Generally speaking when it comes to refrigerants, chillers are divided into two categories: low/medium (L/M) and medium/high (M/H) pressure. L/M pressure chillers can benefit from the use of pure HFOs (R1233zd and R1234ze), resulting in a GWP close to zero. The flammability penalty is very low and manageable, especially for systems installed outdoors or in machine rooms. We can expect that for the short-to-medium term, this type of systems will adopt ultra-low GWP refrigerants. The upper GWP limit, for large L/M chillers, could reach 630, which corresponds to the GWP of HFO blend R513A, listed by the EPA-SNAP regulation of July 2015 while R134a will be delisted starting in 2024.
For M/H pressure chillers, the medium GWP alternatives are in the 125-750 GWP range but users must be willing to accept an A2L flammability classification. This, again, should be acceptable for systems installed outdoors or in machine rooms. The market will likely move to GWP alternatives which offer the best trade-off between system costs and performance. We foresee that the choice will fall to high density/high pressure refrigerants with a GWP around 500-750.
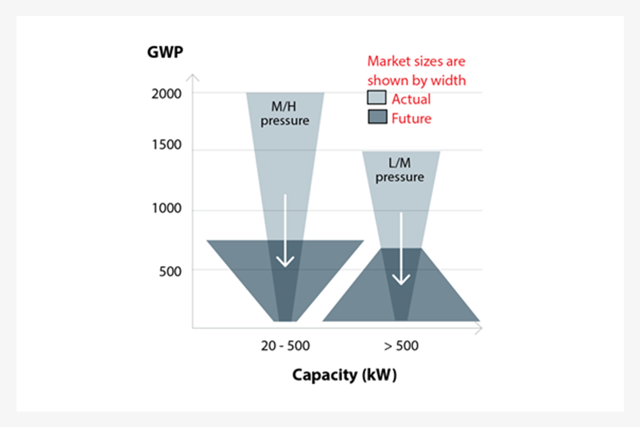
VRF systems use relatively large amounts of refrigerant per unit compared to ducted systems due to their decentralized evaporators and subsequent piping. Minimizing piping size requires medium to high density refrigerants where the only alternatives to R410A are A2L refrigerants like R32 or DR55.
The use of A2L refrigerants is closely connected to safety standards like EN378 and ISO5149, where the allowable amount of A2L refrigerant has been increased considerably in the latest editions. The ASHRAE15 working group is also looking into the future need of low GWP refrigerants. However, while these safety standards are a must, they are not sufficient on their own. Many local fire regulations have been serious barriers towards the using of A2L refrigerants. Innovative, alternative fluids for circulation are under constant development—water is an obvious choice for circulation and even CO2 has been proposed. The recent HFC phasedown under the Montreal Protocol has put pressure on revealing opportunities and risks associated with using A2L refrigerants. The coming years will likely show a more clear direction on the refrigerants choice for VRF systems.
From a glance, Industrial Refrigeration (IR) seems to be an easy sector regarding low GWP refrigerants, but we still see potential pitfalls as well as room for innovation. NH3 (ammonia) has been the preferred refrigerant in IR due to its excellent efficiency and it continues to be used as demands for sustainable refrigerants increase. However, safety concerns may potentially limit the success of NH3 as it is toxic; there have been some severe accidents in the last decade, which taught us, an industry, some important lessons such as avoiding large charges and carefully planning the location of larger plants. This has led IR to find new, innovative ways to reduce charge sizes. One way to decrease charge size while increasing efficiency is to combine NH3 with CO2: CO2 takes on the role of thermal carrier and is circulated inside the larger storage facilities.
Commercial Refrigeration and Food Retail applications are very diverse regarding systems types and refrigerants used. It includes cold rooms, glass door merchandizers, and display and islands cabinets, either in centralized or plug-ins – hermetic or autonomous cooling circuits with condensing units.
Commercial Refrigeration and Food Retail applications are grouped into three main categories.
Hermetically sealed applications are suited for using low GWP refrigerants, which are safe due to their low charge amounts. Many of these systems already use hydrocarbons like R600a and R290 and the EU phasedown has required GWP values below 150 since 2016.
Condensing units have a refrigerant charge that is typically between 5 and 20 kg and safety on flammability is imperative as many of these systems can be accessed by the public.
High GWP refrigerants like R404A have been used for many years, but new alternative, A1-classified HFCs have a GWP of less than 60% of R404A. Nevertheless, the impact of higher compressor discharge temperatures on the operating envelope and the impact of refrigerant glide on cooling performance present new challenges. We believe that the market will quickly move to an average GWP level of around 150 before slowly seeking for more, lower solutions like CO2, R290 (Hydrocarbons), or HFO blends.
