Transitioning to liquid low-carbon fuels is an important part of the CO2 decarbonization journey. Many of these fuels, which are created from different types of raw materials, are already available and will contribute significantly to climate protection together with modern oil-fired condensing boilers. Until now, the challenge has been getting biofuels to the boiler. With the release of our Bio30 pump last year, for the burner components industry, we played part with our portfolio of solutions, helping customers to decarbonize and lower the heating emissions.
This year, we have taken up the next step in developing further our Bio product portfolio, by making its pumps and nozzles 100% biofuel ready, so we can meet your exact needs
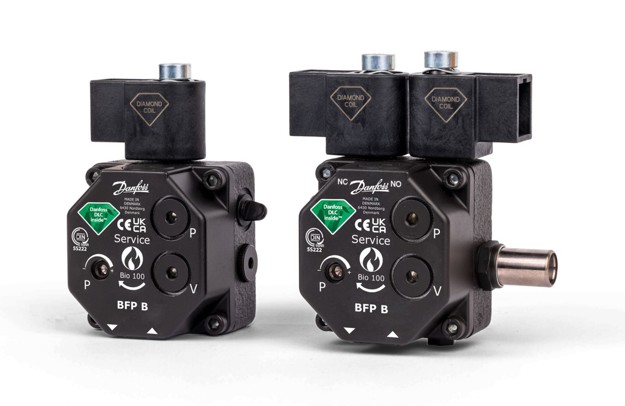

Solving the corrosion challenge
Traditional pumps contain copper or copper-containing metals, for example brass. Independent research has shown that contact between parts made of brass and biofuels should be avoided. When biofuel contacts this type of nonferrous metal, it oxidises and polymerises. The fuel’s acid content increases and it becomes more corrosive. The fuel will then react with these metal parts in the pump, which can adversely impact pump performance, cause leakage, or lead to the safety function (e.g., solenoid valve) failing.
Additionally, the combination of copper-containing parts and higher temperatures harms the biofuels, because of the internal circulation process. The fluid passes these parts several times, thereby reducing the biofuel’s stability and causing the fuel to degrade. To prevent this from happening, manufacturers would have to replace the parts yearly or every second year.
Corrosion of a solenoid valve by using a Bio30 fuel with brass material
Ina Corneliussen, Product Manager, Burner Components, explains how the new biofuel ready pumps address this challenge. “We have been working with biofuels for over 15 years, and we have always prioritised safety. That’s one of the reasons we’ve changed the brass components in our Bio100 pumps to make sure all product components are biofuel compatible. And our well-known mechanical shaft sealing secures the highest quality and helps eliminate the risk of oil leakage and product malfunction.”
TUV and UL certification to work with biofuels
Danfoss has conducted extensive in-house and field testing to develop our bio product portfolio, working closely with customers and independent competence centers to ensure the components’ compatibility with biofuels. After successful product testing, we acquired a TUV certification for Bio 30 pump back in 2021. “ Some of the largest OEMs are already using our Bio30 pumps and have approved them for their applications, and we can see that more of our existing customers are interested in switching to Bio30 pumps or even higher content of biofuels. France changed its regulations to only install Bio30 ready products in their boilers since July 1st 2022, but they are already planning to increase to much higher content and we are ready for that.”, comments Stefan Spornberger, Senior Application and Development Manager, Burner Components. “We’re pleased to support our customers decarbonization efforts by providing them with best-in-class solutions for transitioning to carbon-neutral energy sources.”
Nozzles ready for the HVO market
The expanded portfolio of bio products also includes HVO nozzles, which have been adjusted and are now fully compatible for 100% biofuel use. These nozzles are designed for domestic oil burners in the UK and enable them to use hydrotreated vegetable oil (HVO) derived from used cooking oil or non-food vegetable oils.
Removing barriers to the net zero transition
By developing 100% biofuel ready components, Danfoss aims to support the transition to low-carbon liquid fuels. “Over the past 75 years, Danfoss has built a reputation within the industry for designing and manufacturing high-quality, reliable products. And our customers can expect that same standard from our new line of bio products,” says Ina Corneliussen.
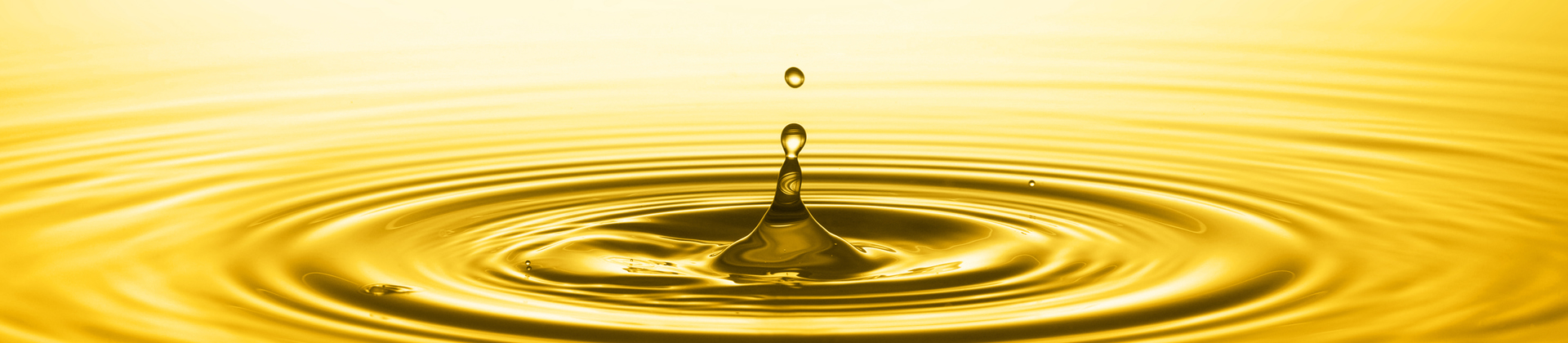