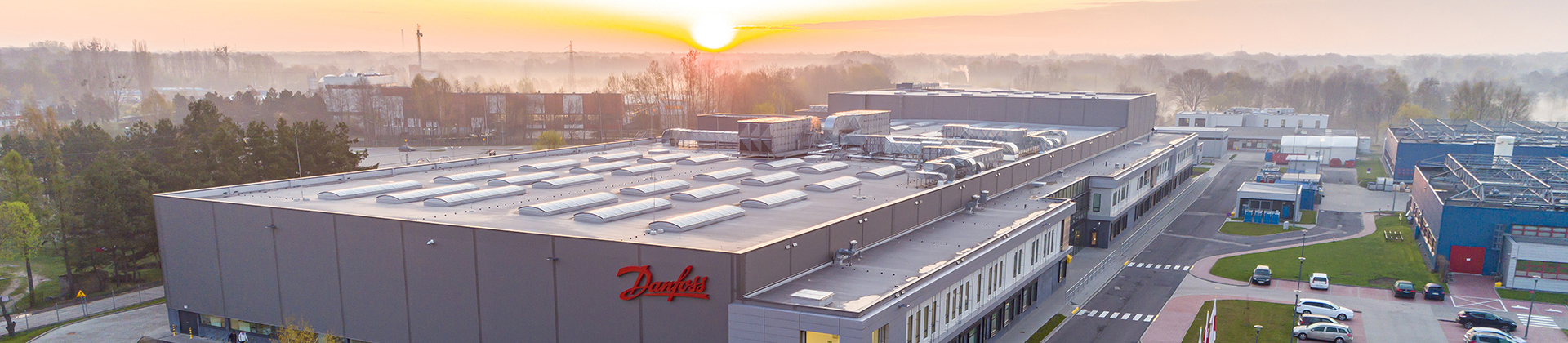

POLAND: Innovative approaches to industrial production are essential given the growing challenges of climate change and the need to reduce greenhouse gas emissions. Therefore, manufacturers increasingly strive to use clean and sustainable energy sources to minimize their environmental impact.
Danfoss’ factory in Grodzisk Mazowiecki is among the company’s most advanced production facilities and is the first to be fully powered by renewable energy sources. An important aspect during the construction of the plant was to optimize efficiency, using technologies for data collection and processing. In the factory, VLT® HVAC Drive FC 102 supports efficient ventilation, featuring condition-based monitoring and connected to a DrivePro® Remote Monitoring service. These drives control the ventilation and air-conditioning system and also collect information about the parameters, or emergency states of the system.
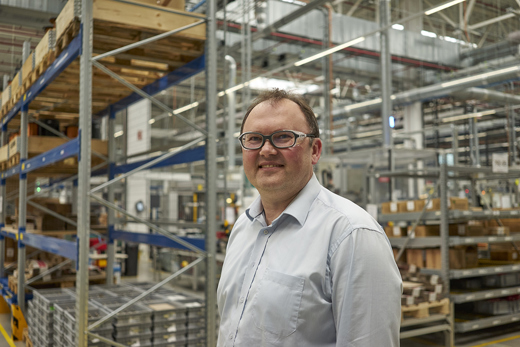
The challenge: More comfort for less CO2 emission
During the design process of the facility, it was important to ensure the safety of workers and production. The systems had to meet the requirements of maintaining set parameters in buildings to ensure a comfortable working environment.
Eliminating downtime risk was also a priority. According to estimates, a production stoppage costs the factory 22,000 EUR per incident. This figure is based such factors as the cost of delays in meeting order deadlines, the purchase of spare parts, and the cost of employees leaving their workstations.
Danfoss also aims to achieve carbon neutrality by 2030. To meet this goal and customer demands for sustainable, eco-friendly products, Danfoss focused on using renewable energy sources and maximizing energy efficiency in the new factory. By reducing energy usage and optimizing its carbon footprint in this way, Danfoss aimed to lower costs while upholding its commitment to ethical, environmentally-conscious operations.
