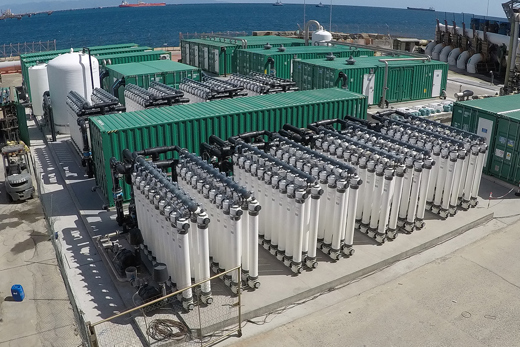
The process of seawater desalination is intrinsically energy intensive. Therefore, operating costs related to electricity consumption are very significant and directly impact the sustainability and profitability of a desalination plant.
However, technologically advanced solutions allowed Acciona to create an innovative sea water reverse osmosis (SWRO) modular desalination plant for the Sarlux refinery in Sardinia, Italy, reducing energy consumption compared to traditional solutions.
The system designed and developed by Acciona includes four modular reverse osmosis desalination lines, which supply a total of 12,000 m3 ultrapure water daily with a guaranteed 97% availability over the entire year, thanks to Danfoss solutions.
By employing sophisticated products such as the VLT® AQUA Drive, Acciona was able to optimize the overall efficiency of the plant. The space requirements for the drive are minimal, thanks to the extreme compactness of this AC drive.
And while a typical reverse osmosis desalination plant based on centrifugal high-pressure pumps and recuperators typically requires around 2.7 kW per m3 of water produced, on this site the volumetric high-pressure pumps and iSave isobaric recuperators enable the production of ultrapure water with energy consumption as low as 2.4 kW/m3. This reduction represents 11% savings in energy consumption.
Related products
-
if (isSmallPicture) {
; } else if (isBigColumns) { } else { }iSave® energy recovery devices for high-pressure membrane applicationsThe 3-in-1 Energy Recovery Device (ERD) optimized for sea water reverse osmosis applications.
-
if (isSmallPicture) {
; } else if (isBigColumns) { } else { }DST P40I titanium pressure transmitter for harsh environmentsFor use in corrosive environments, Danfoss offers the new robust DST P40I pressure transmitter made of Titanium and with ceramic pressure sensing element. DST P40I is optimized for use in applications such as desalination systems, seawater cooling, and chemical processing.
-
if (isSmallPicture) {
; } else if (isBigColumns) { } else { }VLT® AQUA Drive FC 202VLT® AQUA Drive FC 202 controls all types of pumps and comes equipped with a cascade controller.