Agri-Norcold is a major player in the Danish cold storage market, providing flash freezing, handling, and storage services for a wide range of customers in Denmark’s food industry. With a total of one million cubic meters of refrigerated space countrywide, the reliability and efficiency of Agri-Norcold’s refrigeration systems are critical. The company recently replaced its old air purger in one of its cold storage facilities with a new Danfoss IPS 8, which is now providing better air separation and system diagnostics.
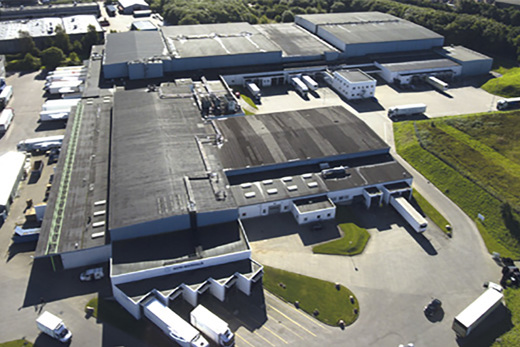
The challenge: Purge air from a large refrigeration system as effectively as possible – and get better insight into system diagnostics
Agri-Norcold is an innovative cold storage provider that is open to trying new technology and processes. As an ISO 50001 certified company, managers have clear goals to make operations as energy-efficient, reliable, and environmentally friendly as possible.
When one of its plants, located in Kolding, Denmark, needed to replace its outdated air purger, managers were eager to investigate what was new on the market.
Agri-Norcold managers were interested in finding something that purged more efficiently but also wanted to get better diagnostic data on its refrigeration system than the old system could provide.
The solution: The new Danfoss IPS 8 air purging system
Discussions with Danfoss engineers led to the installation of the new IPS 8 from Danfoss. The result of an R&D project that set out to create an intelligent air purger, the IPS 8 maximizes system performance by continuously monitoring and automatically adjusting to pressure differences between system refrigerant and purger refrigerant. A small, self-contained unit that functions independently from the main refrigeration plant, it is easy to install.
The IPS 8 performs very precise electronic purging, which reduces the risk of unnecessary refrigerant release to the environment. Importantly, the new purger also as an excellent operation log that takes it simple to monitor and easy to understand past purging cycle. This, in turn, provides better diagnostic information on refrigeration systems than traditional purgers.
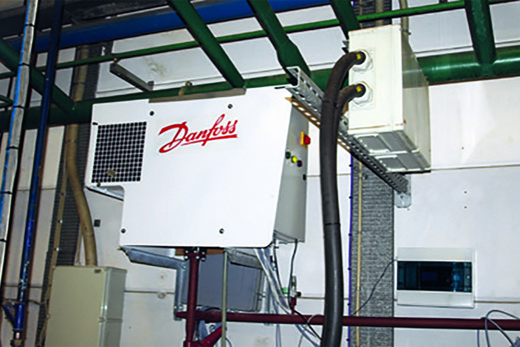
The results: Plug-and-play installation, better separation – and improved diagnostic insights
As a stand-alone unit with few connections, the installation was straightforward and completed in just five hours, including all welding.
After several months of operation, results of the new purger are clear. The IPS 8 delivers significantly better air/ammonia separation than its predecessor because it operates at a
lower temperature, resulting in far less ammonia in the purged gas. According to Henrik Straarup, team leader at Agri-Norcold’s plant in Kolding, Denmark, the smell of ammonia in the machine room has been dramatically reduced with the new system.
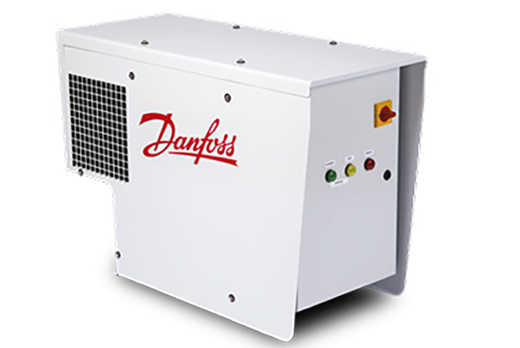
The smell of ammonia in the machine room has been dramatically reduced with the new system.
Straarup also notes that the new IPS 8 gives far better diagnostic data than the plant’s previous purger. “Unlike our old purger, the IPS 8 purges are directly related to the amount of air in the system. This lets us know, much more precisely than previously, if and when air enters the system, how much air enters, and when the air has been purged,” explains Straarup. “Such diagnostic information enables us to calculate better how many liters of air are purged and the size of any leaks.”
Plant information
Capacity | High pressure: 1,782 kW Low pressure: 2,075 kW |
Refrigerant | Ammonia (NH3) 25 tons |
Evaporators | 28 in freezer rooms, 38 in freezer tunnels 100-150 kW |
Temperature range |
Blast tunnels: -35°C Storage: -22°C |
For more product information
-
if (isSmallPicture) {
; } else if (isBigColumns) { } else { }Intelligent purging system for industrial refrigerationWith its compact design and automatic purging functionality, the Danfoss intelligent purger system helps improve the operational safety, efficiency and cost-effectiveness of industrial refrigeration systems.