In this article we will take a look at another standard component of commercial refrigeration systems: the solenoid valve. In almost every dry-expansion refrigeration system above a certain capacity, solenoid valves are used mainly in the liquid line. This is why we discuss this topic in some detail in this Fitters Notes article.
In this article we will take a look at another standard component of commercial refrigeration systems: the solenoid valve. In almost every dry-expansion refrigeration system above a certain capacity, solenoid valves are used mainly in the liquid line. This is why we discuss this topic in some detail in this Fitters Notes article.
Construction
How is a solenoid valve put together? Generally speaking, a solenoid valve consists of a coil and a valve body. The coil is fitted on an armature tube. With relatively small, direct operated valves, the moveable armature opens and closes the valve by directly opening or closing the valve seat.
The part of the armature that contacts the valve seat is fitted with a Teflon gasket to improve the internal media tightness of the valve.
Danfoss EVR v2 2 and EVR v2 3 valves are examples of this type of direct operated solenoid valve. Servo operated solenoid valves have the same sort of armature movement, but the armature opens or closes a servo bore instead of the main valve seat. In the case of membrane servo valves, the differential pressure over the valve causes the membrane to move, which in turn opens or closes the valve. The same principle is used in servo solenoid valves with a piston but no membrane. Here again the valve is opened or closed via the servo bore, but this is done using a piston mechanism instead of a membrane.
Classifying solenoid valves according to their rated capacity makes perfect sense. For instance, solenoid valves with a very small rated capacity, such as EVR v2 2 and EVR v2 3 valves, are direct operated. The EVR v2 6 and EVR v2 22 models, both of which have membranes and are servo operated, are used in larger systems. Finally, solenoid valves in the EVR v2 25 to EVR v2 40 series are used in dry-expansion systems with very high capacity. They are servo operated piston valves. If even these models are not adequate, a main valve (such as a Danfoss ICS or PM valve) can be converted into a solenoid valve by fitting a solenoid valve accessory (EVM). Systems of practically any desired size can be built using this type of combination.
A practical tip: if you open a solenoid valve and see that it does not have a membrane or a piston, it is usually a direct operated valve. This sort of valve also has relatively small connections, such as 6, 8 or 10mm.
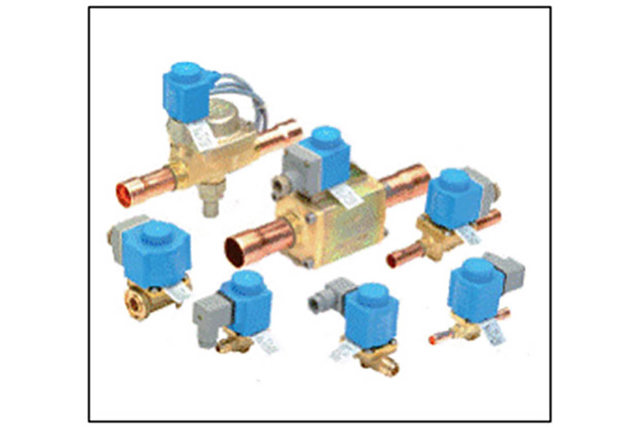
Why should an installation or service technician need to know whether he is dealing with a direct operated solenoid valve or a servo operated solenoid valve? The reason is that this is a decisive factor for the dimensioning of the valve.
Direct operated solenoid valves (such as EVR v2 2 and EVR v2 3 valves) do not need any minimum pressure drop for their operation. They are thus very well suited to partial-load operation, which allows the system to be configured for a moderate pressure drop under full-load conditions. With an assisted-lift servo operated valve, such as the EVRAT and EVRST (where "T" stands for assisted-lift servo operation), the same design criteria apply as for direct operated valves.
