DENMARK: Copenhagen has adopted the ambitious goal of becoming a CO2-neutral city by 2025, and district heating plays an important role. The FlexHeat demonstration plant at Copenhagen’s Nordhavn harbor, which supplies cruise ship terminals with district heating, shows just how far you can get with electrification and sector coupling. It emits 315 fewer tonnes of CO2 annually, compared with the LPG gas-based alternative.
District heating based on ground water
The HOFOR (Greater Copenhagen Utility) district heating in Copenhagen's Nordhavn district was established in 2018 as a demonstration project in EnergyLab Nordhavn, that also supplies three cruise ship terminals and the nearby UNICEF warehouse. The FlexHeat plant comprises a heat pump based on ground water that is retrieved from a 150 m deep well. The saline 10.5°C water is pumped through a heat exchanger with ammonia as a refrigerant. The temperature is raised in two steps via two compressors, and in a heat exchanger, the heat from the condensed ammonia is transferred to the district heating water, which then leads into a storage tank and is pumped out to consumers at the three cruise ship terminals and the UNICEF building. Altogether, the FlexHeat facility has a heating capacity of 1 MW.
FlexHeat facility schematic diagram, Wiebke Meesenburg, DTU Mechanical Engineering
4 MWh virtual battery
One way of creating flexibility in power consumption is through sector coupling, where excess electricity is stored in other energy systems. In the district heating supply, heat pumps with thermal storage can use power when it is plentiful and therefore inexpensive; and avoid using it in periods with peak loads in the system, for example, late afternoon, when most people come home from work and turn on lights and household appliances. The HOFOR (Greater Copenhagen Utility) FlexHeat project in Copenhagen's Nordhavn is a prime example of this type of sector coupling. The thermal energy storage consists of 100 cubic meter tank and corresponds to a "virtual battery" of 4 MWh.
Smart operation ensures flexible power consumption
The FlexHeat plant can operate in six different modes. Intelligent switching between these modes ensures the plant runs as effectively and economically as possible in relation to electricity prices, and the weather forecast. For example, when wind turbines are harvesting at full power, prices are low and the FlexHeat facility can contribute to a higher coefficient of exploitation of green energy.
The challenge is that the purchase of electricity has to be determined a day in advance, before the market closes.
Tore Gad Kjeld, Energy Planner at HOFOR, explains: “Smart-operation of the facility is based on electricity prices and a weather prognosis, where we take into consideration the power consumption viewed historically under similar weather conditions. Along with current operation data, these data are fed into an algorithm, which helps us work out a plan for the next day’s use of electricity. The machine learns a bit every time, getting smarter and smarter because of the data that we feed into the system. This type of machine learning will make us even better in the future at operating the facility according to favorable electricity prices.”
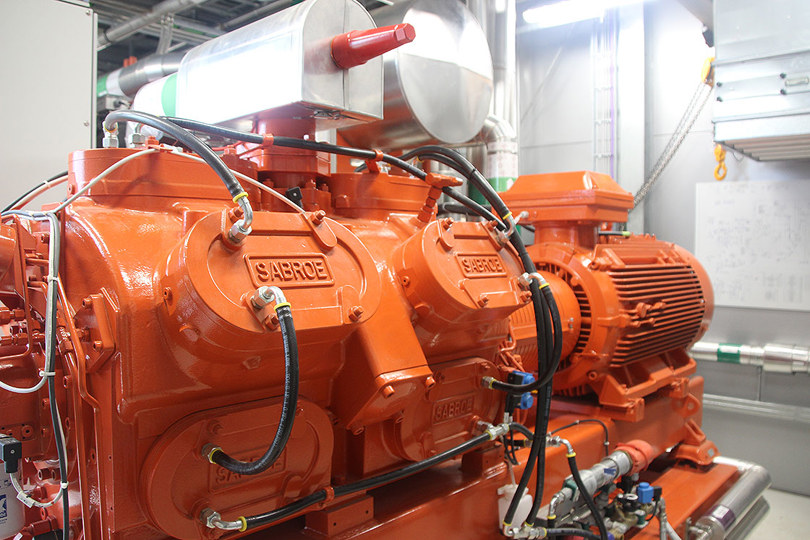
VLT® drives facilitate fast response
An electric boiler regulated by VLT® drives allows for a small boost in temperature, so the plant can quickly provide heat to customers from the storage tank in periods where electricity prices are highest. “VLT® AQUA Drive units can accelerate the heat pump from minimum to maximum performance in just a few minutes, while the electric boiler can be adjusted upward in just a few seconds,” explains Tore Gad Kjeld, energy planner at HOFOR.
Savings on electricity bills and CO2 emissions
How much CO2 can the HOFOR FlexHeat plant at Nordhavn save the environment? Tore Gad Kjeld estimates that the savings today are about 315 tonnes of CO2 annually, seen in relation to LPG gas boilers, which would be the best fossil-fuel alternative to a district heating solution. And, in the future, when the electricity uptake becomes 100% green, the savings can potentially reach up to 430 tonnes of CO2 annually.
VLT® AQUA Drive FC 202
Discover how VLT® AQUA Drive FC 202 controls and protects all types of pumps. This drive is optimized for water and wastewater applications, and comes equipped with an integrated cascade controller.
District heating and cooling case studies
-
if (isSmallPicture) {
; } else if (isBigColumns) { } else { }Unlocking efficiency with a drive retrofit at a Czech hydropower plantCZECHIA: When 80-year-old gears were replaced by variable speed control at the Albrechtice hydropower plant, power production increased by 10%.
-
if (isSmallPicture) {
; } else if (isBigColumns) { } else { }DrivePro® services enhance security of heat supply for 49,000 apartments in GliwicePOLAND: At district heating company PEC Gliwice, AC drives reduce energy consumption of electric motors by up to 40%. DrivePro® Site Assessment audits help ensure optimal efficiency.
-
if (isSmallPicture) {
; } else if (isBigColumns) { } else { }Electrification and sector coupling achieve CO2 goals at FlexHeat NordhavnDENMARK: The FlexHeat district heating plant at Copenhagen’s Nordhavn harbor emits 315 fewer tonnes per annum of CO2 than the LPG gas-based alternative.
-
if (isSmallPicture) {
; } else if (isBigColumns) { } else { }Seawater cools Copenhagen city, cutting emissions by 70%DENMARK: Two district cooling centrals in Copenhagen use seawater from Copenhagen Harbor for their cooling systems. For seven years, VLT® drives controlling pumps and compressors have proven their worth, ensuring high efficiency and impressive security of supply.
-
if (isSmallPicture) {
; } else if (isBigColumns) { } else { }World leader in biogas reduces CO2 emissions by 50,000 t annuallyBy generating power and heat from biogas instead of fossil fuels, MEC-BioGas reduces its CO2 footprint by 50000 tpa. Danfoss VLT® drives ensure optimal uptime in the 24/7 operations.
-
if (isSmallPicture) {
; } else if (isBigColumns) { } else { }Full-scale biogas plant in Kalundborg ensures the return of all nutrients back to natureAC drives from Danfoss help convert biomass from insulin and enzyme production to energy.