NETHERLANDS: To meet growing demand for pipe repair clamps and modernize the manufacturing process, Huwa International Pipeline Products set out to automate its pickling line. Pickling is a method of reinforcing welded joints in steel products where the metal is immersed in a bath of nitric acid and then cleaned. The pickling line employs a biaxial gantry crane that has customarily required servo technology — an expensive and complex solution. By choosing the Danfoss VLT® AutomationDrive FC 302 with its Integrated Motion Controller functionality, Huwa successfully developed a fully automated pickling line with optimum reliability at a reasonable price.
Discover how Huwa International Pipeline Products improved worker safety and reduced lead times on its pickling line with Danfoss VLT® AutomationDrive FC 302 and its Integrated Motion Controller (IMC).
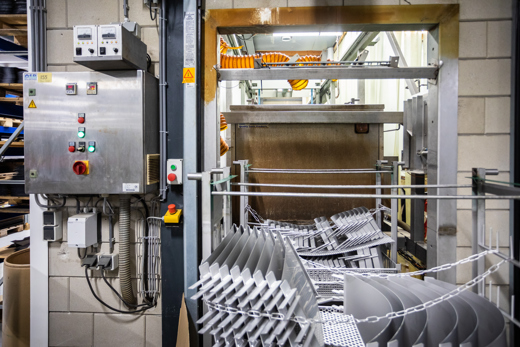
The challenge: Cost-effective precision and reliability
Leaky pipes can lead to a myriad of consequences — commercial to environmental, structural to societal. While replacing a leaky pipe may seem preferable, patching it on site with repair clamps is significantly faster and cheaper.
United Pipeline Products is the largest producer of pipe repair clamps in Europe. The company was formed in 2010 following the merger of six analogous Dutch companies, including Huwa. In fact, United Pipeline Products is one of the world’s leading manufacturers of stainless steel repair clamps. But with increasing global demand for these repair clamps and the use of hazardous chemicals in their production, Huwa decided a change was required in the manufacturing process.
When constructing stainless steel repair clamps, certain parts are welded together, but welding weakens the steel’s properties. To counteract this, clamps are ‘pickled’ —immersed in a bath of nitric acid — and then cleaned. To meet contemporary OH&S standards, Huwa no longer wanted employees to enter the room with the pickling line. Additionally, Huwa hoped to make its pickling line more efficient. The lead time for a basket of parts to be put through the pickling line was two hours, while the process itself took one hour.
The pickling line is a linear setup with four pickling stations, two rinsing steps, an ultrasonic bath and a dryer. To fully automate the process, Huwa needed a drive to control the biaxial gantry crane that hoists baskets of parts in and out of the baths.
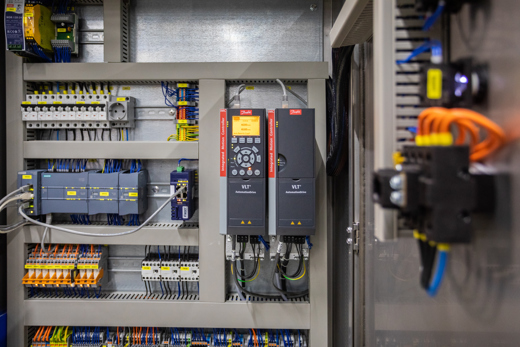
The solution: VLT® AutomationDrive FC 302 with IMC
In collaboration with local production-line specialists Hellings Machinebouw and electrotechnical supplier Van Egmond, Huwa settled on the VLT® AutomationDrive FC 302 to control the gantry crane.
Traditionally, servo drives have been used for these types of positioning and synchronization operations — an expensive, complex, and often unreliable solution. By contrast, the VLT® AutomationDrive FC 302 with its IMC functionality is much cheaper and more robust. It is also easier to use, maintain and adjust. All this with only a fractional reduction in dynamic performance compared to servo technology.
IMC is an innovative alternative to servo control. Essentially, IMC is software functionality that enables an AC drive to perform high-precision positioning and synchronization operations without the need for additional modules or hardware. It is also configured via parameters for easier, faster, safer, and cheaper set-up — there is no need for advanced programming or servo technology knowledge.
