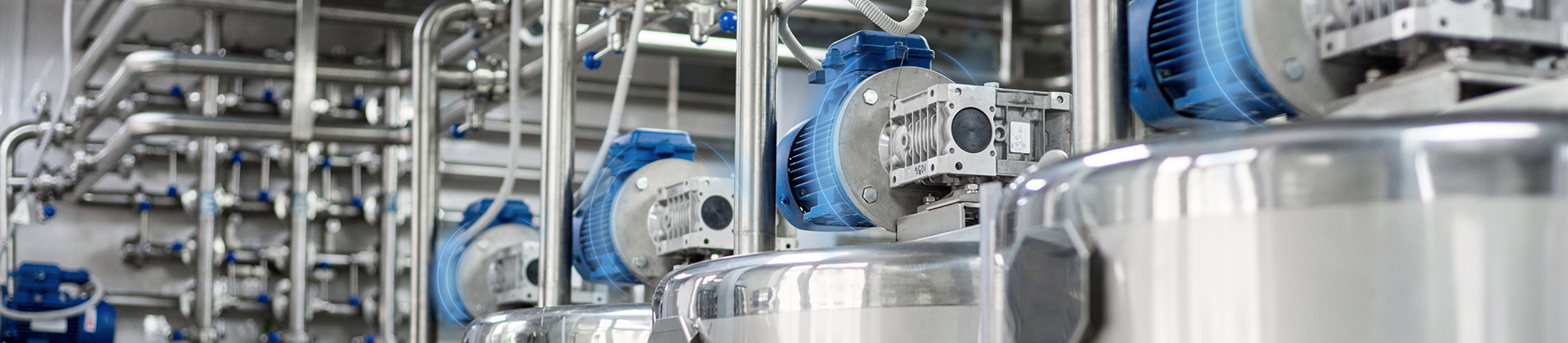
Integrated CBM in one comprehensive package
Condition-based monitoring (CBM) integrated into premium Danfoss drives has revolutionized the way these drives monitor electric motors for faults and potential failures. With breakthrough technology implemented at the drive level, CBM offers advanced features such as motor stator winding monitoring, vibration monitoring, wear-out monitoring of bearings, load envelope (torque) monitoring, and cavitation detection,Ā all in one comprehensive package.
Improving performance via a motor monitoring system
The benefits of CBM for motors are significant. Monitoring performance using CBM provides a simple and cost-effective way to obtain machine data for smart maintenance decisions. With CBM, there is no need for specialized expertise, as existing user interfaces are supported. CBM can be used in a wide range of applications and motor ratings. Itās also reassuring to know that CBM operates independently of the cloud, using edge computing in the drive, ensuring data privacy and security.
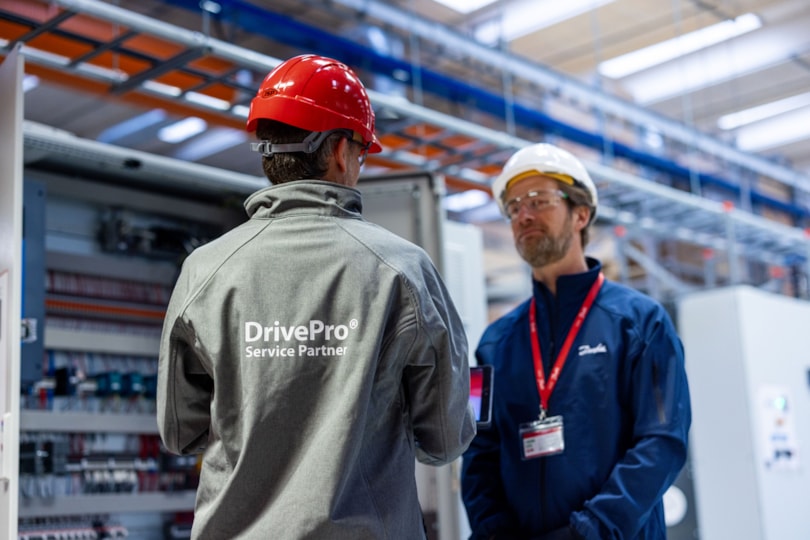
Explore long-term savings now
In today's competitive landscape, itās crucial to make the most of your CAPEX. Invest in a proactive maintenance strategy that goes beyond just the sale. By prioritizing early detection and consistent upkeep, youāre not only safeguarding your investments but also driving long-term savings.
Make the shift from scheduled maintenance to predictive maintenance
Enable your maintenance decisions based on application data. By enabling early warnings and notifications,Ā CBM increases production uptime by allowing operators to take action on alerts, to perform necessary remedial actions before an unscheduled breakdown occurs. It helps identify damaged motor windings, increasing vibration levels, squealing bearings, and unusual torque values. CBM also allows for theĀ transition from scheduled maintenance toĀ predictive maintenance, increasing the efficiency and effectiveness of maintenance strategies. It is a cost-effective solution compared to external complex systems offered by third parties.
Example: The ability to prevent unexpected breakdowns is especially significant in an aseptic manufacturing environment. One pharmaceutical company conducted tests to prove that intelligent Danfoss drives with integrated condition-based monitoring provideĀ reliable ventilation in an aseptic environment.Ā The drives help to prevent downtime with real-time system monitoring and customizable instant alarms, which provide an early warning enabling operators to take preventive action.
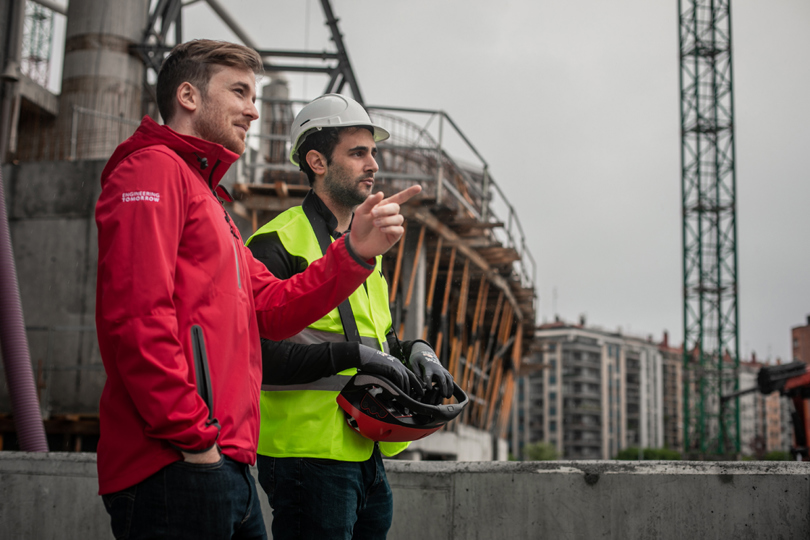
Motor condition monitoring for remote locations
CBM isĀ especially suitable for remote locations or devices that are difficult to access. With permanent monitoring, potential faults can be detected and addressed before they result in motor failure and production downtime. By taking maintenance strategies to the next level with CBM, industries can increase their application uptime, reduce maintenance costs, and enhance overall operational efficiency.