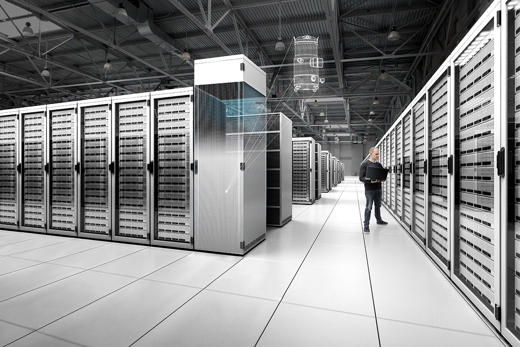
A Quest for Perfection
NEXTDC is a market leader enabling business transformation through innovative data center outsourcing solutions, connectivity services and infrastructure management software. It provides enterprise-class colocation services to local and international organizations. In July 2012, its M1 Melbourne data center — a 15MW hyperscale colocation facility went live.
NEXTDC is committed to sustainability and renewable energy, so it was no surprise when the M1 data center received a 4.5-star NABERS (National Australian Built Environment Rating Systems) rating in 2016 for incredible building performance. A good portion contributing this excellent rating was reflective of NEXTDC’s decision to install Smardt Chillers using Danfoss Turbocor oil free compressor technology.
But that wasn’t enough. They improved their systems even more, receiving a 5-star NABERS rating in 2019. The M1 data center became the first to ever receive 5 stars in Australia. Because of this reputation, maintaining and continuing its sustainable, efficient systems are essential to upholding its core business values and maintaining its 100% uptime guarantee for its customers.
Yet, that begs the question — how can you improve something that’s already top-rated?
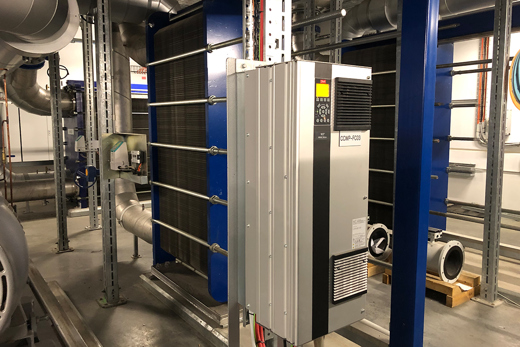
Test for the best
NEXTDC consulted with the Smardt Chiller Group, a longtime OEM partner of Danfoss, to help them further improve the efficiency of their cooling system. When they expanded in 2016, they added three additional Smardt chillers in to maintain maximum efficiency of their M1 Facility.
In applications like data centers, the cooling system typically has a high number of run hours in order to protect the servers that generate quite a bit of heat on a 24/7 basis. This is quite different from traditional cooling applications for office buildings and schools, the system may only run 50% of the year. Therefore, any improvements in efficiency on the cooling systems in data centers can create major annual energy savings.
In recent years, data centers have been utilizing various technologies to cool their equipment in the most efficient way possible. Further, they are pushing the operating envelope in the server rooms by operating at higher temperatures. This enables the chiller to consume less power but also challenges the compressor operating map. In response, Smardt collaborated with Danfoss to expand the operating map of their oil-free Danfoss Turbocor® compressors in order to allow it to operate at the higher water temperatures while also enabling for operation at lower ambient conditions.
Compressors operating in these two areas, high chilled water temperatures and low ambient conditions, run at low compression ratios or “low lift.” Operation in this area offers significant energy savings but required some changes to the compressor. Smardt and Danfoss engineers overcame these challenges by developing a technology which implements software changes and other improvements needed to allow the oil-free centrifugal Turbocor compressor to run at low lift. The Smardt team then developed the software to optimize the operation in these low lift conditions.
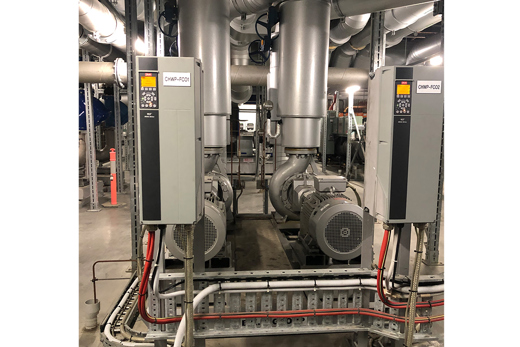
Low lift, high reward
Smardt piloted this new low-lift configuration, SmardtLiftTM, with NEXTDC which was installed on one of their Smardt chillers at the M1 data center facility. The pilot proved that the chiller could run quite efficiently during low-lift scenarios. This means that it will activate when the ambient temperature of the data center is within an optimum threshold of what the cooling system requires. This method significantly cuts energy costs of the chillers — by 31% (depending on the ambient conditions)! This validation of savings paves the way for upgrading the remaining chillers and creating even greater savings for the facility as a whole.