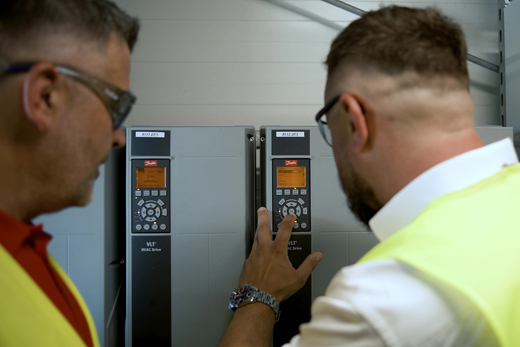
The solution: Intelligent drives with remote monitoring
The ventilation and air conditioning system at the factory is controlled by Danfoss VLT® HVAC Drive FC 102 units with built-in condition-based monitoring (CBM) and DrivePro® Remote Monitoring service.
The monitoring service applies to 10 drives in the power range up to 18.5 kW. These drives operate in conjunction with cloud computing based on an industrial Ethernet standard. CBM improves real-time control of motor insulation status and load profile. Historical and real-time data are accessible from a web browser, which means the maintenance staff can analyze them from anywhere in the world.
The factory maintenance department receives notifications regarding any deviations from the baseline values. This enables staff to identify and react early when situations arise which can pose a risk of imminent failure, such as dirty filters or increased overload. The notifications also streamline the process of fault localization.
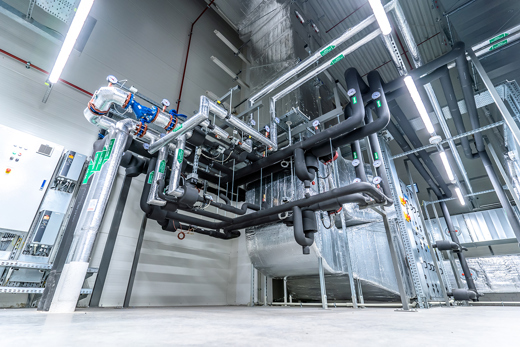
The outcome: 50% less energy consumption
The main benefit to the factory of Danfoss Drives technology, particularly CBM and remote monitoring, is a reduction in failures and increased uptime. The DrivePro® Remote Monitoring service has improved the efficiency of the entire maintenance department, facilitating the service process. By monitoring the operating condition of machinery, the personnel can prepare a detailed repair and maintenance plan. Spare parts are ordered well in advance so that there is no need to stock redundant components. Reducing the load on machinery has extended the life of the entire plant. Thus, the time spent on all service activities has been reduced and production continuity is maintained. Servicing and maintenance costs have decreased as well.
Full electrification, the use of energy-saving solutions (such as Danfoss drives) and the use of energy from renewable sources have made the newly built production hall in Grodzisk Mazowiecki climate-neutral. In this way, Danfoss reduces emissions and operating costs while taking care of employees’ well-being and getting a step closer to meeting climate targets.
Danfoss products installed in this project
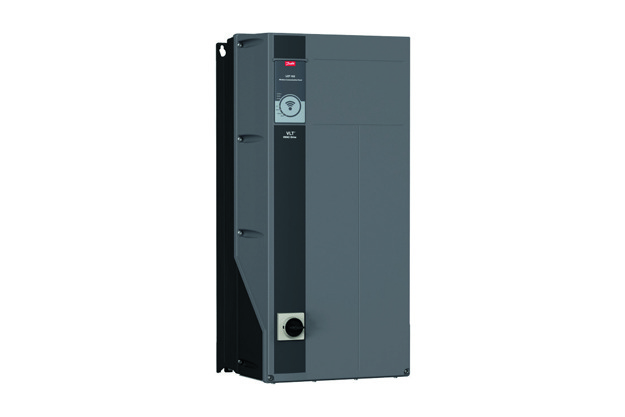
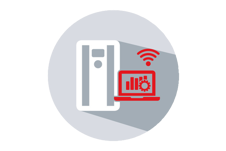
More case stories using condition-based monitoring
Case stories from factories
-
if (isSmallPicture) {
; } else if (isBigColumns) { } else { }How did this smart factory reach carbon-neutral?POLAND: The new Danfoss production hall in Grodzisk Mazowiecki has reached carbon-neutrality, thanks to full electrification, energy-saving solutions such as Danfoss drives, and energy from renewable sources.
-
if (isSmallPicture) {
; } else if (isBigColumns) { } else { }EC+ Concept drives optimal air conditioning at Volkswagen’s Navarra factoryHighly efficient axial fans controlled by VLT® HVAC Drive FC 102 at Volkswagen Navarra, Spain, delivered 20% energy savings in AHU operation.