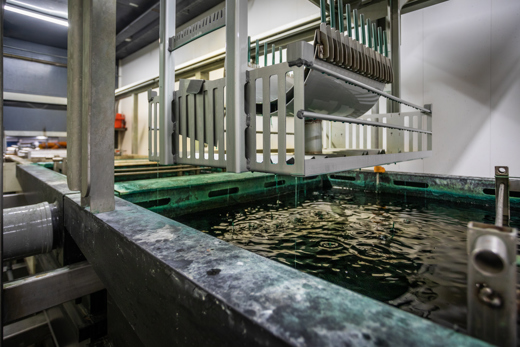
The outcome: Maximum uptime and rapid ROI
Since September 2021, Huwa’s fully automated pickling line has been 100 percent reliable. With its IMC functionality, the Danfoss VLT® AutomationDrive FC 302 has achieved much faster lead times, while Danfoss’ overall support has been described as “top notch”.
The Danfoss VLT® AutomationDrive FC 302 has also proven itself to be highly adaptable. New movement profiles for the gantry crane are calculated quickly and executed seamlessly. Combining this with maximum uptime thanks to the Danfoss VLT® AutomationDrive FC 302’s robust construction, Huwa’s pickling line is no longer a bottleneck in its manufacturing process.
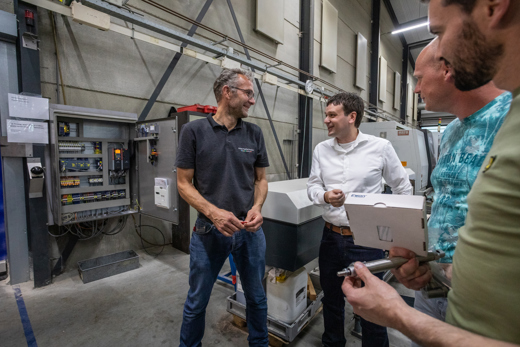
Benefits of Integrated Motion Controller (IMC) functionality:
- Compatible with all conventional motor technologies, with closed loop and open loop control
- Lower purchase cost due to fewer components
- Reduced electrical and mechanical installation time and cost
- No advanced programming or servo technology knowledge required — minimizes risk of errors in set-up
- Sensor-less homing with torque detection
- Reduced maintenance costs — maximum uptime
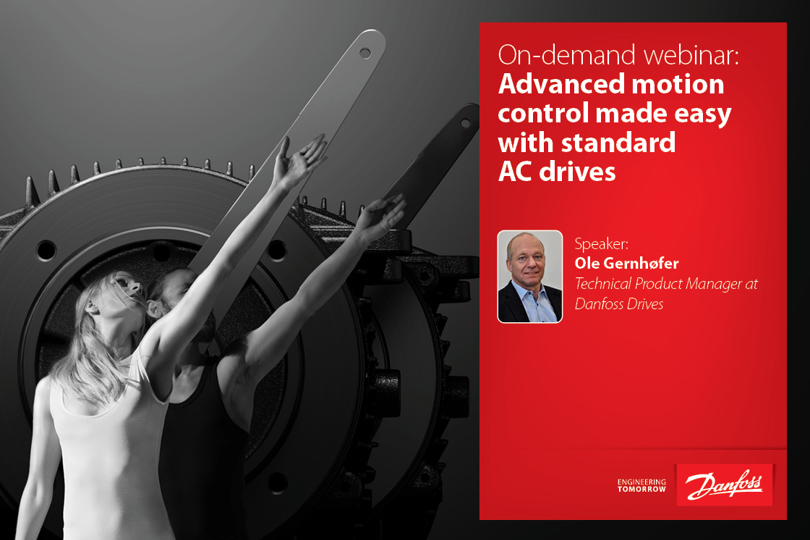
Curious to learn more about Integrated Motion Controller?
Discover the product
Coming soon...
Coming soon...
Related case stories
-
if (isSmallPicture) {
; } else if (isBigColumns) { } else { }Italcementi enjoys optimized process performance in all conditionsItalcementi chose the VLT® AutomationDrive FC 302 to ensure optimized process performance in their harsh environments.