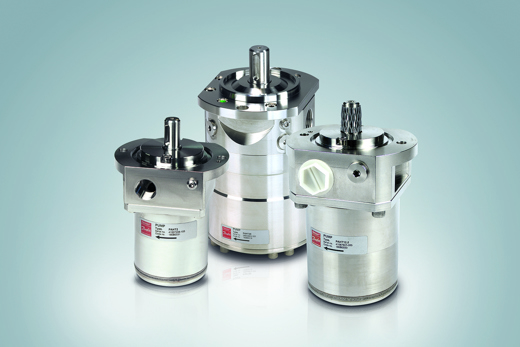
Compact, oil-free pumps with high efficiency
The Danfoss PAHT high-pressure pump is an ideal choice for the electrolyzer application due to its many benefits.
High-pressure PAHT pumps for ultra-pure water are made of stainless steel and have high compatibility with the water and the electrolysis process making them highly reliable.
The pumps offer high efficiency rates up to 95% volumetric efficiency. There is no risk of oil contamination as the pumps are oil-free and lubricated by the media itself. The pumps have very long service intervals, only a few moving parts and are easy to maintain.
Videos: Pump animation and hydrogen electrolysis plant
Related products
-
if (isSmallPicture) {
; } else if (isBigColumns) { } else { }High-pressure pumps for ultra pure water applicationsHigh-pressure pumps for ultra-pure water applications i.e. with de-ionized, de-mineralized or distilled water. Appropriate for critical applications such as high-pressure cleaning and humidification. Available with or without motor.
-
if (isSmallPicture) {
; } else if (isBigColumns) { } else { }High-pressure pumps for SWRO applicationsThe range of high-pressure APP pumps is optimized for both landbased, off-shore and marine sea water reverse osmosis applications. Available with or without motor.
-
if (isSmallPicture) {
; } else if (isBigColumns) { } else { }iSave® energy recovery devices for high-pressure membrane applicationsWith a 3-in-1 design that integrates highly effective isobaric pressure exchangers with positive displacement booster pumps and electrical motors, iSave® ERDs deliver big energy savings in small spaces. Covering train sizes from 200-3,000 m3/day