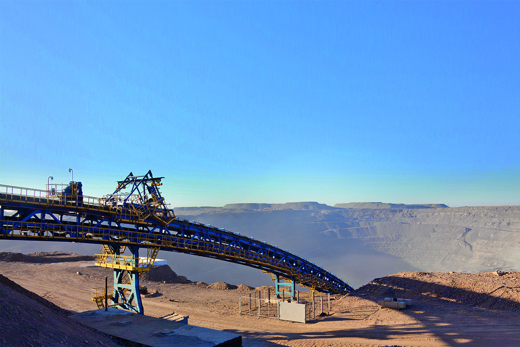
Long conveyor capability
Smoothly controlling the acceleration and deceleration of long conveyors reduces mechanical stress throughout all drive-train components and within the conveyor belt itself. This leads to longer lifetime for the belt and other drive components, increasing asset availability and lowering maintenance and operating costs. Having the flexibility to control the speed of long conveyors can help optimize the complete system, reduce bottlenecks and maximize the efficiency of a material flow process, resulting in operating cost savings.
Maximize belt life
Installing multiple motors on long conveyors is common practice. Apply drives to ensure load sharing between each motor for reliable operation and to maximize belt life. Danfoss drives include both Master-Master and Master-Follower control solutions for this. Selection of the control solution depends on the configuration of the conveyor drives on the conveyor. For example, you can mount all drives at the head end or drives at both the head and tail end.
Both approaches are easy to implement and have proven to be robust, reliable solutions for long conveyors.
Bulk handling
For downhill conveyors, continuous regenerative braking operation is typically required. Here, an Active Front End (AFE) drive or alternatively a regenerative drive panel solution, using a standard 6-pulse drive with separate regenerative module, is the best solution to feed back energy when the conveyor runs downhill.
Intelligent control of electric motors by AC drives ensures that the mine and plant can cut equipment operating costs thanks to
- Regenerative braking which recovers energy when the conveyor runs downhill
- Controlled start-up procedure
- Reduced mechanical stress for all components of the start motor and clutch
- Smooth control algorithms ensuring gentle startup, braking, and transition between full and partial load operation, to minimize wear on equipment.
Danfoss drives are used extensively on long conveyors in excess of 1-km length, which are common on bulk material applications on mine sites, processing plants and port facilities such as:
- Run-of-mine (ROM) bin feeder conveyors
- Stockyards
- Train loadout conveyors
- Pipe conveyors
- Long overland conveyors
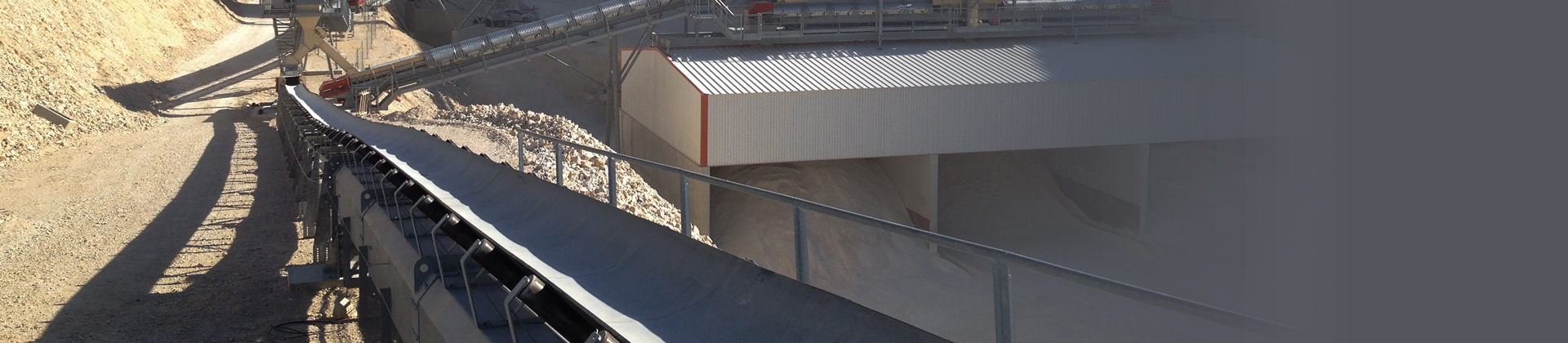
Optimal quarry conveyor performance at Italcementi quarry
Fearless of the difficult conditions, rugged VLT® drives ensure efficient production of hard limestone
Get more information
Read the Mining and minerals brochure
Read more about Energy and natural resources
Products
-
if (isSmallPicture) {
; } else if (isBigColumns) { } else { }VACON® NXP Air CooledDesigned for a broad range of demanding applications, focusing on higher power sizes and system drives.
Case studies
-
if (isSmallPicture) {
; } else if (isBigColumns) { } else { }DrivePro® services enhance security of heat supply for 49,000 apartments in GliwicePOLAND: At district heating company PEC Gliwice, AC drives reduce energy consumption of electric motors by up to 40%. DrivePro® Site Assessment audits help ensure optimal efficiency.
-
if (isSmallPicture) {
; } else if (isBigColumns) { } else { }Italcementi enjoys optimized process performance in all conditionsItalcementi chose the VLT® AutomationDrive FC 302 to ensure optimized process performance in their harsh environments.
-
if (isSmallPicture) {
; } else if (isBigColumns) { } else { }80 kW power savings at Kolomela mineBack-channel cooling in VLT® AutomationDrives reduces substation heat load enabling use of a smaller air-conditioning system with lower power consumption.
-
if (isSmallPicture) {
; } else if (isBigColumns) { } else { }Optimized production at KWB Coal Mine90 kW VLT® Drives ease the mechanical stress on the heavy equipment and improve steering when the excavator turns sideways.
-
if (isSmallPicture) {
; } else if (isBigColumns) { } else { }Minimal energy use at Shanxi Zhongxi CementVLT® Drives move a 10.5-km-long conveyor belt. Load sharing between drives transfers energy from downhill segments to the uphill parts.
Contact us
For further information please contact us