Here again there is no specified minimum pressure drop that must be taken into account. In contrast, with servo operated valves (EVR v2 6, EVR v2 10, EVR v2 15, EVR v2 20, EVR v2 22, EVR v2 25, EVR v2 32, and EVR v2 40 valves) the minimum pressure drop under partial load must be taken into account, in addition to the maximum pressure drop. The differential pressure under partial load must always be higher than the minimum differential pressure the valve needs for reliable operation. This minimum pressure difference is specified on the valve data sheet. For example, an EVR v2 10 valve has a minimum differential pressure of 0.05 bar. With a cooling capacity of 20kW, R134a and evaporation at -10°C and the valve installed in the liquid line, an EVR v2 10 valve is, in principle, not a bad choice because the 0.06 bar pressure drop under full load is more than 0.05 bar and is thus OK. However, if this system is then configured with two large 10kW compressors, for example, connected in tandem to the refrigeration circuit, the pressure drop will be less than the required minimum value when the system is operating with only one compressor. The calculated pressure drop in this case will be only 0.02 bar. In this case, the EVR v2 6 valve would be a better choice.
The minimum pressure drop for the EVR v2 6 valve is also 0.05 bar. The full-load pressure drop is 0.36 bar, and the partial-load pressure drop is 0.09 bar. Both values are higher than 0.05 bar, which means that the valve will operate reliably under all expected operating conditions. However, if, despite all your efforts, you cannot find a suitable valve for a system with a full-load cooling capacity that would normally call for using an EVR v2 6 or higher valve but also has excessively low differential pressure under partial load, it is technically possible to use a suitable main valve instead. Practical tip: a small main valve from the PM or ICS family fitted with an EVM pilot valve has excellent partial-load characteristics and can often be used in a situation where the desired partial load operation cannot be achieved with a standard EVR v2 solenoid valve. The drawback of this valve combination is its higher price compared with a standard EVR v2 model. Another option for partial-load situations of this sort is to use an assisted-lift servo operated valve, which has a minimum pressure drop of 0 bar. These valves, such as the EVRAT and EVRST valves, were originally designed for use with ammonia, but they can also be used in "copper-pipe" refrigeration systems.
Positioning
Solenoid valves are mainly used in the liquid line. It is estimated that 95% of all solenoid valves are installed there in refrigeration systems. It is advisable to place the solenoid valve close to the expansion valve, but this is not absolutely necessary.
Placing the valves close together minimizes the risk of liquid-hammer effects. However, as such effects are relatively rare in commercial refrigeration systems (manifesting themselves in the form of vibrating pipes and knocking noises when the solenoid valve opens), the solenoid valve can be placed in any desired location allowed by the structural conditions. The question as to whether the solenoid valve should be placed before or after the dryer/sight glass combination is essentially a matter of preference.
If you fit the solenoid valve upstream from the sight glass, you can observe the pump-down process when the system is switched to pump-down or pump-out mode. However, this arrangement is not specified as mandatory.
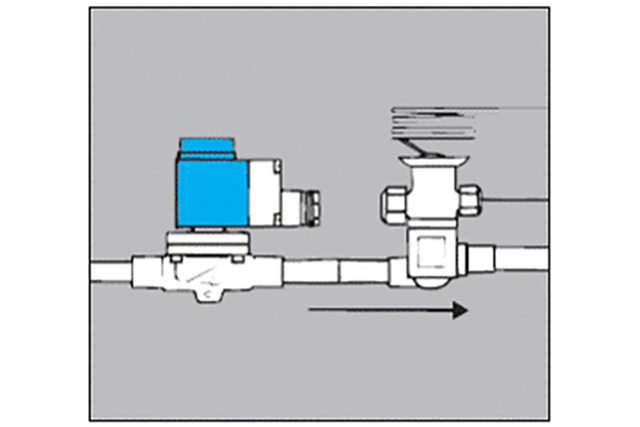
Solenoid valves for copper-pipe refrigeration systems are available with flare or solder connections.
The pipe can be connected to the flare connections in the conventional manner using a flaring tool or by means of flare adapters. Flare adapters have the advantage that they are considered to be threaded fittings instead of flare fittings and are thus exempt from certain restrictions described in the EN 378 standard. In addition, the valve can be replaced without soldering if this is necessary for service purposes. However, they have the disadvantage that in this case a fitting must be soldered onto the connection at each end. With solder connections, the pipes are typically soldered directly to the valve. This usually does not require the valve to be dismantled. Placing a wet cloth around the valve for cooling is usually sufficient.
