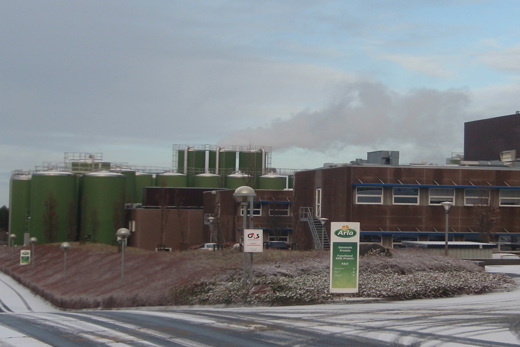
Energieeffiziente Proteinproduktion in der Arla Food Ingredients Group
Die energieintensive Produktion von Molkepulver bei der Arla Food Ingredients-Gruppe P/S in Videbæk, Dänemark, wurde durch die Verwendung von Danfoss VLT®-Antrieben optimiert. Sie sparen Energie, Zeit für die Projektierung und sorgen dafür, dass hunderte von Motoren effizienter laufen und länger halten.
Um verschiedene Produkte in der Molkepulverproduktionsstätte der Arla Food Ingredients Group in Videbæk zu trennen, sind für die Prozesse Hunderte von Pumpen, Ventilatoren, Verdampfern, Filtrationseinheiten und Sprühtrocknern erforderlich. Dies ist ein sehr energieintensiver Prozess. Um Energie und Geld zu sparen, hat Arla ein Konzept für die Motorinstallation gewählt, das VLT®-Antriebe von Danfoss umfasst.
Anstatt neue Schaltschränke für Motorstarter zu entwerfen und zu bauen, werden die VLT®-Antriebe (VLT® AutomationDrive FC 302 IP20) in den Schalträumen installiert. „Die Antriebe sind an jeden Motor angeschlossen - neue und vorhandene - und die Motoren profitieren von allen Funktionen der Antriebe. Die Antriebssysteme sind mit einem computergesteuerten Leitsystem verbunden, sodass die Mitarbeiter von Arla alles vom Computerbildschirm aus steuern können. Das war mit dem alten System nicht möglich. Wir integrieren zur Kommunikation immer eine Profibus-Karte innerhalb des VLT® AutomationDrive, wodurch wir auf die Prozessdaten und Informationen der Antriebe zugreifen können. Dies ist ein großer Vorteil “, sagt Knud Rahbek, Wartungsleiter bei Arla Food Ingredients.
Mit einem Mehrzweckantrieb wie dem VLT® AutomationDrive, der Oberschwingungsfilter und EMV-Filter für 150-Meter-Motorkabellälnge enthält, können alle Anwendungen mit einem einzigen VLT®-Antriebstyp bedient werden, und alle Motoren können über die zentrale Steuerung angesprochen werden.
Laut Knud Rahbek nutzt das Werk dieses Konzept auch bei Modernisierungsprojekten. „Wir werfen einfach die alten Schaltschränke raus und bauen die neue Installation mit VLT®-Antrieben in Verbindung mit Verteilern auf.“
Einsparungen bei neuen Antrieben
Vor der Installation von VLT®-Antrieben verfügte das Werk über viele Motoren mit DOL-Startern. Das bedeutete weniger Flexibilität bei der Drehzahlregelung, mehr mechanische Wartung der Motoren und weniger Motor- und Anlagensteuerung. Zudem erhielten sie ohne die Profibus-Kommunikation weniger Informationen von Motor und Anlage. Gleichzeitig beanspruchte die bisherige Lösung viel Platz im Schaltschrank. „Die Schaltschränke sind jetzt nur für den Vertrieb vorgesehen, einschließlich Sicherungen oder Trennschaltern. Dies ist nur halb so groß wie bei einem normalen Motoranlasser und spart Geld und Platz in den Schalträumen “, erklärt Knud Rahbek. Das eingesparte Geld wird für den Kauf neuer energieeffizienter VLT®-Frequenzumrichter verwendet. Daher verursacht das neue Antriebskonzept keine zusätzlichen Investitionskosten, sondern spart tatsächlich Geld.
