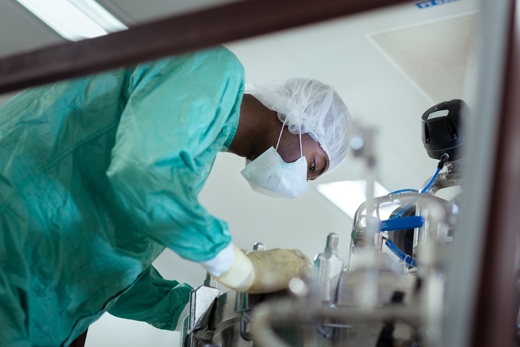
Modern Pharmaceutical companies employ technologically advanced HVAC control systems for precise temperature, humidity & dew point regulation. These HVAC controllers manage the sensitive equipment and help carry out the production processes that require specific environmental settings. It's noteworthy that the HVAC systems consume the highest fraction of the total energy consumption of any building. The importance of the HVAC system for a pharmaceutical set-up can be observed from the fact that it shares up to 60% of the total energy consumption.
HVAC units intended to be employed for use in the cleanrooms are equipped with processes like positive/negative pressure regulation, recirculation of the airflow, and alarm warnings on the slightest change in the set tolerance levels.
Methods to reduce energy consumption in the pharmaceutical industry
The following methods can be employed in the pharmaceutical set-ups to downsize the energy consumption of the HVAC systems.
Variable speed controls in high-efficiency fans
All the fans in the clean rooms should be fitted with a Variable Speed Drive (VSD). Combined with a flow transmitter, these high-efficiency fans control the flow level whenever the filter gets clogged. The minimum efficiency rating of IE4 for the motors would be an ideal choice.
Danfoss HVAC drives are known for their world-class AC to DC and DC to high/low voltage DC conversion and provide variable speed control functions for electric motors. Danfoss has the world's most advanced portfolio of VLT drives, power converters, and VACON drives readily available at your fingertips. Using these HVAC drives in your pharmaceutical establishments would surely increase energy efficiency while providing better speed controls.
Installation of advanced heat recovery systems
The pharmaceutical systems that use 100% fresh air or a substantial amount of fresh air require a good heat recovery system to be installed to extract the air. The most acceptable systems capable of sorting out this issue runs around coils for heat recovery. These heat exchanger systems call for functions where the supply airflow is completely separated from the exhaust airflow.
Danfoss has the widest range of heat exchangers consisting of micro-channel heat exchangers, micro-plate heat exchangers, semi-welded plate heat exchangers, and brazed plate heat exchangers used in refrigeration systems. The Danfoss Micro Plate Heat Exchanger (MPHE) is best suited for application in chillers, heat pumps, and dedicated control systems with a cooling capacity of up to 400 kW through single or dual circuits. Danfoss' heat exchangers have an innovative plate design that enhances the heat transfer in the condensers and evaporator. They also provide high reliability resulting in increased system efficiency with the lowest refrigerant charges.
Temperature & pressure management smart sensors
Many pharmaceutical processes are impacted by the development of Low Delta T syndrome, which is an issue in the performance of the water distribution system. This syndrome occurs when the temperature difference between the incoming and outgoing fluid is lower than the delta T of the designed coil. This issue causes over-pumping of the refrigerant, necessary for the coil energy demand, which ultimately leads to the rise in energy consumption.
One of the significant causes of this syndrome is the inappropriate balancing of the water distribution system, which requires a secondary circuit and a separated coil pump. These pumps are equipped with flow meters and temperature sensors to adjust the flow, thus maintaining a constant differential temperature.
Danfoss industrial temperature sensors have a measuring range of – 50° C to 800° C and are known for their high degree of moisture protection. These sensors are available with marine approvals, fitted with a changeable or fixed measuring insert and built-in transmitters. These sensors are best suited for the pharmaceutical processes as they radiate the least amount of heat which assists in their precise measurement and adds to their applicability for clean rooms.
Efficient cooling/heating compressor technology for the clean rooms
A requirement-based analysis of the facility's heating/cooling capacity is necessary to decide the best energy-efficient technology to be used in the pharmaceutical set-ups. The selection of the compressors, chillers, boilers, heat pumps, etc., depends on the set-up's rationale knowledge.
To enhance the cooling/heating performance of the overall system, it should be fitted with an energy-efficient compressor. Danfoss Turbocor compressors are equipped with magnetic levitation technology, which helps provide high efficiency at low sound levels, generating the least carbon footprints.
Danfoss compressors provide a sustainable and intelligent refrigeration functionality for a wide range of commercial applications like the specific requirements of pharmaceutical cleanroom temperature regulation. These compressors are compatible with lower GWP refrigerants making them suitable for different refrigerant regulations.
Conclusion
Reducing energy consumption in the different pharmaceutical HVAC systems is a challenging task due to the prevalent GMP constraints and other biological containment issues of the facility. Using the Danfoss technological solutions for HVAC control systems of your pharmaceutical set-ups, you can increase energy efficiency and reduce the carbon footprint of all your processes. Using the Danfoss technological solutions, you benefit from the best-in-class efficiency and get the assurance of Danfoss, whose legacy is based on decades of passion & experience.