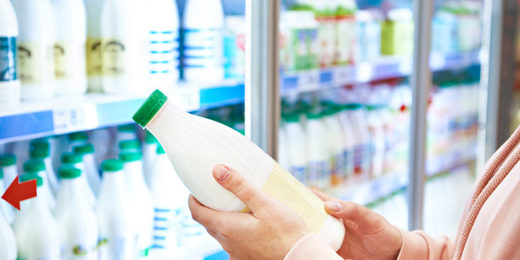
Why is precise temperature important for a dairy plant?
The dairy industry uses advanced technology that controls the refrigeration systems and guarantees strict hygiene at every step of the manufacturing process. The wide range of end-to-end products in the dairy industry, comprises processed milk, cream, ice cream, yoghurt etc. All these products require precise temperature management for extended periods.
Raw milk is stored at 4°C to 6 °C temperature in the initial processes. Further, after the filtration and pasteurization are done, the milk is stored in sterilized conditions, under precise temperature control before and after the treatment. The employed cooling media is either ammonia, ice water or CO2. The pasteurization process operates at an accurate temperature for protein denaturation, holding the milk for the required time. Hence total and precise control over temperature for a designated time becomes an essential factor for the dairy plants.
Temperature precision is essential for the pasteurization process and the effective operation of other system processes, like homogenization, deaeration, and fermentation. If the temperature is too high in the dairy processing, the deaerator’s vacuum can create an unwanted rise in heating demand, increasing the operating cost. Also, extremely high temperature in the condensers leads to excess vapor leaving the product, which intensifies the risk of product loss. On the other hand, if the incoming temperature is maintained too low, it leads to inefficiency in the system as air removal in the initial steps is affected. There are chances of foaming that can fill the deaerator vessel, disrupting the production process.
The above-discussed processes highlight the importance of an uninterrupted cold chain equipped with thermal conditioning during processing and precise temperature control during fermentation processes. Hence it’s manifested that precise temperature management is a vital factor for the dairy processing industry.
How is the shelf life of dairy products increased?
The dairy products industry has several refrigeration applications, which needs state-of-the-art technologies to attain high-quality dairy end products. The basic process includes heating at high temperatures to inactivate microorganisms, thus ensuring product safety. Pasteurization is another widely practiced process that increases the shelf life of these dairy-based products from 7 to 20 days.
The dairy refrigeration systems extensively apply a pasteurization process designated as HTST (High-temperature short-time). This includes heating at a temperature of 72°C for a standing period of 15 seconds. Under favorable dispensation and storage environments, this HTST process extends the shelf-life of dairy products up to 3 weeks based on the quality of the raw milk used. All these dairy processes require advanced refrigeration systems, safety valves, and pressure control valves, etc., where the market-leading expertise of Danfoss comes into play.
Danfoss products that help dairy plant owners maintain precise temperature:
Several dairy production services are based on stainless steel components which ensure safe and hygienic production atmospheres. Recently many producers are shifting towards CO2 as the refrigerant since it is safer and energy-efficient for daily use. The Danfoss product ranges for the dairy industry include:-
i) Valves:- The Danfoss stainless steel overflow valves (OFV-SS) provide triple functions of a stop valve, check valve, and overflow valve. With an operating pressure of up to 52 bars and a wide temperature range, the opening pressure can be easily adjusted for the required range of 2-8 bars. Danfoss range of stainless steel needle valves (SNV-SS) and EVRS and EVRST stainless steel solenoid valves provide futuristic advantages to enhance the overall system efficiency of the dairy products.
ii) Compressors for refrigeration:- Danfoss compressor in refrigeration systems for the dairy industry provide sustainable, energy-efficient, and smart refrigeration applications. The Danfoss compressor ranges help maintain the required temperature throughout the system processes. These refrigeration compressors work seamlessly with lower GWP refrigerants, which help comply with refrigerant regulations.
Danfoss compressors sport a compact design, making them seamless to use and ideal for small spaces. Danfoss compressors function quietly, creating a noise friendly working environment. Danfoss’ compressor in refrigeration system are equipped with excellent thermal load management features, which makes them flexible and restricts the development of intense heat loads without degrading the performance.
iii) Drives: Danfoss refrigeration drives help modulate the speed of conveyors and precise motion control (like ice cream conveyors) to help regulate the control process like agitators, condensers, and pumps. Danfoss drives function to assist in capacity modulation under varying loads using which you can target to save energy up to 30-40% while dropping the drift losses due to makeup water.
· Capacity Modulation as per Load Requirements
· Energy savings are typically in the range of 5%-15%
· Precise System control & Automation
· Motor Safety & Process Interlocks
In conclusion
Danfoss’s range of technologies for cooling and refrigeration applications assist dairy producers in delivering efficient, reliable, and environmentally friendly refrigeration systems to the global dairy industry. Danfoss products ensure safety while delivering hygienic and precise temperature-controlled products to dairy manufacturers. Innovation has been the main focus at Danfoss, due to which we provide the latest technologies in refrigeration systems. With our 80+ years of experience in the global refrigeration business, our product ranges signify cutting-edge and environmentally friendly dairy product-based installations.
All Danfoss products use a modular design system to enhance their functionality for a wide range of structures. These power-packed features enable Danfoss products to deliver low life cycle costs and other energy-saving benefits. To know more about our products, write to us at danfoss.india@danfoss.com