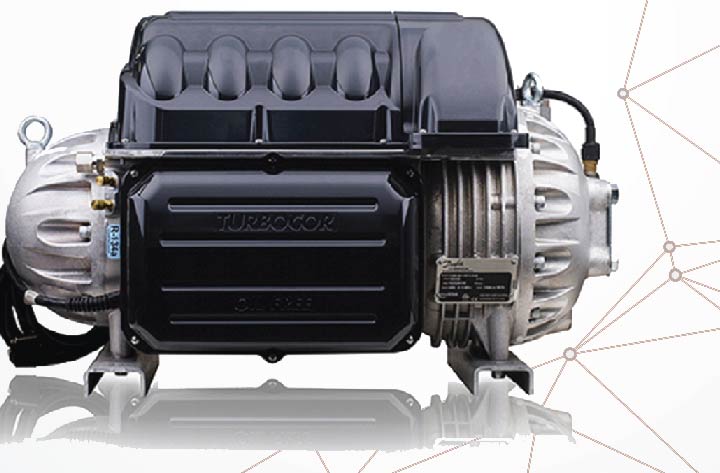
Turbocor compressors are recognized across the globe for their compactness, low noise, and energy performance. However, what helps the Turbocor stand out is, its oil-free technology that brings unmatched benefits in terms of efficiency, low maintenance, and long-lasting energy performance. With climate change as a real looming threat and changing environmental regulations, novel technology such as the Turbocor is not a matter of convenience, but a necessity. As more government bodies and builders explore the concept of sustainable smart cities that produce reduced or zero waste, the oil-free chillers fit perfectly into the vision for the future.
The Turbocor offers 6 major advantages over the conventional chillers:
Oil-Free Performance Advantage: Oil-Free, magnetic bearing compressor technology eliminates complex oil and refrigerant lubrication management systems resulting in a simplified chiller design, increased reliability, and reduced maintenance. Consistently increasing complications in traditional chillers regarding maintaining oil pressure, oil separators, etc. are entirely eliminated. Moreover, by ensuring the makeup water used is free from hardness, the insulation is intact, the flow of water is optimum, and refrigerant charge is maintained with the performance advantage maximized.
Zero Performance Degradation: In conventional chillers, over time a layer of oil forms over the heat exchanger tubes, which degrades the performance & efficiency of the chiller. The cutting-edge, oil-free design of Turbocor eliminates the need for an oil management system and thus avoiding the performance and efficiency drop that are usually caused by oil degradation in conventional chillers. Also, it eliminates the drop in performance due to mechanical wear between the screws.
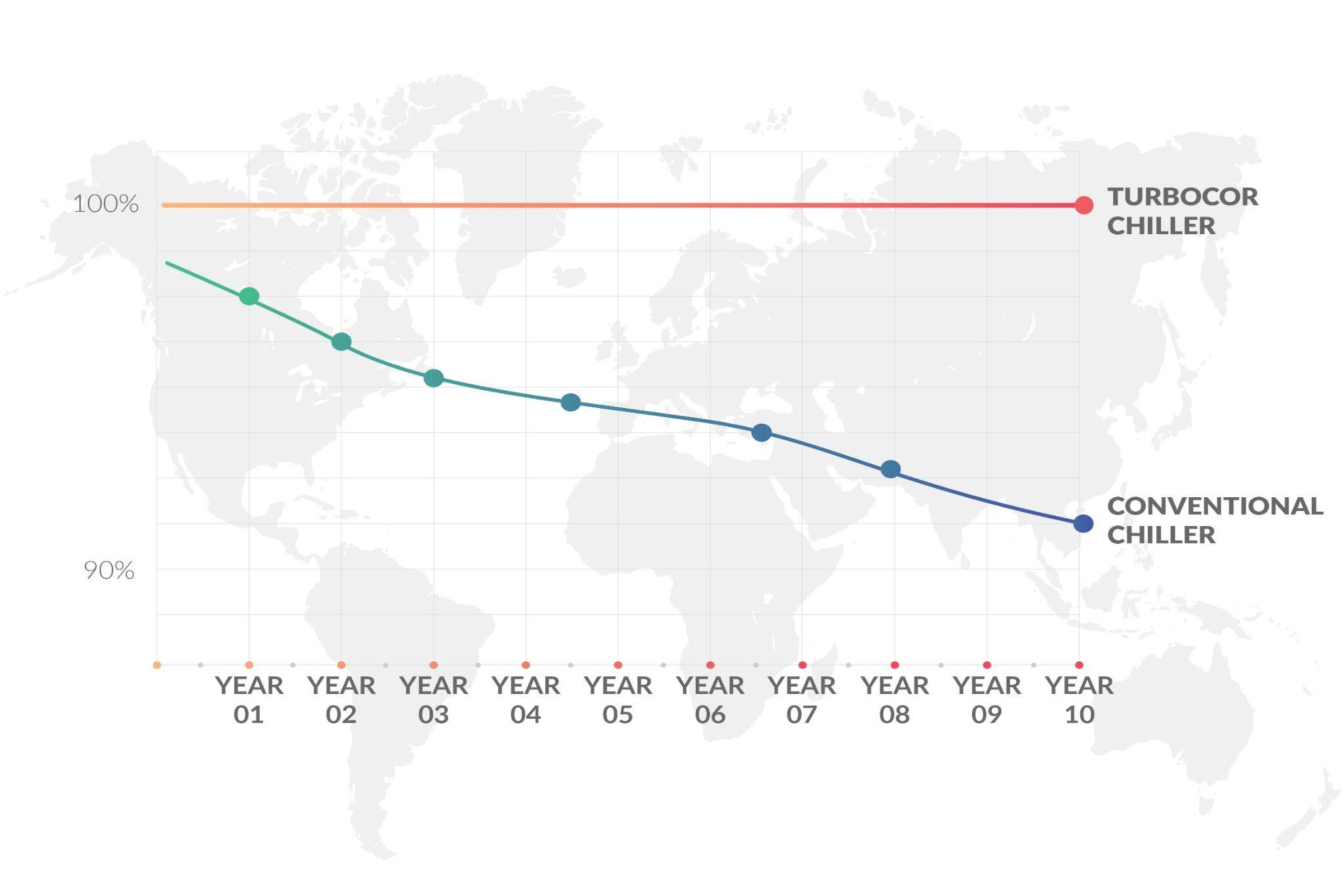
Energy Efficient: Turbocor compressor - the world’s first oil-free magnetic bearing compressor, is 35% more energy efficient than the traditional chiller. Often, buildings experience internal and external loads that vary within a day leading to changing demands of efficiency from the chillers. Consequently, buildings with fixed speed systems are wasting energy when the loads fall below 90%. Turbocor’s Variable Frequency Drive optimizes the speed from as low as 20%, all the way up to 100%. With permanent magnet motors and variable speed drives that provide unmatched full and part load efficiency & an intuitive system that can seamlessly adapt to varying demands in both air and water-based chillers, energy efficiency is always optimum. Additionally, taking into account the extreme current draw a conventional compressor starts with, causing stress and wear on mechanical and electrical components, Turbocor’s magnetic bearing compressor that starts with just 2 amps of current translates to lower investment in electrical infrastructure, lower stress on the electrical system while providing a longer compressor life.
