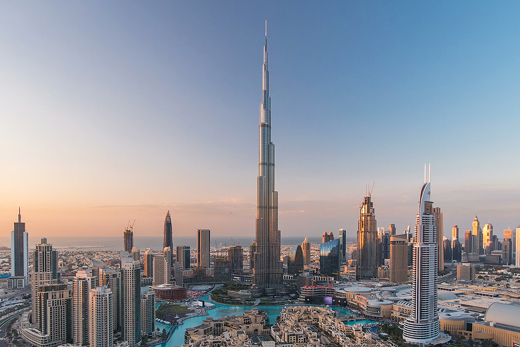
Try to imagine a building with a height of more than 800 metres. It is difficult. However this is reality for Burj Khalifa (originally Burj Dubai), the tallest building in the world, in Dubai, United Arab Emirates. The 5600 workers on the project placed a high value on construction hoists that were safe and reliable. The 12 Pega Hoist construction hoists on the site were controlled by VACON® AC drives.
Pega Hoist, a Czech company specializing in construction rack and pinion hoists, played a vital role in erecting the building. An undisputed fact is that with a height of 828 metres, Burj Khalifa towers above the tallest buildings in the world: the Taipei 101 in Taiwan, the Petronas Towers in Kuala Lumpur, and the CN Tower in Toronto.
Pavel Policar, Pega’s Industrial Hoist Director and Manager of the Burj Khalifa project, hasn’t experienced a better challenge in the field of construction hoist production than the world’s tallest man-made structure.
Demanding conditions
Almost three years non-stop operation in severe local climate conditions placed extreme demands upon the equipment. “Temperatures reaching 53 degrees centigrade, very high humidity, sand storms and fine salt film pollution. On top of this, we needed to manage the challenge of unlimited transportation of men and materials and traffic peaks,” says Mr Policar.
The company is no novice in its field. Pega Hoist has delivered dozens of construction elevators to the United Arab Emirates and to neighbouring Saudi Arabia operating at heights up to 200 and 300 metres. Thanks to their advanced technology and technical solutions, the performance of the Pega construction hoists has been unbeatable. This convinced those behind the Burj Khalifa project to contract Pega Hoist.
Large and small jump hoist solutions
The hoist solution eventually chosen for the Burj Khalifa project was a combination of large static hoists and smaller ‘jump’ hoists which rise with the building to service the busiest areas. “The concept was four twin hoists (eight cages) on the main building to a height of approximately 420 metres in one go,” says Mr Policar. “We supplied super-fast, no-counterweight 3240 variable frequency-controlled hoists with a capacity of 3.2 tonnes and a four metre cage running at 100 metres per minute, full load.” He says that this 420 metres’ run is the longest ever single ride by a temporary construction hoist.
Other “fixed” hoists were installed at a level of around 420 metres; these were two twin units of the same type operating up to a level of 560 metres and 600 metres respectively. The final 110 metres of the tower was reached by a single twin-cage unit.
In addition to these fixed hoists, Pega Hoist supplied three single-cage ‘jump’ hoists – a mix of 1 ton and 2 ton units with 2.4 metre cage lengths – which service a height of 90-120 metres and generally covered the section of the tower which was the busiest, providing inter-floor transport. “When the building significantly ‘outgrew’ the jump hoist, the hoist was dismounted and transported another 80-120 metres higher,” explains Mr Policar.
Pega’s sophisticated floor call and information control system gave workers the ability to see where the hoists were located, the direction they were travelling in, and where hoist requests were made.
Cooperation with Vacon started in 2004
Pega’s great achievements make the company the innovation engine of the rack and pinion hoist industry. Whatever parts Pega needs for its hoists, the corporate philosophy is to accept only the best products and suppliers in the world.
Pega came into contact with Danfoss Drives (then Vacon) in 2004 when making conceptual designs for the Burj Khalifa construction hoists. The first contact soon led to a joint project in product and software development, and after several months of close cooperation, the hoists controlled by Vacon AC drives were ready to be delivered to the Burj Khalifa site.
Please note that Vacon joined the Danfoss Group in December 2014.
Get more information
Read more about Drives for industrial crane and hoist movement