Dank dieses Konzepts spart Arla außerdem Kosten für die Konstruktion. Ein Ingenieur kostet 750 Dkk pro Stunde, während ein Elektriker, dessen Aufgabe es ist, die Antriebe zu montieren, nur 350 Dkk pro Stunde kostet. Laut Knud Rahbek haben die Elektriker von Arla die Vorteile der VLT®-Umrichter verstanden und wissen genau, wie sie sie effizient installieren und programmieren können.
Energieeinsparungen im Fokus
„Wir sind uns der Notwendigkeit bewusst, Energie zu sparen, da wir ein energieintensives Unternehmen sind. Dies ist darauf zurückzuführen, dass der Produktionsstandort mehr als 600 Motoren und Ventilatoren enthält. Die Arla Food Ingredients-Fabrik in Videbæk verbraucht jährlich rund 50 Millionen kWh Strom. Daher ist eine Einsparung von 10% bei den Energiekosten von enormer Bedeutung, spart viel Geld und verringert die CO2-Bilanz von Arla erheblich. Wir haben jedem Motor und Ventilator einen VLT®-Antrieb hinzugefügt, und auf diese Weise haben wir eine geschätzte Energieeinsparung zwischen 5-15% erzielt. In den nächsten drei Jahren planen wir die Installation von 100 weiteren Antrieben in neuen Projekten “, erklärt Knud Rahbek.
Die Antriebe steuern die Pumpen so, dass sie nur bei Bedarf und dann nur mit der erforderlichen Drehzahl laufen. Dies spart viel Energie, da die Motoren ohne Frequenzregelung kontinuierlich laufen würden. Die Drehzahlregelung anstelle der Ventilsteuerung reduziert dabei die Amortisationszeit für die Antriebe. Bei Filtereinheiten beispielsweise ergeben sich durch die verbesserte Temperaturregelung über Geschwindigkeits- und Durchflussregelung weitere enorme Energieeinsparungen. Das Werk verfügt über zahlreiche Filtrationsanlagen, da es in erster Linie darum geht, alle Bestandteile der Molke zu verwenden, die von der Käseherstellung übrig bleiben.
DrivePro® Servicevereinbarung
„Für uns ist es wichtig, eng mit Danfoss zusammenzuarbeiten. Bei einem Ausfall eines VLT®-Frequenzumrichters sind wir aufgrund des Servicekonzepts von Danfoss nach maximal 6 Stunden wieder betriebsbereit. Ersatzteile sind immer griffbereit und leicht zu beschaffen. Die enge Zusammenarbeit mit Danfoss bedeutet auch, dass unsere Mitarbeiter mit den VLT®-Antrieben bestens vertraut sind. Dies verbessert die Betriebssicherheit “, sagt Knud Rahbek.
Die Arla Food Ingredients Group hat mit Danfoss einen DrivePro®-Servicevertrag abgeschlossen, der die VLT®-Frequenzuumrichter über einen Zeitraum von 3 Jahren ab ihrer Installation abdeckt. Der Danfoss Service-Partner Styreg prüft die gesamte installierte VLT®-Basis und dokumentiert diese mit dem kostenlosen Danfoss VLT® Software Tool MCT10, sodass bei Warnungen oder Alarmen ein weiterer Ausfall vermieden werden kann. Außerdem werden alle Antriebsparameter heruntergeladen und die Antriebe werden physisch geprüft. Alles in allem bietet die Servicevereinbarung eine verbesserte Betriebszeit und reduziert die Anzahl teurer Ausfälle.
Hintergrunddaten
Das Werk der Arla Food Ingredients Group im dänischen Videbæk verbraucht jährlich rund 50 Millionen kWh Strom. Daher ist eine Energieeinsparung von nur 10% von enormer Bedeutung. 600 Danfoss VLT® AutomationDrive FC 302 werden in Größen von 0,37 bis 400 kW installiert. Zukünftige Projekte umfassen mehr als 100 Antriebe in den nächsten 3 Jahren.
Hier erhalten Sie weitere Informationen
Erfahren Sie mehr über den VLT® AutomationDrive FC 301/FC 302
Lesen Sie hier mehr über den Bereich Lebensmittel und Getränke