This low-lift operation produces the highest efficiency possible today for oil free chillers. Oil-free chillers also mean there is no performance degradation over time, where oil based chillers typical lose 10-30% of their capacity and efficiency over the life of the chiller; mainly caused by oil coating the heat exchangers and act as an insulator which inhibits optimum heat transfer (see ASHRAE 601 paper for more details).
The Danfoss Turbocor compressor also supports the data center’s 100% uptime guarantee requirements due to multiple compressor chiller configuration versus single compressor oil based chillers. Plus, because there is no oil system which hinders fast startup times, Smardt chillers powered by Danfoss Turbocor offers 30-second fast re-start — the shortest restart time in the industry.
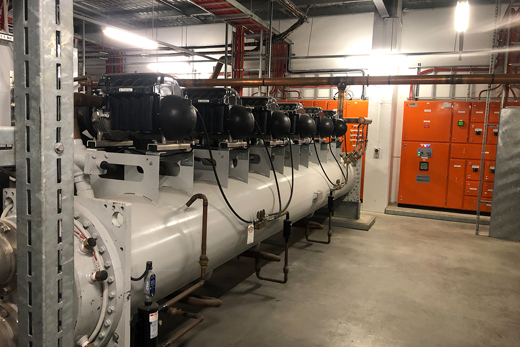
Total solutions provider
Not only was Danfoss and Smardt able to engineer a solution that can operate efficiently in low-lift conditions, but they also collaborated closely to validate this new solution. In this world class plant, the large heat exchangers and the variable speed drives that were needed to complete the hydronic system were also manufactured by Danfoss. This demonstrates Danfoss’s understanding of the total cooling system.
The solution has performed so well at the M1 Melbourne plant that NEXTDC has decided to roll out the SmardtLift low-lift chiller configuration across its fleet of data centers — improving their efficiency across the board.
Who knew that the trick to improving the most well-oiled machine was a customized oil-free chiller?
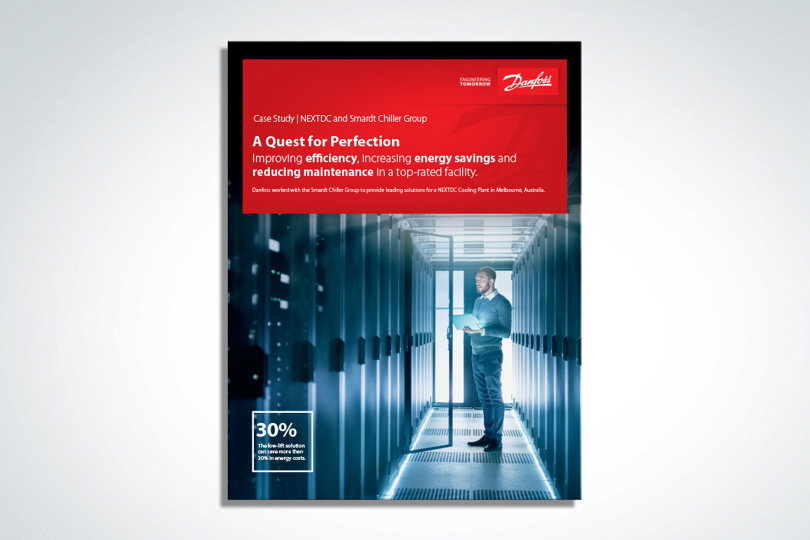
Download Case Study PDF
View related products
-
if (isSmallPicture) {
; } else if (isBigColumns) { } else { }Turbocor®Danfoss is the leading manufacturer of oil-free compressors and is the pioneer of the Danfoss Turbocor® compressor - the world’s first oil-free magnetic bearing compressor for the HVAC industry.