Excellence in electric main propulsion
Electric-based main propulsion provides a great deal of freedom in ship design, and ships can be designed much more efficiently without the traditional limits on equipment layout, due to mechanical restrictions.
Benefits of electric propulsion:
- The power can be supplied by any number of generators, which enables high redundancy
- The motor + drive combination consumes energy only when the azimuth thruster is actively turned
- The environment benefits from lower fuel consumption and exhaust gas emission levels
- Electric propulsion is a good platform for the next phase of development – hybridization.
Generally speaking, the design of vessels with modern electric propulsion systems, either diesel electric, LNG electric or even fully electric, can be quite easily converted to a hybrid solution. In the best case, just by adding a parallel E-Storage system, a vessel can be operated utilizing battery power for example for peak power demand. In some cases, the optimum solution is to use DC power distribution instead of, or in conjunction with, traditional AC power distribution.
Danfoss Drives’ solutions for the marine and offshore industry have the highest number of class type approvals from nine authorities: DNV-GL, ABS, Bureau Veritas, Korean Register, CCS, RINA, Lloyds Register, RMRS and Class NK.
This gives you the best possible choice when selecting drives for your marine application.
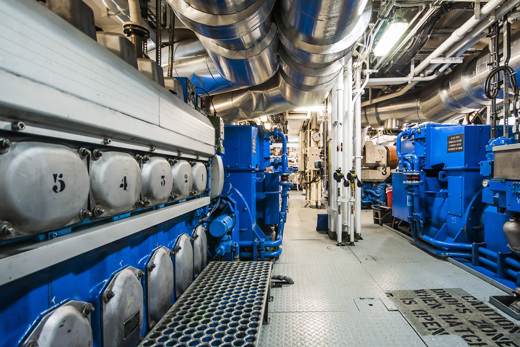
Shaft generator for optimal propulsion with PTO/PTI
Many long-haul vessels are still operating with direct diesel propulsion and no electric propulsion system at all. These vessels can improve efficiency and optimize main engine load power and emissions by adding a shaft generator/motor between the propeller and the main engine. This solution, called Power Take Out and Power Take In (PTO/PTI), is an electrical add-on which makes these vessels more efficient and even ready for hybridization. In hybrid vessels, a shaft generator/motor with AC-drive technology allows the optimum control of propulsion machinery at various speeds, which saves energy.
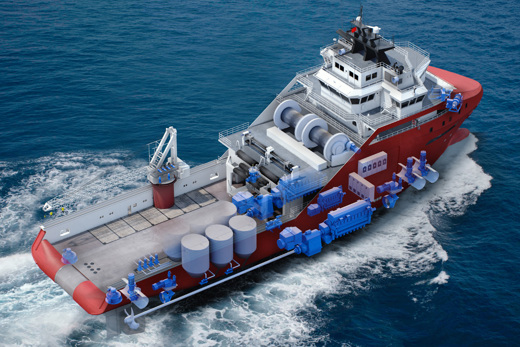
Clean hybrid propulsion
AC drives have key roles in hybridization and integration, and offer answers for the marine and offshore industries, which are looking for ways to reduce consumption of diesel oil and minimize emissions. A move towards using cleaner fuels like liquefied natural gas (LNG) is already in place. The future will be a move towards the operation of fully electric vessels. In the meantime, shipyards and vessel owners are investing more and more in marine hybrid systems to increase flexibility in design and installation, optimize operational performance and minimize the environmental impact. Many vessel types from small shuttle ferries to huge aircraft carriers can utilize hybridization technology for a more efficient and cleaner performance.
The benefits are clear business drivers:
- improved vessel performance
- reduced emissions
- lower operating costs due to lower fuel consumption
- lower maintenance costs related to diesel engines
- reduced noise levels
- improved long-term efficiency of the power supply system
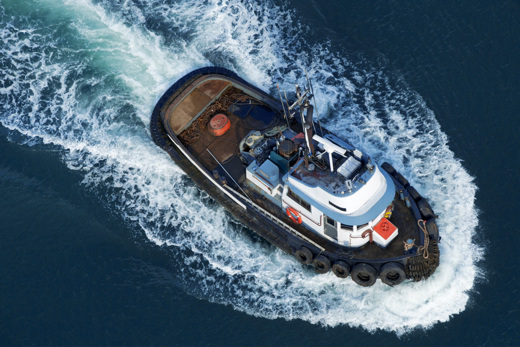
How hybridization works
Hybridization utilizes AC drives in the form of power conversion and grid converter technology. VACON® drives are in place when hybridized energy production is used with generators, and hybridized loads is used, for example, with propulsion and cranes.
