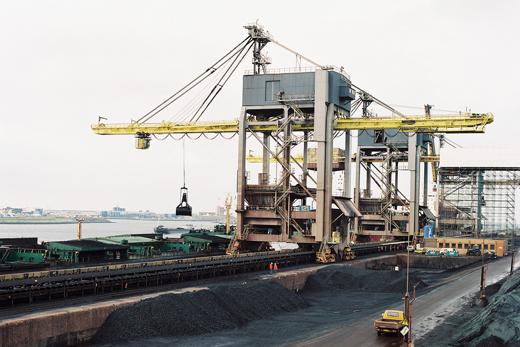
Liquid-cooled VACON® active front-end drives control Tata Steel grabber crane
Time is money, and the downtime of cranes is loads of money. If a ship is not unloaded in time, penalties are to be paid. Therefore, a reliable operation of AC drives that control the crane plays a major role.
Within the city limits of Heemskerk, Beverwijk and Velsen in the Netherlands, three massive grabber cranes raise their heads high in the sky. These cranes with a total capacity of 40 tons each unload ships that transport coal and iron ore for Tata Steel (previously Corus) at its plant in IJmuiden.
Reducing expensive downtime
These cranes form the backbone of the Ijmuiden plant, and the need for refurbishing old drives dating from 1968 became evident. Since December 2006, VACON® liquid-cooled active front-end drives have been controlling the hoist and trolley travel of one of the cranes, with reliable and trouble-free operation.
Compact drives and high protection class
Liquid-cooled VACON® AC drives are very compact as the power section is specially designed for liquid cooling and no air channels are required. The compact size was the main reason why they were chosen for the task. The space savings compared to just the power module of a similarly rated air-cooled drive can be up to 70%.
Another essential reason was that liquid cooling enables the use of cabinets with a high protection class. The AFE filters are also liquid-cooled. The physical size of the Vacon solution in the electrical room allowed considerable space-saving benefits to be achieved, and were therefore highly appreciated.
Additional factor that contributed to the choice of liquid-cooled VACON® AC drives was their heat loss transportation. The crane is located in the middle of the coal and iron ore storage fields, where the air is filled with coal and iron air dust. Liquid-cooled drives made it possible to transport the heat losses outside the electrical room without ventilating the room and cabinets with the dust-filled air.
Feeding energy back to the mains
The AC drives are equipped with active front-end units to feed the regenerative energy back to the mains. VACON® AFE drives also generated a minimum level of harmonics and made it easy to meet the harmonic specifications without the use of dedicated, large 12-pulse transformers.
GTI Electroproject as system integrator
GTI Electroproject was appointed as system integrator and was responsible for designing and commissioning the drive system including the water cooling system and grabber control.
Acceleration and deceleration of the trolley travel makes the grabber of the crane swing. As unloading cycle times should be as short as possible, the crane driver has to cope with the swinging grabber. Here, the way the AC drives respond to changes in the position of the joysticks plays a major role.
At the Tata Steel plant in IJmuiden, all crane drivers work with three unloading cranes. Therefore, the response of the refurbished crane should be equal to the response of the cranes not yet refurbished. By using a very sophisticated speed controller and freely programmable torque-to-speed characteristics of the AC drives, GTI Electroproject attained equal responses that fully satisfied the crane drivers.
“As a system integrator, we are very pleased with the programming capabilities of VACON® AC drives. This applies not only to cranes but also to heating, ventilation and air-conditioning as well as to other industries where we are active,” says Mr Jan van Gurp, Managing Director, GTI Electroproject.
The cooling water is supplied by a Donaldson Ultrafilter chiller that produces cooling water with a constant temperature of 30 ºC.
Scope of supply:
- Hoist: 2 x 820-kW active front-end (AFE) liquid-cooled AC drives
- Trolley travel: 1 x 485-kW active front-end liquid-cooled AC drives
- Water chiller
Please note that Vacon joined the Danfoss Group in December 2014.
Get more information
Read more about Drives for industrial crane and hoist movement
Read more about VACON® NXP Liquid Cooled