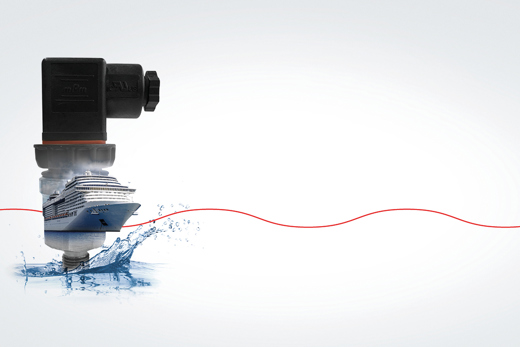
Marine-industry cleaning systems like exhaust-gas scrubbers and ballast water treatment systems have been adopted to meet the IMO’s environmental legislation and restrictions. However, the processes in these systems – which use seawater as the primary cleaning agent
to wash out sulfur particles from exhaust gas or to produce bacteria eliminating disinfectant in ballast water – create highly corrosive environments that pose a challenge to critical components.
Exhaust gas scrubbers utilize seawater spray to precipitate harmful carbon and sulphur particles before the clean exhaust gas is emitted into the atmosphere. The effluent from the scrubbing process accumulates harmful substances and is, therefore, an aggressive combination of carbon particles and sulphuric acid diluted in saline water – which has the potential to corrode any surface the comes into contact with the fluid.
Similarly, the seawater used in the electrolysis process of ballast treatment systems to produce disinfecting chlorine accumulates hydrochloric acid – a highly aggressive agent against metal surfaces in combination with sodium chloride.
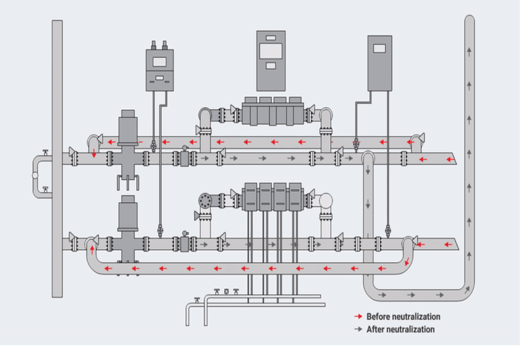
Ballast water treatment system using electro chlorination
The speed and severity of corrosion in exhaust-gas scrubbers and ballast water treatment systems depend on temperature and the concentration of aggressive media – which means all components within the systems must be robust, reliable, corrosion-resistant solutions.
Sulfuric and hydrochloric acids accelerate the deterioration of metal surfaces exposed to the saline solution, placing huge demands on the materials used in the pump systems. And it’s not an easy challenge to overcome: even commonly used AISI 316 stainless steel has its
shortcomings as a material for pressure transmitters when faced with acidic conditions.
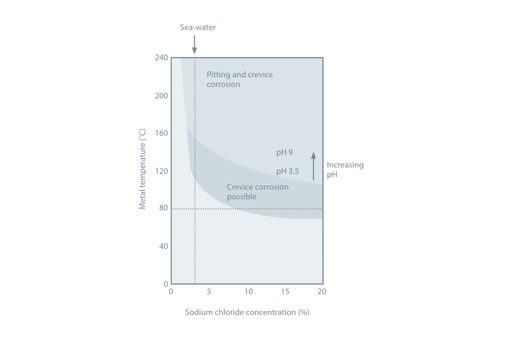
Titanium corrosion pattern when exposed to sea water
However, following decades of frontline expertise in harsh marine environments and innovative engineering, the DST P40M pressure transmitter offers best-in-market performance in monitoring marine applications, such as ballast-water treatment, exhaust gas scrubbers,
desalination, and seawater cooling – systems that demand high corrosion resistance and longevity to ensure the continued operation of auxiliary and propulsion systems onboard a vessel.
While most metals are subject to increased corrosion in the crevices formed between themselves and other metals, titanium is exceptionally resistant to this type of corrosion at temperatures as high as 80°C.
So, the DST P40M pressure-transmitter housing has been engineered from a single bar of titanium, eliminating any structural weaknesses that would be caused by welding or brazing. This is because the temper and grain structure of the welded metal is altered under high temperature – leading to material amalgamations that reduce the metal’s inherent corrosion protection.
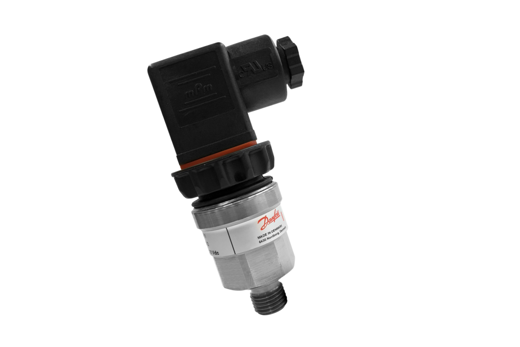
A titanium powerhouse - Reliable performance in the toughest marine environments
In the DST P40M, state-of-the-art weldless titanium housing provides exceptional material properties such as high corrosion resistance, low density, and high tensile strength, offering best-in-market protection from a broad range of acids, alkalis, and aggressive pollutants in numerous chemical-processing and marine applications.
The pressure sensing element is made from ceramic Al2O3 96% – a material with excellent chemical immunity against corrosive media. Plus, the pressure transmitter follows the piezoresistive principles and features a Wheatstone bridge screen printed onto the ceramic diaphragm with Thick Film technology. And, as titanium is a more noble material than stainless steel, it means the P40M can be used alongside stainless steel without initiating galvanization and corrosion.
These properties combined – along with having all the required international marine approvals – means the DST P40M is the ultimate corrosion-resistant, high-performance pressure transmitter for intense marine applications.