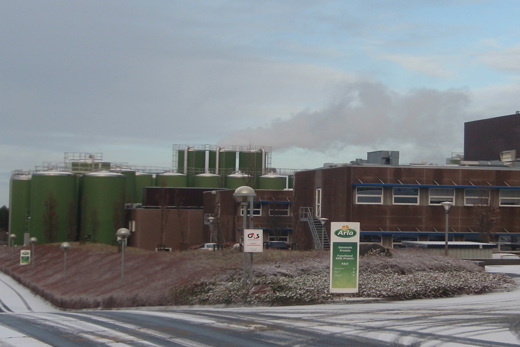
Energy consuming production of whey powder at Arla Food Ingredients Group P/S in Videbæk, Denmark has been optimized by the use of Danfoss VLT® drives. It saves energy, time for project design and makes hundreds of motors run more efficiently and last longer.
In order to separate different products at the whey powder-manufacturing site at Arla Food Ingredients Group in Videbæk, the processes demand hundreds of pumps, fans, evaporators, filtration units and spray dryers. This is a highly energy consuming process. To save energy and money, Arla has chosen a concept for motor installations that includes VLT® drives from Danfoss.
Instead of designing and building new panels for motor starters, the VLT® drives (VLT® AutomationDrive FC 302 IP20) are installed in the control rooms. ”The drives are connected to every motor - new and existing - and the motors benefit from all the features of the drives. The drive systems are connected into a computerized control system, so Arla employees can control everything from the computer screen. That was not possible with the old system. We always install a Profibus card within the VLT® AutomationDrive for control purposes, which gives us the ability to access process data and information from the drives. This is a huge advantage”, says maintenance manager at Arla Food Ingredients, Knud Rahbek.
With a multi-purpose drive, like VLT® AutomationDrive, which includes harmonic filters and EMC filters for 150-metre motor cables, all the applications can be handled with one type of VLT® drive, and all the motors can be accessed from the control room.
According to Knud Rahbek, the factory also uses this concept in renovation projects. ”We simply throw out the old panels and build-up the new installation with VLT® drives in connection with distribution panels.”
Savings Spent on New Drives
Before the installation of VLT® drives, the factory had many motors with DOL starters. That meant less flexibility for speed control, more mechanical maintenance of the motors and less motor and plant control and information without Profibus communication. It also took up a great deal of panel space. ”The panels are now only designed for distribution, including fuses or circuit breakers. This needs only half the size of a normal motor starter panel and saves money and space in the panel rooms”, Knud Rahbek explains. The cash saved is spent on buying new energy efficient VLT® drives. Therefore the new drive concept doesn’t result in extra investment costs but actually saves money.
Due to this concept Arla also saves money on engineering costs. An engineer costs 750 DKK per hour, whereas an electrician, whose job it is to mount the drives, only costs 350 DKK per hour. According to Knud Rahbek, the Arla electricians have been educated in understanding the benefits of the VLT® drives and they fully understand how to install and program them.
Energy Savings in Focus
”We are extremely conscious of the need to save energy since we are an energy intensive company. This is due to the fact that the production site contains more than 600 motors and ventilators. The Arla Food Ingredients factory in Videbæk uses around 50 million kWhrs of electricity per year. Therefore just a 10% saving in energy costs is of huge importance, saves a great deal of money and makes a significant reduction in Arla’s carbon footprint. We have added a VLT® drive to each and every one of the motors and ventilators and in this way we have achieved estimated saving between 5-15% of energy. We plan to install 100 more drives in new projects over the next three years”, Knud Rahbek explains.
The drives control the motor-driven pumps so that they only run as and when needed and then only at the required speed. This saves a great deal of energy, since without inverter control, the motors would run continuously. Speed control instead of valve control as before reduces the payback time on the investment on the drives. On filtration units, for instance, there are additional huge energy saving benefits due to improved temperature control via speed and flow control. The factory has numerous filtration units, because its prime function is to make use of all the elements of the whey that is left over from cheese production.
DriveProTM Service Agreement
”It’s important for us that we are working closely with Danfoss. If we have a breakdown of a VLT® drive, we will be up and running again after a maximum 6 hours, due to the Danfoss service concept. Extra parts are always to hand and easy to procure. The close co-operation with Danfoss also means that our employees are very familiar with the VLT® drives and this improves the operational reliability,” Knud Rahbek says.
Arla Food Ingredients Group has made a DriveProTM service agreement with Danfoss covering the VLT® drives over a period of 3 years from their installation. The Danfoss Service partner, Styreg, checks the whole installed VLT® base and documents this with the free Danfoss VLT® Software Tool MCT10 so that if there have been warnings or alarms, a further breakdown can be avoided. In addition, all drive parameters are downloaded and the drives are physically checked. All-in-all, the service agreement offers improved up-time, and reduces the number of expensive breakdowns.
Facts
The Arla Food Ingredients Group factory in Videbæk, Denmark uses around 50 million kWhrs of electricity pr year. Therefore just a 10% saving in energy costs is of huge importance. 600 Danfoss VLT® AutomationDrive FC 302 are installed at sizes from 0,37 kW - 400 kW. Future projects include more than 100 drives more over the next 3 years.