Hybrid vessels run using two or more power sources: Main engines and generators are usually combined with integrated energy storage in the form of batteries or super capacitors. The intention is first to hybridize either the energy production to ease up the main engine optimization and secondly to hybridize all machinery consuming the energy to optimize machine behavior.
The marine and offshore industry recognizes the potential of using hybrid power and innovative propulsion systems. They reduce emissions and improve fuel consumption while extending engine maintenance intervals and engine life. With hybrid solutions, it is even possible to reduce the size of the engine, saving investment costs and space on board.
In energy production, the flexibility comes in the form of ‘time’. Energy storage gives time for generation to react to changes in loading conditions in an optimal way. On the load side, loading behavior is not reliant on generation and is ‘time’ constant.
Proven feedback and design targets from operating hybrid vessels has shown that using multi-source energy solutions to power vessels can reduce fuel consumption by 20–30%. You can choose to stop a diesel engine and run on battery or a smaller generator, or disconnect the battery or generator and start the engine again.
In the case of special vessels like tugs and support vessels, for example, they spend a lot of their service time idling with the main engines running and ready to respond, but no power is actually being used for propulsion. With hybrid solutions, batteries and smaller diesel generators can be used to provide energy to the vessel when it is idling, in standby operation, while harbor transiting short distances. A similar process can be used with regard to ferries operating in start/stops and scheduled routes. With regard to dynamic positioning, batteries can be used to provide the power for propulsion until the additional main engine is started and accelerated to provide long-term power for propulsion.
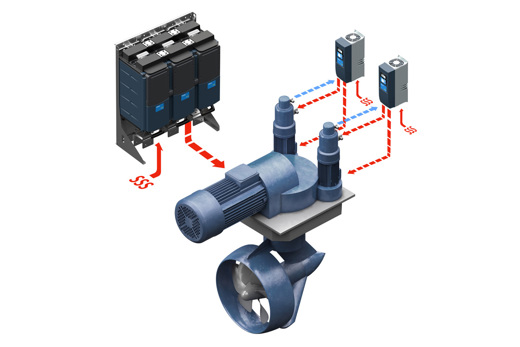
Thruster control for precision maneuver
Precise maneuverability in all seas is what you need from a thruster, and that is what Danfoss drives deliver, with their high torque capabilities and fast, accurate performance.
Danfoss drive controlled variable speed propellers with fixed pitch are typically 20-30% more energy efficient than fixed-speed variable-pitch propellers – which waste approximately 20% of the power at zero thrust.
Frequency-controlled variable-speed propellers use 50% less energy than hydraulic variable-speed propellers. The need for special motor preheat function eliminates an anti-condensation heater.
Electrically-steered azimuth thrusters deliver more accurate control and respond more quickly than a hydraulic steering system. A minimum of two parallel motors and drives are always in use. If one combination stops, the steering system continues to operate.
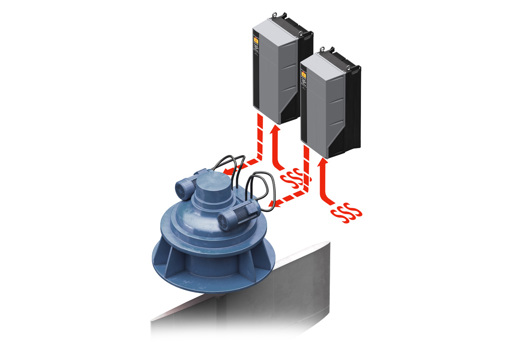
Steering gear
With variable-speed control, you can achieve accurate rudder positioning, enabling a precise analog control system. In rotary-vane steering gear with reversible hydraulic pumps, use a VLT® or VACON® drive to change speed and direction, saving energy by only running when the vessel is changing course.