EVR v2 solenoid valves should be installed in a horizontal section of pipe, preferably with the coil (armature tube) facing upward. If necessary under difficult installation conditions, the armature tube can be rotated to a horizontal position (with the tube connections horizontal and the armature tube facing to the side). Orientations between these two limits are also feasible.
Use
EVR v2 solenoid valves for refrigerants can also be used in other locations in a refrigeration system - not just in the liquid line. For example, they can also be used in the hot gas, condensate, suction or hot-gas bypass line.
If you use a solenoid valve in the hot gas or hot-gas bypass line or as a hot gas supply valve for hot-gas defrosting, you must pay particular attention to the maximum rated media temperature of the solenoid valve, which is 105°C for the EVR v2 valve. The crucial factor for using a solenoid valve in the suction line is the minimum rated media temperature, which is -40°C for the EVR v2 valve. You should bear in mind that evaporation temperatures as low as -45°C are not a problem here because the refrigerant is overheated by the time it reaches the suction line.
This means that the evaporation temperature of -45°C is raised by at least 7K. The resulting calculated value is -38°C, which is well within the specified operating range. If you want to install a hot-gas bypass valve in addition to a hot-gas bypass regulator, an EVR v2 valve is certainly a reasonable choice. However, if the solenoid valve is also supposed to perform regulation tasks and be operated with a cycle time measured in minutes, you should use an EVRP solenoid valve, which is specially designed for high cycle rates.
MOPD
One of the important parameters of a solenoid valve is the MOPD. MOPD stands for "Maximum Operating Pressure Differential", which means the maximum pressure difference that a particular combination of valve and coil can manage and still open if wanted.
The MOPD is largely determined by the solenoid valve type, but it also depends on the coil that is used. For example, an EVR v2 3 can hold 21 bar with a 10W AC coil or up to 25 bar with a 12W coil. This factor is not a problem if the valve is used in the liquid line with normal cooling operation.
However, if the system is pumped down, for example, because the solenoid valve is closed, and then switched off by the low-pressure switch, the solenoid valve must hold the full pressure difference between the high-pressure and low-pressure sides. To give an example, a system with R134a could have an evaporation pressure of 1 bar (gauge) with an evaporation temperature of -10°C and a condensation pressure of 10.5 bar with a 45°C condensing temperature. The solenoid valve would thus have to be able to manage 9.5 bar (= 10.5 - 1).
This is usually not a problem. The pressures are usually higher with R404A or R507, and in such cases you should be alert for possible MOPD problems. As a practical tip, in case of doubt you can use a "stronger" 12W coil in place of the standard 10W coil. This does not cost very much, never has any negative impact, and may help in a borderline situation.
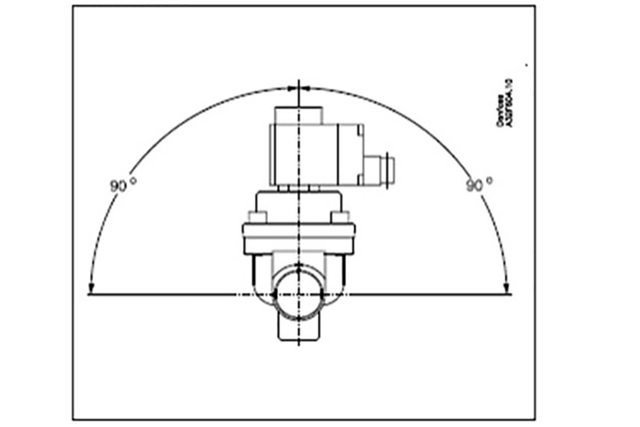
Coils are an important aspect of solenoid valves. The modern clip-on attachment arrangement could hardly be simpler: just slide the coil over the armature tube of the solenoid valve body, press until it snaps in place, and you're done. The coil is self-contained and closed on top. Check to make sure that the O-ring is fitted at the bottom of the armature tube (at the junction of the armature tube and the valve body) and is undamaged. The O-ring protects the coil against moisture (including atmospheric humidity).