Centralized DX systems are by far the highest refrigerant-consuming application due to their large charge sizes and high leakage rates. In the EU phasedown, they are estimated to use more than 40% of the baseline amount of refrigerant recommended by the phasedown. During the last ten years, CO2 has become a viable refrigerant and can be used in different system setups:
Transcritical systems where CO2 is used in all circuits (MT and LT). CO2 transcritical systems have also been driving the development of integrated heating and cooling systems, linking the refrigerant choice to the type of system.
Indirect systems where a chiller-like rack using HFCs, HCs, or NH3 cools the CO2 in a receiver, which is then circulated in the MT circuit, cooling the MT circuit. LT is also covered by CO2 and condenses either directly to the chiller on top or the CO2 MT circuit.
Cascade systems where CO2 is used only in the LT circuit and cascaded into the MT circuit which uses HFC. This type of system still uses around 80% of the HFC refrigerant used in a conventional system
Geographical location affects the energy efficiency of any system due to outdoor ambient temperature. Transcritical CO2 systems have been known to be extraordinary sensitive to outdoor temperatures. However, the latest developments with injection technologies have seriously increased CO2 system efficiency even in very warm climates and we expect it to see a market breakthrough during the next years.
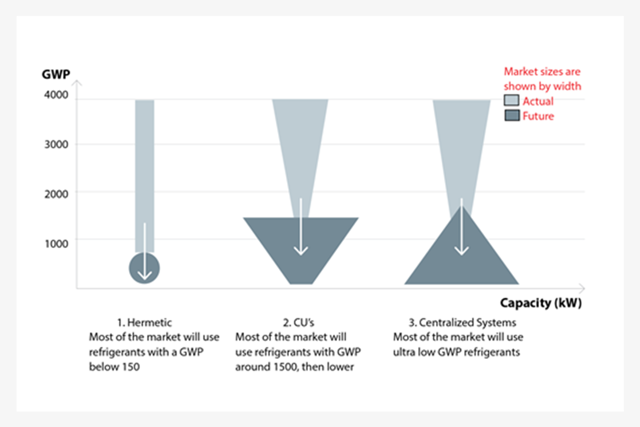
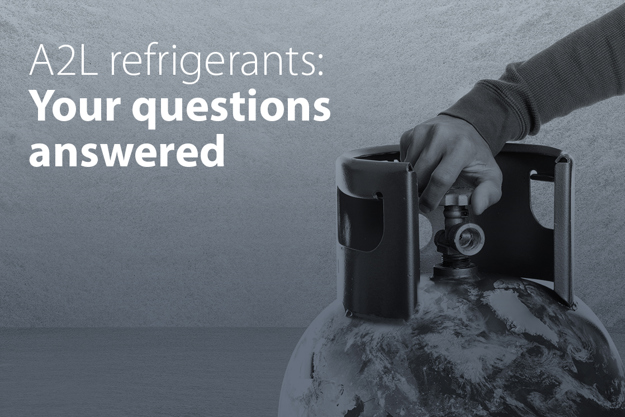
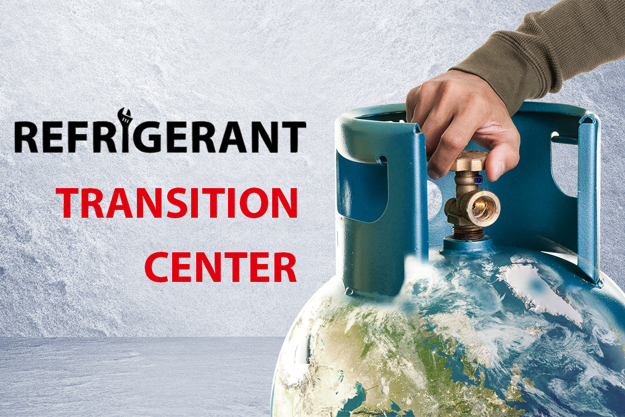
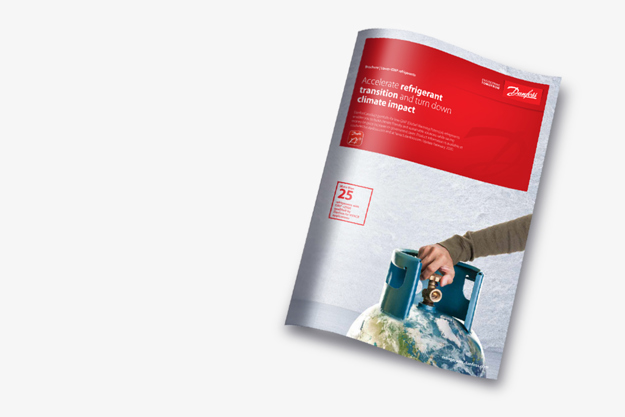
More about refrigerants
- Main refrigerants at play
- Natural refrigerants
- HFC replacements