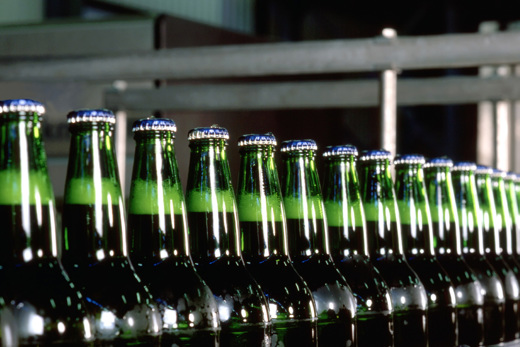
Relying on Danfoss VLT® FlexConcept® to control the motors on their new inspection line, FORST Brewery has increased efficiency with significant energy savings.
Beautifully situated in the Italian Alps, close to the Austrian border, FORST Brewery has produced beer since 1857. Combining natural products to produce first class beer has always relied on mastering the balance between time, temperature and technology.
Technology Upgrade
In 2011 the Lagundo based brewery embarked on a project to replace its old rotary inspecting machine on the bottling line with a new on-line inspecting machine fitted with VLT drives and Danfoss’ VLT® OneGearDrive®.
Commissioned in 1989 the now obsolete line inspected returnable and non-returnable containers and was built with traditional motors controlled by a centrally installed Danfoss VLT® 3000 frequency converter. The new system is a significant upgrade in terms of both efficiency and ease of maintenance.
Already well acquainted with Danfoss drives, FORST had VLT drives in bottling and keg filling lines and also in the many process applications crucial to beer production: transfer pumps, washing pumps, water supply pumps and also the air conditioning systems that carefully control the temperature as the beer moves through the production process. It seemed logical to continue and remain within the same control concept.
VLT FlexConcept Increases Efficiency
The speed of the new conveyor belts is controlled by Danfoss VLT FlexConcept. Specially developed for conveyor applications in the food and beverage industry, the solution consists of a VLT OneGearDrive in combination with either a VLT® AutomationDrive FC 302 or a VLT® Decentral Drive FCD 302 frequency converter.
A total of 10 OneGearDrives, in the EHEDG compliant hygeinic version, and 10, 1.5 kW, FC 302 units now control the line that has a capacity of 50,000 bottles per hour. The retrofit was completed in two weeks, and has enabled FORST to improve the production process with softer acceleration and deceleration ramps for increased conveyor stability. In addition the new setup has increased energy efficiency by about 25% compared to the old system.
Mr. Floretta, head of the technical department at FORST, who coordinated both the installation of the original line and now also the upgrade, is satisfied with the results of the new line:
“The OneGearDrives have provided significant savings in the installation and commissioning of the plant. They integrate perfectly with the environment and also convey a visual sense of cleanliness and functionality.”
At a Glance
- What: Inspection line upgrade
- Where: Birra FORST S.p.A.; Lagundo, Italy
- When: 2012
- Business area: Brewery
- Type of project: Retrofit
- Products: VLT® FlexConcept® consisting of 10 VLT® OneGearDrive®, Hygienic and 10 VLT® AutomationDrive FC 302
About FORST
BIRRA FORST SpA was founded in 1857. In 1863 ownership was transferred to Josef Fuchs to become a family dynasty where the fourth generation continues to ensure the quality drinking experience made famous the by original brewers.
The brewery is one of Italy’s largest and produces 700.000 hl beer per year, using a mix of traditional techniques and cutting edge technology.