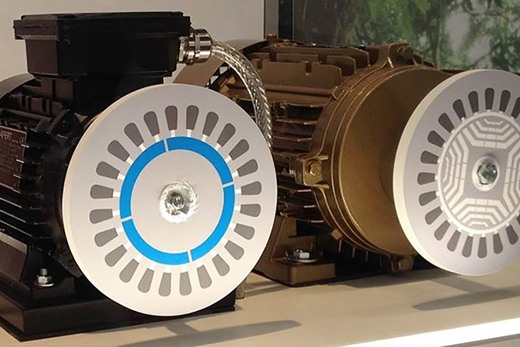
Whether we are genuinely interested in having a positive effect on the environment, or simply following the ever-intensifying standards and regulations, optimizing the energy efficiency of our motors and motor controllers is something we cannot escape.
The energy-efficiency discussion has forced the development of new motor technologies and the reinvention of existing, older technologies. In the past, the induction motor (IM) was the only type of electrical motor used in industrial applications. It is still today one of the most commonly used motors in most applications. Synchronous reluctance motor technology, first invented a century ago, was originally optimized for size and torque. Thanks to the advent of AC drives, the high-efficiency synchronous reluctance motor (SynRM) can now be optimized for energy efficiency. And then there are internal and surface-mounted permanent magnet motors. Each motor type has its advantages and drawbacks; the key is finding the one that best fits your application.
For optimal energy efficiency, we then need to take a look at the motor controller – the AC drive. We all know that AC drives reduce the electricity consumption of motors under variable torque loading (for example, with fans and pumps). In addition, AC drives can also be configured to run in regenerative mode where braking energy is fed back into the power supply instead of being lost as heat. But how do we put the energy-efficiency puzzle together? Are there any constraints on what AC drives we can use with what motors?
Is bundling the answer?
Some motor suppliers offer a bundled motor and drive solution. On paper, this may seem the most convenient, and cost-effective, option. You’re only dealing with one supplier, compatibility is ensured and spare parts stock is minimized. However, it is important to keep an eye on the total cost of operation and the total lifecycle costs.
Think about support, for example. You still need to contact one person for drive support, another for the motor, and yet another for other equipment in the chain. That’s time consuming and potentially costly.
And what about replacements or retrofits? If the motor-drive bundle has been delivered to an installation in a remote region, and the exact same motor technology or compatible drive technology is not available, you’re looking at expensive, and potentially critical, downtime in a breakdown situation.
So, to come back to the headline, let’s look at the topic of motor independence and discuss why choosing an AC drive that adapts to any motor technology makes the most sense.
Four reasons why motor independence matters
Flexibility
In this sense, flexibility means the ability to accommodate changing customer specifications and new technological trends over the entire lifetime of an application. If the drive is compatible with all state-of-the-art motor technologies, it’s just a case of including new motor algorithms into software updates of the drive when needed.
Fast replacement/retrofitting
As discussed earlier, there may be occasions when there are bottlenecks in delivery by a particular motor supplier. Similarly, it may be difficult to find an identical replacement motor, for example, in a remote site or location. In these instances, your only option might be to choose a different motor technology. Having a drive that’s compatible with all motor technologies gives you the freedom to choose another, more available, motor technology to avoid costly downtime.
One drive fits all
Now, we’re talking about multiple installations in, for example, large plants. Having the same motor-independent drives installed throughout the entire plant mean there’s a lower spare parts stock inventory, simplified staff training and more straightforward maintenance.
A future-proof solution
Using automatic motor adaptation, motor-independent drives can deliver optimal performance of any motor both now and throughout the lifetime of the application. Motor-independent drive suppliers continually test new motor technologies in order to develop new algorithms for compatibility. Independently optimized components adapt completely to a variety of applications. OEMs, for example, can therefore design the highest-performance drive/motor system for a specific niche application.
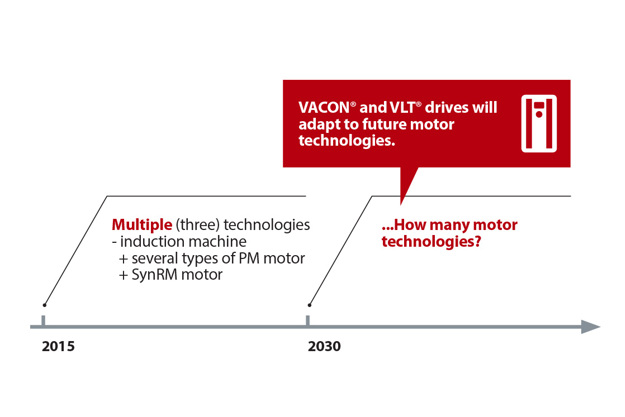
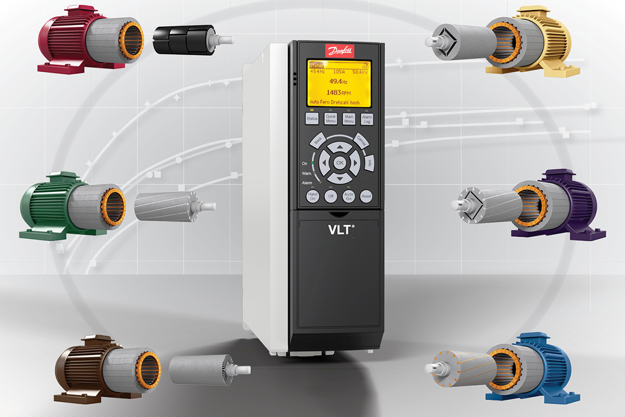