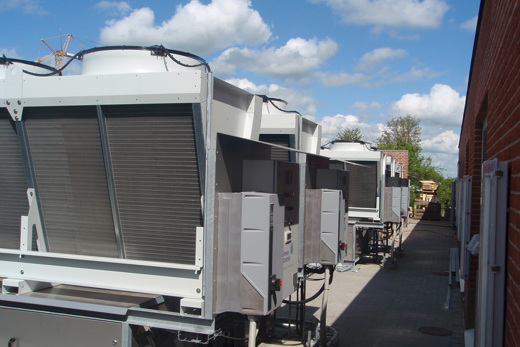
A new centralized cooling plant will annually save 800,000 kWh energy and secure optimal operation at Denmark’s second biggest hospital.
Stability and efficiency are key words at the new centralized cooling plant at Aarhus University Hospital, Skejby. This, the main hospital of Denmark’s second largest city Aarhus, has replaced a huge amount of old decentralized cooling units with one, new centralized plant with a cooling capacity of 2.5 MW. It improves the level of stability of the necessary cooling of surgery rooms, scanners, server rooms and IT-equipment.
At the same time it facilitates the possibility of the operations department to control and run the complete cooling plant more effectively - with much lower energy consumption than before. It is estimated that the hospital will save around 3.5 mio kWh of energy annually, due to the installation of a highly energy efficient heating and cooling system. The new system combines the cooling system with the heating system, an obvious solution, which is not used very much worldwide.
High efficiency heat pumps and chillers
The new cooling plant consists of two large air/liquid heat pumps, 9 air-cooled chillers and a number of compressors. The units are called SAB LightTM from Johnson Controls. Danfoss VLT® drives control the speed of the units. The new technology used combined with the frequency converters contribute to the total energy savings.
During the months of June, July and August the heat pumps are able to deliver all the heat required at the hospital. Therefore no extra heat has to be delivered from the public district-heating network. Surplus heat from the cooling production during the summer is reused for heating purposes. During the winter the heat pumps deliver a smaller portion of the heat consumption, while the main heat supply is taken care of by the district-heating supplier, AffaldVarme Aarhus.
The two 180 kW heat pumps (actually two times two separate heat pump circuits, which are built together into one unit) are designed for temperatures of 35/80 C. They achieve important energy savings, due to the fact that they re-use the heat instead of exhausting it into the air. ”The heat pumps´ COP (coefficient of performance) is 3.6 or more, depending on outside temperature and cooling demand. This means that their heating power is 3.6 times the electricity consumed. On the old system, the COP was only between 2 and 3, so the heat pumps are an energy saving solution”, says Svend Madsen from Johnson Controls, who have installed the cooling plant and hold the service agreement.
The chillers´ COP is 5 or more depending on cooling demand and outside temperature. The 90 kW VLT® drives from Danfoss, combined with the control system, regulate that only the required cooling is actually being produced. A small 5.5 kW VLT® drive runs a pump on the cooling system and is regulated according to the speed of the big VLT® drive depending on cooling demand.
Easier control and service
A new PLC monitoring system measures and analyses the efficiency of each machine in order to secure the right combination of chillers and heat pumps, so that the most energy efficient production is chosen at any time. For instance, the supervision can change the production from three chillers at maximum load to four chillers running at 80 % load, based on a snapshot on what achieves the biggest energy savings. This way the CO2 emissions are reduced as much as possible. Svend Madsen explains that the cooling plant also uses free cooling in the wintertime in order to utilize the cold days of the year, so no cooling is produced during this period. “It’s also very important in the attempt to save energy that surplus heat from the chillers is re-used for heating purpose instead of being sent into the air,” he says.
The highly efficient centralized cooling plant is easier to monitor, control and service than the many old cooling units. There will be less maintenance work to do for the operating staff. “The entire system is computerized and PLC controlled, so the physical monitoring will be brought to a minimum. In the design phase and during the installation process we have cooperated closely with the operations department. They are the ones who will work with the plant on daily basis, so their input is important for the project”, project manager Lars Torp Larsen from consulting engineer Alectia says.
If, for instance, one cooling machine has a lower performance than the others, the staff will be warned by an alarm and immediate action will be taken to optimize it. A CTS system monitors a number of parameters, which takes care of the efficiency of the IT monitoring system. Poul Hvid Nielsen, Chief of Technical Department at Aarhus University Hospital, Skejby, is satisfied: “In this way the hospital has got double security for optimal operation. Being a hospital, security of supply is fundamental to us”.
Hospital enlargement on the way
Poul explains that three new buildings have been built and added to the hospital recently, and the new centralized cooling plant is prepared for a further growing demand for cooling.”The cooling system is designed so that, for instance, a cooling machine or a heat pump can cut out on a warm summer day without creating any kind of problems to the cooling supply”, he says.
The hospital is one of Denmark’s most important hospitals and will be enlarged to more than double the size over the coming years. “The project group has worked on achieving synergy in the process of renovating the existing hospital and at the same time enlarging it to almost twice the size. I think we are succeeding in this”, Poul says. However, the newly established cooling plant will not be able to supply the many new hospital buildings to be built in the coming years. Instead, a second cooling plant will be built and the two plants will supplement each other to fulfill future cooling needs.
Environmentally friendly solution
"Since several of the old cooling units were worn out and needed to be replaced, something had to be done now. There was no possibility of waiting until the new parts of the hospital are built. The new cooling plant is not only more efficient but also more environmentally friendly than the old system. Many old units used the greenhouse gas Freon 22 as refrigerant - this is forbidden in all new cooling systems in Denmark, and at Skejby Hospital it has been replaced by natural refrigerants. The choice fell on chillers using R290 (propane, GWP*=3.3) and heat pumps using R600a (iso-buthane, GWP=4). Other options like CO2 had also been evaluated but were found to be less efficient in the applications and the temperatures required. This way about 750 tons of CO2 emissions are saved annually”, Lars Torp Larsen says. Moreover, the new cooling system saves around 800,000 kWh of energy per year and surplus heat from the cooling plant is reused.
All the environmentally friendly results are additional benefits of the installation of a much better cooling system, where state-of-the-art energy technology is being used to the benefit of the hospital patients and its staff.
Get more information
-
if (isSmallPicture) {
; } else if (isBigColumns) { } else { }VLT® HVAC Drive FC 102This tough and savvy FC102 drive enhances pump and fan applications in building management systems, and runs outdoors in most climates.