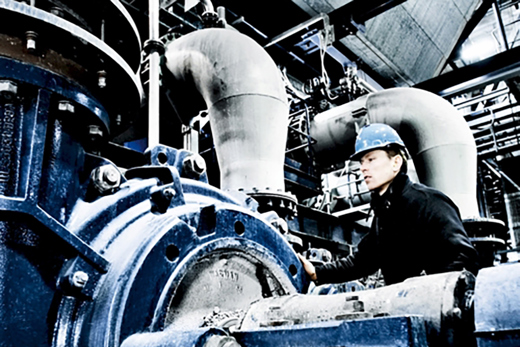
One of the main factors for obtaining long reliable service from any piece of equipment is maintenance. Any type of electrical or mechanical device is subject to wear and tear. This can be further aggravated by undesirable environmental conditions. Such things as heat, moisture, dust/dirt, poor electrical connections, and poor ground connections can cause premature failures. They can also cause the normal service life of the equipment to be shortened considerably.
A piece of equipment employing the use of a motor controlled by a Variable Frequency Drive (VFD) is no exception. Many manufacturers of motors and VFD’s as well as companies specializing in the service of these products offer service related products such as PM contracts to assist the user in maintaining the equipment.
Regardless of the type or brand of motor or VFD, there are some common areas that require attention during maintenance procedures. These can be categorized as electrical, mechanical, and environmental. Though these three areas can sometimes be quite interrelated, we will address them individually.
Mechanical
As any Mechanic will tell you, keeping all moving parts aligned and lubricated will yield the most reliability and longest service life out of any piece of equipment.
Improper alignment of belts or shafts will result in undo stress or vibration. Shaft and pulley alignment should be checked periodically. Also, the condition of belts should be checked at the same time. Excessive wear of belts can sometimes indicate alignment problems.
Of course, maintaining the proper lubrication of all bearings is necessary. Lack of lubrication, or in some cases over lubrication can result in excessive wear on the bearing. Another area of concern here is using the proper lubricant. Sometimes the decision as to which type of oil or grease to use depends on the purchase price of that substance. It is important to remember that the wrong type of grease can be just as damaging as no grease at all. One should always follow the equipment manufacturers’ specifications as to the type of lubricant and frequency of application.
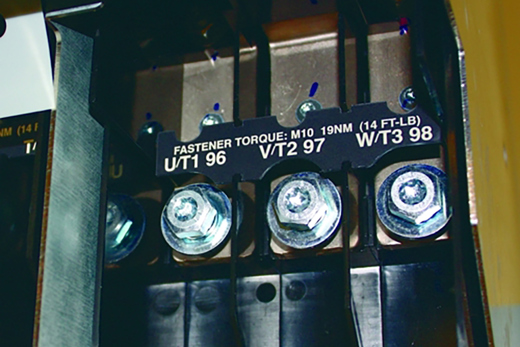
Electrical
Probably the most common function in the PM procedure for any piece of electrical equipment is to check that all electrical connections are tightened properly. Poor connections can cause a variety of problems ranging from instantaneous failure to excessive mechanical wear. All screw type electrical connections should be checked at least annually to ensure that they are tightened to the proper torque.
One mistake often made by maintenance personnel is to tighten the terminal screw as tight as possible. That is almost never correct. Every screw type electrical terminal has particular torque specification. Often these specified torque values will seem somewhat low for the size of the terminal screw. Many people will see a large terminal screw and instinctively want to tighten it with a great deal of torque. Remember, the size of the terminal screw has more to do with the amount of current in that circuit than the physical strength requirement. Over tightening these screws can cause deformation in the terminal or the wire resulting in a poor electrical connection.
If there is a considerable amount of dirt, oil, or other contaminants in the surrounding area, the exposed areas of the connection may also require periodic cleaning as well. This is especially true if the surfaces in the connection are oxidized or corroded.
Ground connections are of particular concern in any electrical installation. This is especially true when a motor is being controlled by a VFD. In addition to the amount of potential noise interference created anytime an AC motor is connected to an electrical power source, there is also the switching frequency from the VFD along with some common mode voltages associated with using a VFD.
There are two main functions of a ground connection. One is to establish a ground level potential on the enclosure of a device to protect against electrical shock hazards for any personnel that may come in contact with the equipment. This is normally referred to as a low frequency ground. The other function is to enable any structure or enclosure to act as a shield to prevent noise interference from entering or exiting the equipment. This is often referred to as a high frequency ground connection. With a high frequency ground, the integrity of the connection is much more critical. Ground connections should be checked and cleaned periodically to ensure that the high frequency capability of the connection is maintained. A good high frequency ground connection on the motor can reduce the damage caused by bearing currents induced by common mode voltages, and eddy currents from asymmetrical coil windings in the motor.
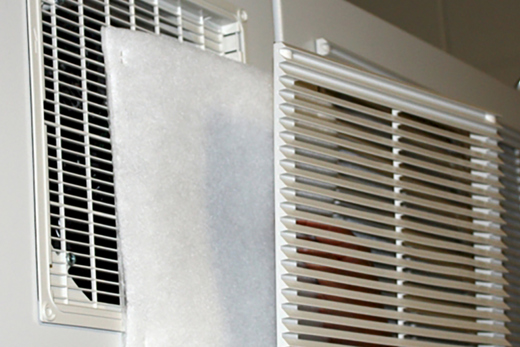
Environmental
There are several environmental factors that can affect the life and reliability of a motor/VFD system. One of the major factors is, of course, temperature. This can be caused by the weather of the location where the system is installed or by the heat that is being produced by the equipment itself. Heat can be considered the common enemy of any type of equipment whether it is electrical or mechanical. VFDs typically have efficiency ratings that range from 92 – 98%. This means that for every kilowatt of electrical power that is being used, 20 – 80 watts are being dissipated in the form of heat.
By design, most manufacturers of motors and VFDs have included a method to remove excess heat. These normally consist of a cooling medium (either air or liquid) passing along a heat exchanger or heatsink. The operative word is passing. This means that in order for the cooling medium to do its job effectively it must be moving along or through the heat exchanger.
A major maintenance function is to ensure that all cooling air or fluid passageways are free from clogs or obstructions that can reduce flow. Heatsinks and heat exchangers must be cleaned periodically to remove any dirt or material that would obstruct flow.
Quite often when the VFD is mounted in a protective enclosure or cabinet, an air filter is used to keep contaminants out. These filters must be cleaned or replaced periodically. The frequency depends upon the amount of dirt or contaminants present. Of course, all fans and circulating pumps must be checked to ensure that they are in proper working order.
One major concern is cleanliness. While this has been alluded to a number of times in this article, it requires reiterating. Dust, dirt, and other contaminants can cause failures in every aspect of a motor/VFD system. Therefore a major function of anyone responsible for maintenance is cleaning of the equipment and surrounding area.
If the VFD or any other electrical equipment is mounted in a cabinet, the cabinet door gaskets must also be checked to ensure that the integrity of the enclosure is maintained. It must also be emphasized that it is important to close and latch cabinet doors when work in that cabinet is complete. It is not uncommon to find watertight enclosures with the door held closed by only one insufficiently tightened door clamp. The rating of an enclosure is only valid when the door is closed and latched properly.
The lack of regular maintenance can result in premature failures of either VFDs or motors. The extra expense of a regularly scheduled preventative maintenance program is considerably low compared to the cost of repairs or replacement of motors or VFD’s. The primary reason for the use of VFD’s is to increase efficiency in processes and power consumption and to save money. Proper maintenance will ensure you are able to continue on that path during the life of the system.
Article by Gregory Finch