Environment-friendly: Climate change is real, and HVAC systems are expected to be stipulated as per current and future regulations demand to meet energy and performance efficiency. Danfoss uses low GWP refrigerants to help slow the process of global warming. Danfoss Turbocor compressors are available with environmentally friendly and future ready R134a and low GWP, A1 non-flammable R513A, R515B, and ultra-low GWP HFO1234ze. Making the transition extremely smooth while contributing to meeting city and state emission goals.
Quiet: Users of the technology have assured the vibration is reduced to a minimum and it is often hard to recognize a working chiller from the ones that are turned off. The low sound levels reduce customer complaints in noise-sensitive areas (such as hospitals) and reduce the cost of expensive sound treatment typically required of noisy screw compressors. The sound pressure levels are as low as 70.0 dBA at 1.5m (5ft), resulting in up to 8 dBA lower than a typical screw compressor.
Reduced Maintenance: A chiller using oil-free technology has fewer mechanical parts and a simpler design since all the components associated with the oil management system are eliminated. This results in reduced maintenance and higher reliability over the life of the chiller. Tedious processes such as oil changes, maintaining oil pressure, managing oil separators, etc. are completely eliminated. Additionally, Turbocor requires zero maintenance on the drive train. Roughly ₹1,50,000 worth of annual maintenance is eliminated by adopting the oil-free Turbocor technology.
With the industry leading energy efficiency, oil-free technology, environmentally responsible mechanization, and minimized need for replacement of machinery, Turbocor’s range of products are the ideal technology for chiller applications while simultaneously being supportive towards the ongoing efforts to oppose contribution to global warming. The decreased carbon footprint combined with the increased efficiency, make Turbocor technology the best contribution to a responsible future.
Turbocor enabled many other organizations through its advanced magnetic levitation technology that has put it at the top of the world in the field of oil-free compressors. It engineers technologies for the futuristic world to do more with less. The Turbocor technology prides itself at being economically, and environmentally sustainable while managing to prioritize the users’ ease.