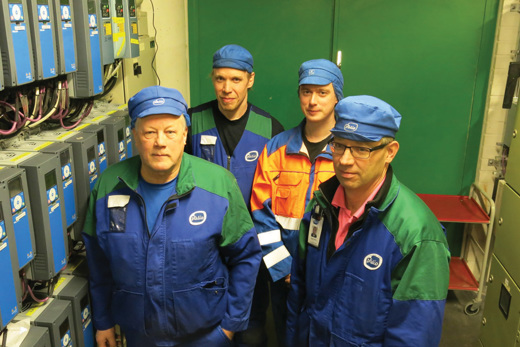
Precise process control is essential in the production of food and beverages. VACON® AC drives enable accurate control and improve work safety and reliability. Valio is the market leader in all key dairy product groups in Finland, and has numerous major consumer brands in its portfolio.
100 VACON® 100 drives in quark production
The Valio plant in Seinäjoki, capital of the province of Southern Ostrobothnia in Finland, produces all Valio quarks. The plant recently doubled its production capacity to meet the increased demand for quark – a product that is high in protein. Commissioned in March 2014, the new production line requires 100 motors to run, for example, the plant’s pumps and mixers. These motors are controlled by 100 VACON® 100 AC drives in the power range of 1.1 kW – 45 kW with a total power of approximately 400 kW.
The VACON® 100 AC drives use Profibus fieldbus for communication with Metso’s automation system.
VACON® 100 is a versatile AC drive that can be used in hundreds of different applications. “We chose the VACON® 100 drive to control our quark production line because of the new requirements for Safe Torque Off (STO) functions and to improve work safety,” explain Hannu Teräväinen and Teemu Takala, Technical Specialists at Valio’s Seinäjoki plant. As the result of the strict standards and risk analysis, an STO function is a must on the quark production line to prevent the motor from generating torque on the motor shaft, which could cause unintentional start-ups. The STO function is provided in the OPTBJ board, which is easy to fit in the VACON® 100 range of drives. The corresponding board option in the previous VACON® NX generation of drives has been available since 2006.
VACON® AC drives also integrated into OEM equipment
In addition to the AC drives delivered directly by Vacon, VACON® AC drives have also been delivered to Valio’s Seinäjoki plant via several Original Equipment Manufacturer (OEM) partners. “Our primary requirement for our OEM partners is the choice of VACON® AC drives for integration in their equipment. Usually we succeed in this,” states Valio Technical Specialist, Pauli Parvi. “It is in our own best interest to choose AC drives from a single manufacturer whose products are reliable and already familiar to us. Familiar products simplify installation, monitoring, preventive maintenance and spare part availability, and facilitate the installation of replacement units if necessary. It is also a great benefit that local support is quickly available, since Vacon’s headquarters and service center lie only 80 km away in Vaasa,” adds Mr Parvi.
Smooth start-up and process control essential
The most common AC drive application is pump control. At the Seinäjoki plant, 80% of the pumps are controlled by AC drives. The AC drive accelerates the pump motor quickly but smoothly to its running speed. A smooth start-up reduces the stress on the electrical network and on the pump’s mechanical parts, and reduces pressure spikes in the pipeline. Continuous control of the running speed also allows the product’s manufacturing process to be optimized. This results in improved reliability and process control. “For us, process control is absolutely the most important reason for using AC drives,” explains Marko Vähäkoski, Project Manager. Reliability is vital as costs from interruptions in production can quickly accumulate. As the drives are connected to the Profibus fieldbus, it is possible to collect measurement data on the energy used by the pumps.
Largest industrial heat pump solution in Europe
Hannu Teräväinen, who has had a 40-year career at the same site, thinks that Valio is always in the forefront of technical development. A good example is a globally unique heat pump solution that was taken into use at the Seinäjoki plant in August 2012. The solution is based on recovering and recycling the heat and cold used in some of the plant’s processes. For example, heat from the milk powder drying process and cold from the product refrigeration process. Previously, condensation heat simply evaporated into the air and wastewater from the cooling process was disposed of as part of the waste energy flow. The recovered heat is now distributed through pipelines to various destinations at the plant. The heat pumps are controlled by five 250 kW VACON® NXC AC drives.
Excellent customer relationship since 1997
“The first VACON® AC drives were taken into use at the Seinäjoki plant in 1997,” recalls Mr Teräväinen. VACON® AC drives control pumps, mixers, separators, fans and conveyors as well as packing and palletizing machines. “In total, we have about 1,000 VACON® AC drives here at the site. We still have several drives from the first product generation, the Vacon® CX range,” he continues. “The VACON® AC drives are great and our user experiences are positive,” his colleagues Pauli Parvi, Marko Vähäkoski and Teemu Takala add. They know from experience, for their total work experience at the same site adds up to almost 90 years. They also have plans for new projects at the plant where VACON® AC drives can be used.
Please note that Vacon joined the Danfoss Group in December 2014.
Get more information
Read case story and download
Read more about solutions for Food and beverage
-
if (isSmallPicture) {
; } else if (isBigColumns) { } else { }VACON® 100 INDUSTRIALDrive modules and enclosed drives that are easily integrated into all major control systems.