The outside of the coil is vapor-proof, but water can penetrate from inside the coil (from the armature tube opening).
Moisture penetration from inside is the main enemy of a solenoid coil. If you have any older models of these coils, always check the seal at the top end of the armature tube as well. These models (designation "18Z" = old model, versus "18F" = clip-on model) are open at the top and bottom before installation and must be fastened (screwed in place) and sealed using suitable installation hardware. Practical tip: if you encounter a burst coil with the plastic shell bulging in places, this is usually the result of moisture penetration into the coil. If you can see brown rust spots on the inside of the coil, the sealing of the coil is most likely inadequate. You should pay special attention to correcting this situation properly during servicing (install a new coil and seal it with the O-ring).
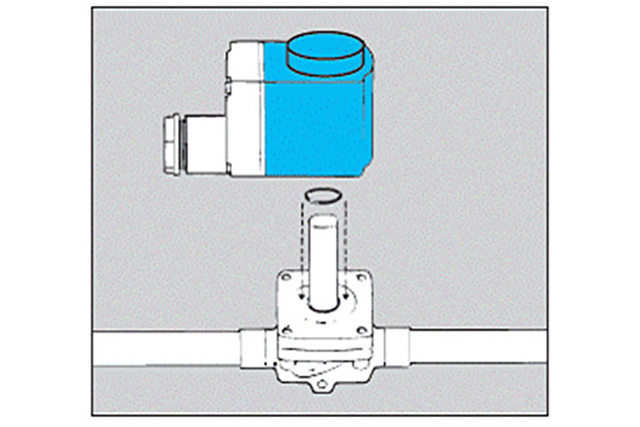
Solenoid valves are available in two types: NC (normally closed; i.e. closed when de-energized) and NO (normally open; i.e. open when de-energized). In most cases, an NC solenoid valve is used if it is installed in the liquid line. This has the advantage that the valve is closed when the system is not running and when the solenoid valve is not energized, which helps prevent refrigerant migration. For this reason, an electrical power failure does not lead to any problems with the refrigeration system. By contrast, using an NO valve can be especially beneficial if the valve only has to be closed for brief intervals. Although solenoid coils are not the biggest power gluttons in refrigeration systems, this can still yield a certain amount of savings in electricity costs over the years.
EVR v2 solenoid valves are available in the NC version for all capacity ratings (EVR v2 2 to EVR v2 40), but only the EVR v2 6 to EVR v2 22 models are available in the NO version. Practical tip: how can you see whether a solenoid valve is an NO or NC type if the type designation is no longer visible on the valve? The answer is that the top end of the armature tube of every EVR v2 solenoid valve has a circumferential groove used to secure the coil. This is the same for both types (NO and NC), but if there is a second circumferential groove at the bottom end of the tube (near the main solenoid valve body), the valve is an NO type. NC valves have only one groove on the armature tube.
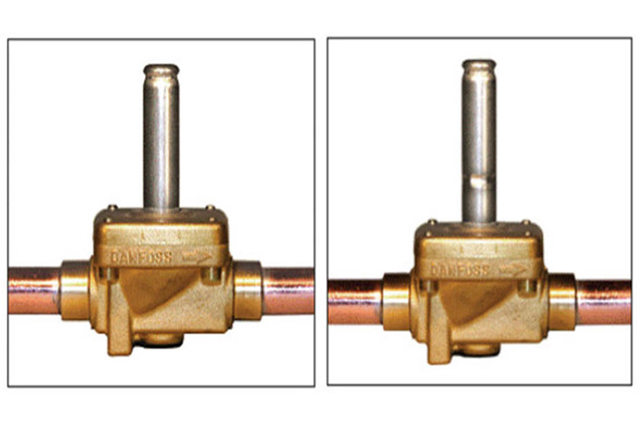
Learn more
For more information, please refer to the Fitters Notes chapter on solenoid valves. You may also explore our portfolio of solenoid valves for refrigeration and air conditioning.