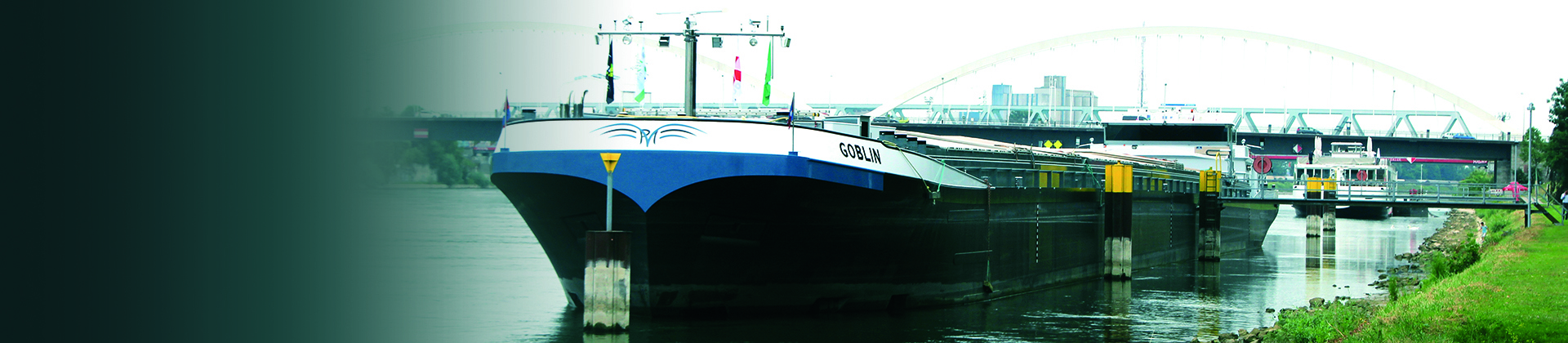
Hybrid efficiency in bulk carrier shipping propulsion
A hybrid diesel-electric propulsion retrofit has paid off fast for this dry cargo bulk carrier business.
Products
-
if (isSmallPicture) {
; } else if (isBigColumns) { } else { }VACON® 3000This range of modular medium-voltage drives (MV drives) empowers systems integrators and OEMs, delivering a whole new approach to attaining the ultimate in performance, exactly tailored to the needs of each medium voltage drive application.
-
if (isSmallPicture) {
; } else if (isBigColumns) { } else { }VACON® NXP System DriveConfigured and assembled to meet your needs whether you need to control one or several motors.
-
if (isSmallPicture) {
; } else if (isBigColumns) { } else { }VACON® NXP DC/DC ConverterMaximizes the energy yield in hybrid solutions and helps improve performance by bringing energy support close to the consumption.
-
if (isSmallPicture) {
; } else if (isBigColumns) { } else { }VACON® NXP Common DC BusEnables system integrators, machine builders and OEMs to design and build efficient industrial drives systems. Active Front-end (NXA), Non-regenerative Front-end (NXN), Brake Chopper (NXB) and Inverter (NXI) configurations are available.
-
if (isSmallPicture) {
; } else if (isBigColumns) { } else { }VACON® NXP Liquid CooledWell-suited to applications where air quality is critical, space is limited and efficient heat transfer is required. Active Front-end (NXA), Non-regenerative Front-end (NXN), Brake Chopper (NXB) and Inverter (NXI) configurations are available.
Case studies
-
if (isSmallPicture) {
; } else if (isBigColumns) { } else { }STX ocean research vessel meets 2025 efficiency targets, todayLeading Korean shipbuilders enhance their vessel performance with assistance from Danfoss for optimized operation, increased efficiency, improved quality, and greater customer satisfaction. Danfoss delivers innovative marine solutions introducing new standards for energy efficiency, expanding opportunities for the shipbuilding industry.
-
if (isSmallPicture) {
; } else if (isBigColumns) { } else { }Battery retrofit saves fuel and improves air qualityDenmark’s shortest ferry route is now a pioneer of battery power.
-
if (isSmallPicture) {
; } else if (isBigColumns) { } else { }38% fuel savings and emission reductions for CMAL ferriesCMAL ferries use 38% less fuel than conventional vessels and emissions are reduced by a similar amount.
-
if (isSmallPicture) {
; } else if (isBigColumns) { } else { }Hybrid powertrain improves tugboat economy and maneuverabilityThe Telstar saves 20% on operating costs compared to traditional tugboats.
-
if (isSmallPicture) {
; } else if (isBigColumns) { } else { }VACON® drives power hybrid ferries 24/7Passenger ferries bridge Amsterdam’s IJ River, keeping the city connected around the clock. Hybrid propulsion powered by VACON® drives ensures 24/7 uptime, smaller generator size, better air quality, less noise and easy maneuverability of the vessels.
-
if (isSmallPicture) {
; } else if (isBigColumns) { } else { }High efficiency in hybrid bulk carrier propulsionVenturing into hybrid propulsion was a bold step for the Vranken family’s dry cargo bulk carrier business, which serves the inland waterways of the Rhine. It has paid off fast, delivering rock-bottom operating costs, thanks to an innovative diesel-electric propulsion system.
Contact us
For further information please contact us